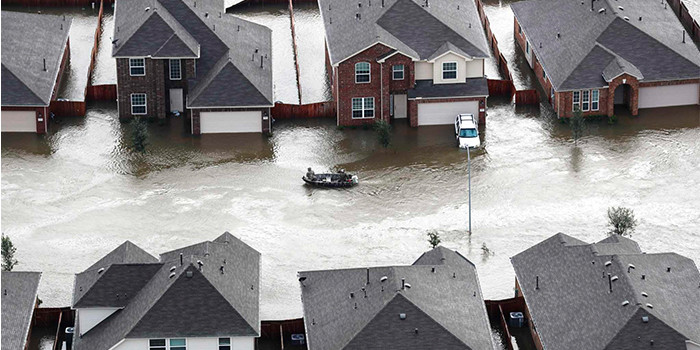
The Power of Mother Nature
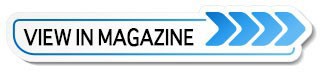
Spray Foam Magazine – Spring 2022 – Drive through any city or town in the country and you’ll see innumerable house and building designs built with a wide variety of materials and methods. This variety reflects the character of the region and under normal climatic conditions, our homes and buildings are weather resistant. That is, until Mother Nature wields her powers of water, wind, and fire.
Hurricanes, floods, and wildfires seem to be increasing in both number and intensity, and all three can more easily destroy our homes and buildings if they’re not constructed with spray foam. Hurricanes blow roofs off buildings built with vented attics. Heavy rains flood buildings, saturating the walls, floors and crawls, and wildfires burn down houses by igniting vented attics. Spray foam can prevent all this destruction and pay for itself as a bonus!
The folks in Miami-Dade County, Florida know a lot about hurricanes and wrote their building code to require the roof sheathing to be bonded to the attic framing and the framing to the walls. Spraying approved foam like SES SucraSeal or NexSeal (1/2-pound or 2-pound foams) to the underside of the roof deck satisfies both the wind uplift prevention requirement and the energy code for insulation. It’s a double win for the homeowner.
They say the three most destructive elements for our homes and buildings are Water, Water and Water! Spray foam helps to prevent migration of water vapor and moisture laden air, and SPF can act as a highly effective water-resistive layer in walls as well as a robust roofing system. But what if water gets around our roof and walls, flowing into the building through doors and windows?
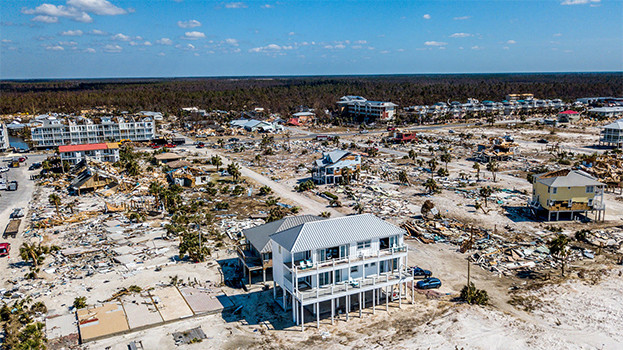
The spray foam in the attic of this concrete-walled house kept the roof on through Hurricane Michael in 2018
If the lower section of the building is insulated and air-sealed using closed-cell, medium density spray foam like SES NexSeal, the walls could be opened, dried and the sheetrock repaired in short order at a relatively low repair cost.
Back in the day when the global population was half of what it is today, we built on high ground and water naturally flowed down and away from homes. Homes were dry and most were more than 5’ away from each other! Climate conditions have changed, and we are reminded of it weekly, if not daily; 120°F in the Pacific Northwest or back-to-back snow years in Austin, TX. Just as the climate has changed, buildable land options have changed as well. There aren’t many buildable lots on a hill left. The affordable lots are at the bottom of the hill in the crosshairs of the next flood or rain event.
The high velocity winds of hurricanes make dramatic news stories, and the winds can do considerable damage, but more destruction caused by hurricanes is from ground saturation and flooding, not wind. Spray foam provides solutions for coastal climates that regularly face high winds and storm surge. Medium density spray foam is hydrophobic and protects against the flood and rain events as well the wind. Build as high as you can! Use piers when needed and use stem wall slabs to elevate the slab to a safer level above grade for reasonable protection from expected rain and flood events. When the waters do rise, medium-density foam will survive and help to save the rest of the structure.
