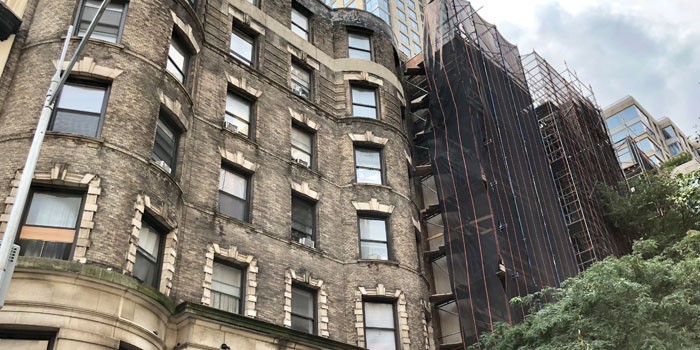
New York Minute
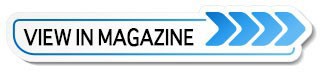
New York, New York! Dubbed the city that never sleeps, the center of the universe, and the concrete jungle where dreams are made of. In this concrete jungle lives hundreds of years of history and architecture that tells stories of its own by the style and décor that line the scores of streets that make up the Big Apple. While these commercial and residential buildings are enriched in culture, repairs are a still necessity to maintain living and working conditions for New York City dwellers.
Recently, two seven-story, mid-rise residential buildings located in the heart of Manhattan were in need of some TLC to keep the spaces energy-efficient, impermeable, and comfortable to live in. For the amount of money residents are paying to reside in New York City, you bet your bottom dollar, or rather top dollar, that the owners were going to choose the premium insulation material to fulfill those roles.
“In Manhattan, every bit of space counts, so with spray foam they were able to achieve an air barrier and thermal barrier on the exterior walls. Yet, since they had to square up the walls, the builders could only use a minimal amount of space for insulation to which spray polyurethane foam could fit,” states George Gray, sales and marketing manager of Coastal Insulation. “That’s where we came in.”
Due to the project’s location and the multiple crews that were coming in and out of the worksite daily, this was no simple task for the three-man Coastal Insulation team. As much as the men would have liked to complete the insulation job continuously, they were allotted only certain days of the week to go in and spray while other crews (plumbers, electricians, framers, etc.) were not on site in order to keep the premises safe for all parties.
Tackling one building at a time, the team used the same application process, materials, and foam to insulate the exterior walls for the entire project since the specifications and board footage were about the exact same in both mid-rises.
Starting from the cellar and working up, one floor at a time, the crew masked off the flooring, windows, and piping with polyethylene, and the electrical boxes with tape. As a safety precaution—in the case that another trade may show up without proper PPE and try to enter the floor they were insulating at the time—the crew put up warning signs and masked off the entry to the level they were actively working on.
Equipped with coveralls, full-face respirators, gloves, and monitoring boxes, the Coastal Insulation team was prepared each day to safely apply foam. The insulators sprayed the exterior walls of the brick substrate one and a half inches of closed-cell Lapolla FL 2000 4G foam with a Graco AP Fusion gun, a Graco E-30 Reactor, and a Graco T2 pump in the two cellars and 14 floors. Completing one floor a day, the crew finished the job in a total of 16 days throughout a month’s time.
“The work we have done at 350/346 W 71st Street has been a welcomed challenge. The coordination with other subcontractors has been handled daily to ensure a safe working environment for other tradesmen,” explains John Achille, vice president of Coastal Insulation. “Applying our spray foam to the exterior walls all the way up seven floors created coordination challenges. Add to that a single access point on a busy Manhattan street, we were stretched to the limit of our truck mounted equipment and 360 feet of spray hose. Suspending our hose in a safe manner was a daily task for the crew of three, but we managed to safely and efficiently complete the job. It’s always a pleasure when a customer understands our needs, so that we can best achieve their expectations.”
For more information on Coastal Insulation, go to www.coastalinsulationcorp.com. •