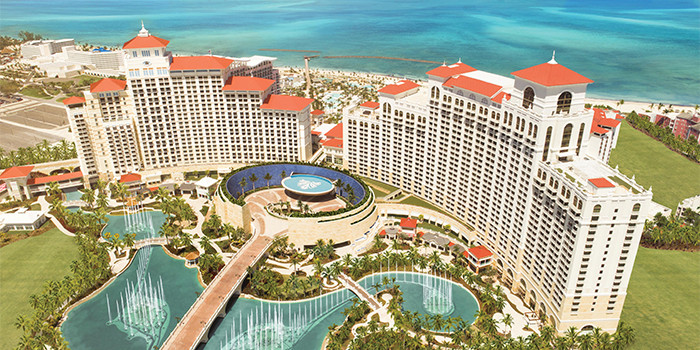
Coated in Luxury
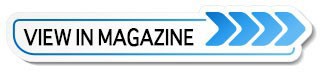
Spray Foam Magazine – Spring 2022 – Along the immaculate white sands of Cable Beach in Nassau, Bahamas sits the luxurious resort of Baha Mar. The resort has three oceanfront hotels, each offering stunning views, a grand selection of pools, a casino, and a luxe waterfront waterpark named Baha Bay. Imagine landing a job working on this spectacular resort? That’s exactly what happened to Gianvittorio “Toio” Mazzoni, owner of Island Spray Professionals, Ltd, based in Freeport, Bahamas. The Spray Foam Magazine team caught up with Toio to ask him about the specifics of the job at this oasis of a resort.
Gianvittorio Mazzoni completed his BS in Mechanical Engineering from Florida Tech in 2000. He then entered the spray foam industry following the 2004 hurricane season that brought destruction and disaster to the Caribbean, Bahamas, and South Florida. Mazzoni and his father originally purchased spray foam equipment to repair the roof of their own house after the storms. They realized that there was an opportunity to use their foam equipment for more repairs, and ultimately started a spray foam contracting business.
Fast forward 18 years and Island Spray Professionals Ltd landed three main jobs to complete at the Baha Mar resort. The crew had to ferry over their equipment as the resort was on a different island to their home base.
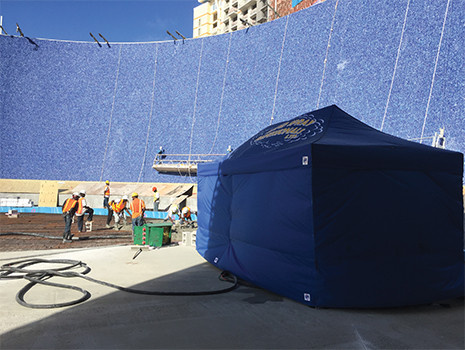
The jobs were waterproofing of the upper and lower basins of a water wall, installing insulation behind the water wall, and applying a floor coating in the mechanical rooms in a potable water tank which services the Baha Mar hotels.
Coating Application
There were several design changes on the water wall project. The original design was a full poured-in-place concrete wall, but this came up to be too expensive and would take too long. So, between the architects and contractor, they decided to do a steel stud wall with exterior sheathing.
The basics of the “water wall” as it is called, is one of the main features visitors see when visiting the resort. The slanted wall has trickling water over handmade glass tiles. It’s a true spectacle at night, as various water speeds produce sound effects along with actual sound and light. This feature consists of an upper and lower catch basin. Both basins are 100% polyurea coated, including all protrusions. The crew applied Versaflex FSS 45dc, VF20 and 30 to all the concrete coating applications. The basins were all poured in place concrete, and all the protrusions were either stainless steel that was blasted for profile on site or PVC piping and fiberglass reinforced angles.
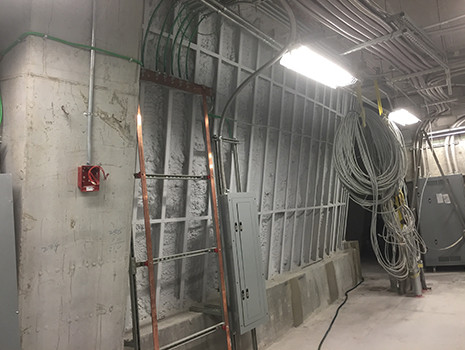
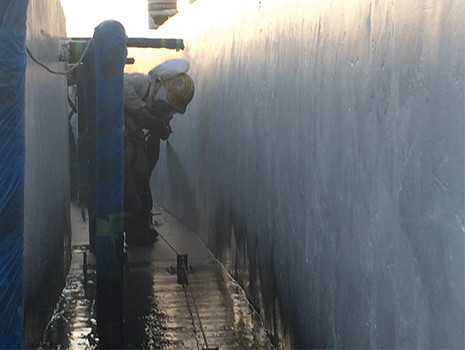
Island Spray Professionals Ltd. was brought in to the luxurious Baha Mar resort to waterproof the upper and lower basins of a water wall, install SPF behind the water wall, and apply a coating to the floor in the mechanical rooms in a potable water tank
The Island Spray Professionals crew’s job was to prep the concrete, prime, and then apply the polyurea at 100-120 mils. They tied in the upper and lower basins to the top and bottom of the wall with the contractor waterproofing the actual sheathing of the wall. Due to the front area wall’s design changing to a steel structure, they needed the back of the wall to be insulated, so the crew accomplished this with three to four inches of NCFI closed-cell foam topped with an ignition barrier. In the same area right behind the wall was a maze of pipework for both the plumbing and all the lighting that was involved with the wall. The crew then installed a full polyurea flooring with texture on all the mechanical rooms that have water pumps in them, which was essentially all of them.