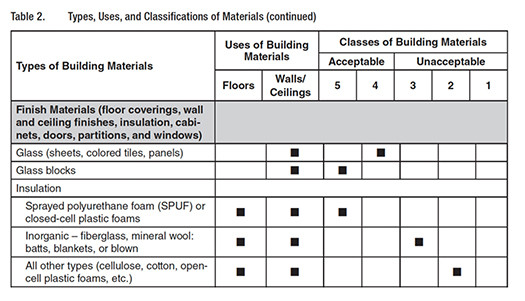
FEMA gives the highest rating to ccSPF but finds fiberglass and cellulose unacceptable for use in flood prone areas. Open-cell should also not be used where it could get wet
SPFA’s technical document titled “Flood Resistant Construction Using Closed-Cell SPF” is an excellent guide to best practice for building in flood zones. It cites work done by Claudette Reichel, EdD, director of LaHouse Research Center in Baton Rouge, and Joe Lstiburek, PhD, P.Eng, of Building Science Corporation on what they call the “Wash and Wear Building System.” Since closed-cell spray foam absorbs little to no water, even when fully submerged, the part of the walls subject to flooding should be sprayed. No fibrous insulation or low-density 1/2-pound foam should be installed in the area expected to get wet. If the house floods, the wet walls should be opened as soon as possible after the water recedes and the spray foam should be cleaned, disinfected then thoroughly dried. Not only does the flood water damage the walls and floors, but the water can also be polluted by nasty chemicals, sewage effluent and other toxic substances, so the need for cleaning cannot be overemphasized.
Once the walls are clean and dry, the closed-cell foam can be covered with the code-required 15-minute thermal barrier and the home or building reoccupied. This is immensely easier than removing and disposing of water-soaked fiberglass or cellulose insulation, and since the closed-cell foam is still providing thermal resistance (insulation) and controlling vapor diffusion during the cleanup process, the drying time is greatly reduced.
Mother Nature can throw more than just wind and water at us. Wildfires are erupting more often and are more intense than ever. Codes in Wildland Urban Interface zones require non-combustible exterior building materials like cementitious siding and low flame-spread roofing, but like flood water flowing in through doors and other openings, so can embers enter ventilated attics through eave or soffit vents. There are many examples of embers (aka fire brands) being carried for blocks to a house with open eave vents and starting a fire in the attic. Either low or medium density spray foam like SES SucraSeal, EasySeal or NexSeal can be sprayed to the underside of the roof deck and the eave vents blocked making it impossible for the embers to enter the home or building. Once again, spray foam is the solution to a potentially serious problem.
In 2021 in the U.S., there were 58,985 wildfires burning over 7.1 million acres and in 2020 over 10.1 million acres burned in about the same number of fires. 89,210 homes were lost from 2005 – 2020, and of those, 57,000 were between 2017 and 2020. The cost of U.S. wildfires for 2021 alone is estimated at up to $90 Billion. The main drivers of that estimate in years past have included the number of structures burned as well as the value of those structures and other infrastructure damage. Other factors include the large costs incurred by widespread electrical system shutdowns by utilities and the long tail of health impacts to people from wildfire smoke.
During these events, outdoor air quality is extremely unhealthy for hundreds of miles downwind of the fire. The air inside most non-spray foam homes and buildings is as bad as the outside since these structures are not airtight. By air-sealing the floors, walls and ceiling with spray foam, infiltration can be controlled, and the air can be filtered and cleaned. It’s only possible to achieve healthy indoor air quality if you can keep the outside air out and the inside air in. Spray foam wins again!
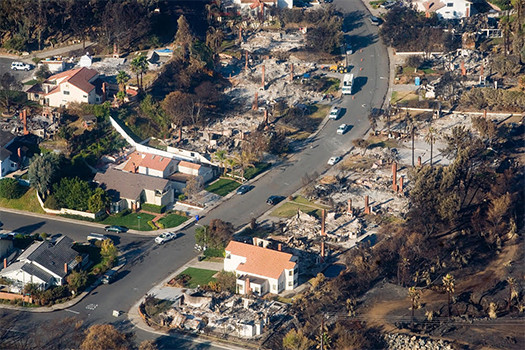
Wildfires can jump hundreds of yards due to embers igniting attic fires in vented attics. Houses with spray foam in unvented attics are far better protected.
For a spray foam professional, these are powerful selling points and so much more. Building effective water control, high-velocity wind control and fire prevention into our homes and buildings protects our families as well as our homes from these natural disasters. And, by the way, the foam pays for itself through energy savings too!
Contact SES Polyurethane Systems: If you’d like to learn more about FEMA and Florida hurricane code compliant foams from SES– Phone: 713-239-0252 // Website: www.sesfoam.com
*Spray Foam Magazine does not take editorial positions on promotional or sponsored; individual contributions to the magazine express the opinions of discrete authors unless explicitly labeled or otherwise stated. The inclusion of a particular piece in the magazine does not mean that individual staff members or editors concur with the editorial positions represented therein.