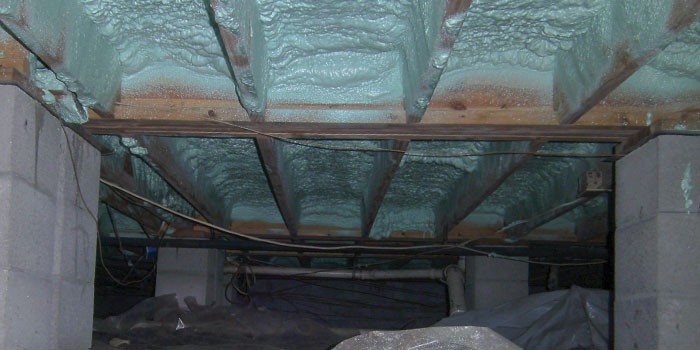
The Challenges Down Below
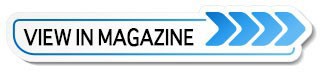
Question: What are some challenges when insulating a basement or crawl space with spray foam?
Answer: Basements and crawl spaces can benefit greatly from the application of spray polyurethane foam (SPF).
When installed correctly, spray foam can provide effective insulation, reduce air infiltration, stack effect, and reduce moisture drive into the living spaces.
It should be noted that these spaces also provide the greatest variety of design challenges for an SPF applicator. In order to insulate them properly you need to assess the temperature and humidity ranges of that climate zone, the design and materials of the existing structure, and how the homeowner uses the space. For example a crawl space can be enclosed with a dirt floor or open on all sides over a concrete pad. A basement can have a walk out door or be completely below grade. The foundation walls can be CMU, stone or poured masonry. A homeowner may have a radiant heating system installed or use the space for a laundry room. In the South, termites pose a challenge. Each of these factors must be considered and addressed. »
Protecting Against Moisture: Crawl spaces and basements tend to contain high levels of moisture from the ground. That factor can be further complicated by whether the foundation walls were adequately water or damp-proofed and if a ground water drainage system was installed.
Once you have gathered information then you have a couple of choices to minimize the potential for condensation in the space:
Provide additional ventilation and air circulation: This traditional approach works well in mixed climates that are not too humid, too cold, or too hot. Circulating air tends to have an evaporative effective on humid air. However, this approach may on occasion allow some moisture condensation on surfaces. Air circulation can be used to dry off the surfaces that condense.
Air-Seal and insulate the perimeter: A newer approach to the same subject is to completely separate the interior spaces from the exterior spaces. To accomplish this, you need to air-seal the crawl space and insulate the perimeter with a Class II vapor retarder insulation such as closed-cell foam. This area is not vented and becomes a semi-conditioned space typically within five to eight degrees of the interior temperature. It relies on the HVAC equipment to naturally provide semi-conditioned air from the interior to eliminate high humidity and the potential for condensation. A Class I vapor retarder is also added to the floor of the space.
In either situation, you would want to obtain hygrothermal modeling analysis of the proposed design to ensure your fix will actually work to its intended purpose.
Protecting Against Termites: After SPF is installed, it may be difficult for termite inspectors to detect the presence of termites. To address that issue, the Spray Polyurethane Foam Alliance (SPFA) developed a technical paper “Spray Foam Insulation and Termites.” The document discusses the types of termites, conventional methods of detection and treatment, along with two important spray foam application techniques to comply with existing building codes regarding termite inspection and treatment. The first method is to spray the underside of the floor. In this way, the termite inspector can very easily observe termite infestation in the wood framing below the flooring. The other way is to leave an inspection gap between the wall of the foundation and the upper flooring baseplate.
For more specific information, the document can be downloaded without charge at www.sprayfoam.org/technical/spfa-tech-tips. •
You may direct any questions concerning basement and crawl space insulation and any other questions regarding statements made in this article to Mason Knowles: 571-239-5221 | www.masonknowles.com