In the first instance, the area was enclosed so the crew had a push/pull recycling the air and had full PPE including full Tyvek suits, Tennessee Chill Box, and full 3M masks for the workers in spray areas.
The polyurea went on all the flooring and curbed around the entire perimeter. Before applying the coating, the crew shotblasted the concrete, taped off all the pipes and pumps, and primed with an airless sprayer. The crew used their in-house custom-made aluminum powder coated mobile rig for the job. The rig contains a Graco HXp3, compressor, dryer,
lp/hp hoses, stick pumps and air dryer. It was basically enclosed with everything but the power, which was supplied by a Genset generator.
The waterproofing that the crew of six applied was twofold, with one primary waterproofing to ensure no water was lost through the basins, and the other for the mechanical rooms to prevent water from getting below.
The area under the entire water wall is 100% inhabited with high-end shops and restaurants, so the crew knew how important it was that the wall did not leak. Waterproofing both the water wall and the basins took them roughly six weeks to complete, which did not include the weather dependency or the standby time. The size of the basin with protrusions was 26,000 sq.ft. and the area of floor which needed coating was 5,500 sq.ft.
They also needed a mobile rig because when the contractors were pouring the floors, the Island Spray Professionals crew were applying the waterproofing. They therefore needed a crane to move equipment around when floor was not available.
Working at height in the top of the basin, there was a 100% tie off with the crew using yoyo’s (self-restricting lifeline) or safety ropes for their fall protection. The crew had to battle the rain, as the areas were exposed to the elements and meant to retain water, so whenever it would rain it would take a long time to get substrate prepped. In the lower basin, the drying process was a headache because the crew had to wait for the entire wall to dry or the water would cascade down the wall into the basin. However, the great part about using a polyurea coating is that there was no dry time. Once prepped, the crew could get spraying and get the job back into service within minutes.
The client was extremely happy with the results, so they brought the Island Spray Professionals back to seal a 6,200 sq.ft. full pour in place concrete potable water tank that supplies water to the hotels. The water tank was leaking after two other contractors tried to use a trowel to apply a cementitious coating and it failed. They required an NSF 61 potable water coating and then Versaflex Aquaverse was used as a topcoat. All the walls were hand scarified to get a profile on the wall and remove the existing waterproofing after the tank was drained, jet washed, then left for two weeks to dry with a dehumidifier installed.
After all the substrate and ambient parameters were met per Versaflex requirements, the primer was spray applied in three coats due to the concrete being very porous. The polyurea was then applied, the pins filled with urethane and poly applied again. It was a difficult job as the water tank was fully enclosed with only two manholes, so a hoist was assembled on top of the tank for emergency extraction, and there were temporary lights and power installed on the ceiling so as not to interfere with work on walls and floors.
Insulation application behind the water wall
The client chose SPF because they needed a material that would last the duration of the structure and in a humid environment would not wick water. The foam was installed behind 12,000 sq.ft. of wall space in the same rooms where the crew had sprayed the polyurea on the floors. The spray insulation job took approximately six days to complete with a crew of four present.
The substrate was concrete, there was DensGlass sheathing and steel studs. It was a new structure so there was minimal substrate prep. The crew did, however, use acetone wipes on all the steel studs, installed a dehumidifier to bring the dew down to get all condensate off the steel, and covered all pipes and pumps in case of any possible overspray. The crew then applied 2lbs of NCFI closed-cell foam at three to four and a thermal barrier paint for the ignition barrier.
In terms of any testing equipment, the Island Spray Professionals crew used a Elcometer moisture meter for the concrete and paneling, a Kestrel handheld for RH (relative humidity) and a Fluke infrared for surface temps.
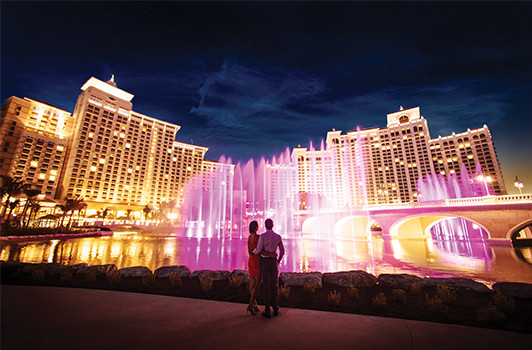
At night, the water wall and surrounding fountains create a spectacle of light and sound.
This job was a big accomplishment for any spray foam and coating contractor to undertake and accomplish with quality results. The crew at Island Spray Professionals, Ltd would like to say a special thanks to Steve and Josh Rice, Dudley Primeaux the late Jeff Downing, and Bob Browning of Bayside Builders, and CCA who was the overall contractor on the entire job. All were instrumental to the success of such a big project.
Visitors paying for an extravagant vacation expect the best in both service and surroundings. Island Spray Professionals have contributed to this high standard by keeping a grand water wall secure and leak proof.
To see our review of this fabulous resort to add to your vacation destination list, visit: https://www.inflorida.com/news/walking-on-a-dream-at-baha-mar/1058