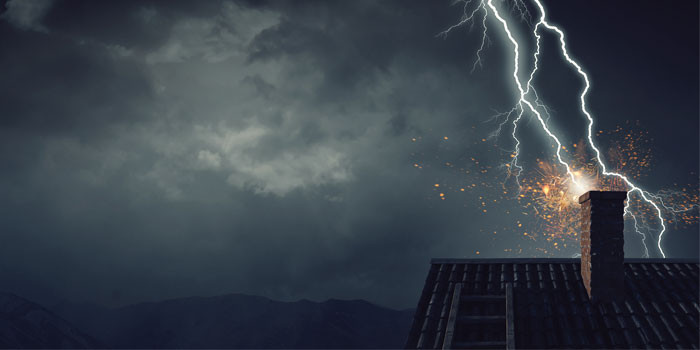
Spray Foam in Extreme Climates
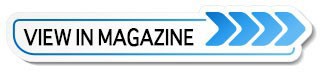
SUMMER ISSUE 2019 (Spray Foam Magazine) – There are places on our planet where average daily temperatures vary only a few degrees, it rains only enough to keep the landscape lush and green, and gentle breezes keep the air fresh and clean. Santa Barbara, Ecuador, Hawaii, and the west coast of Italy are among the most comfortable places in the world. Not surprisingly houses in these locations are often built without HVAC, insulation, and air sealing. They still need to keep rain water out, but even if it does get in, it dries quickly. Life is good. Most of us, however, live in parts of our country where the climate is more variable, and some of us live in areas where it’s downright extreme.
Heat, cold, rain, snow, humidity, and wind present serious challenges to our buildings and in the peak of intense storms, we often question our sanity and the choices we make to live where we do. We humans are a funny species and for whatever reason we make our homes in places where, without sound engineering, buildings are neither durable, nor healthy and comfortable let alone energy efficient. The good news is that we know what works and what doesn’t, and so as long as we pay attention to the First Principles of Building Science, we can build durable, comfortable, and healthy homes and buildings in any climate, regardless of how extreme it might be.
The three most common causes of building defects and unhealthy Indoor Air Quality (IAQ) are water, water, and water. Liquid water, vapor water, and frozen water are all potentially damaging, so we must control them if we expect our buildings to last. Luckily for all of us, spray polyurethane foam can be used as the primary control for all of these problems and when SPF is properly engineered and applied, the house or building can last for centuries, even in the most extreme climates.
Snow is easy to deal with as long as it stays frozen. Since most people don’t live where snow stays snow year-round, we need to prepare for it to become liquid and keep the water out of our structures. We have techniques for controlling snow melt so it doesn’t refreeze at the eaves causing ice dams, that can then cause liquid water to back-up into our roof system. There are many good articles about ice dams and how to prevent them (see Spray Foam 411 section from the Holiday 2018 issue of Spray Foam Magazine). Spray foam in the attic assembly is one of the most effective ways to prevent very expensive water damage.
Water vapor is insidious because like snow, it wants to turn into liquid water and it can do so in places where it’s nearly impossible to detect until it’s too late. Water vapor can diffuse right through many building materials which can be a benefit, but also potentially disastrous.
In extreme climates where it is very hot and very humid, or very cold and very dry, water vapor drive is in one predominant direction; from outside to inside in hot/humid climates and from inside to outside in cold/dry climates. In these situations, we need water vapor control in order to keep the vapor in a state as water vapor and not turn into liquid inside our building assemblies. Closed-cell spray foam does an amazingly good job of controlling vapor diffusion.
Condensation can occur when moisture-laden air contacts a surface colder than its dew point. There are many variables, but simply stated, if we keep the surface the humid air contacts warm, it tends not to condense. We do this by insulating with spray foam. This only works because spray foam is an air barrier material and since it is, the spray foam also controls air from passing through it. Moisture-laden air is the supertanker of water vapor transport, and in extreme climates, huge quantities of water vapor can be forced into our building assemblies where it can quickly change phase to liquid and destroy a home or building in only a couple of years. Both open- and closed-cell spray foams are air barrier materials and both can be used alone or with other control layers to keep a structure dry and healthy.
Driving rain from high-wind events is nearly impossible to keep from penetrating the cladding on our buildings. Some extreme climates regularly see ferocious winds with inches of rain per hour, and without a robust water resistive barrier under the cladding, the structural framing can get wet, which leads to rot, mold, mildew, and insect damage. Spraying closed-cell foam to the exterior of a building outboard of the sheathing is a brilliant way to build in any climate, and in an extreme climate it’s the only really intelligent way to protect the home and those who live there.
Spray foam also helps to hold roofs on houses in hurricane zones. Spraying foam into the rafter bays essentially glues the sheathing to the roof rafters. There is even evidence from Hurricane Michael in 2018 where open-cell foam held a metal roof in place. Since spray foam is a powerful adhesive that we froth up, it is understandable that it works as well as it does.
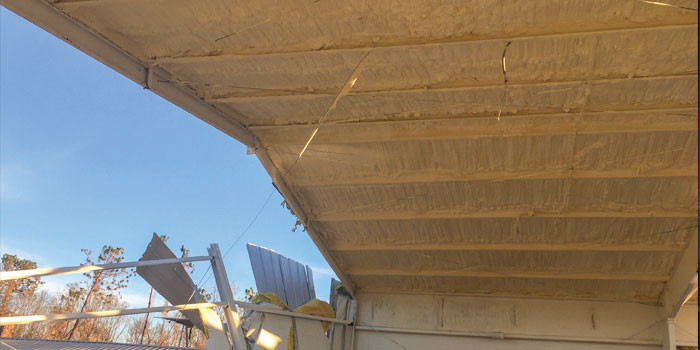
Open-cell spray foam in a Mexico City, Florida warehouse held the metal roof on this building during Hurricane Michael in 2018.
Where it’s really, really, really cold much of the year, spray foam is the most effective way to maintain indoor creature comfort. Think about the two most extreme temperatures in your daily experience–your water heater and your freezer. Both use polyurethane foam insulation and neither is more than an inch or two thick. Homes and buildings in the circumpolar regions of the world use spray foam as the go-to insulation and air seal for good reason. It works where no other insulation can, just like it does in your refrigerator and freezer. 80°F or 100°F difference in temperature from inside to outside? No problem for spray foam.
What about southern climates with three annual temperature ranges of hot, hotter, and hottest? Same idea as the frigid north—spray foam works better than any other insulation and air sealing method. It is continuous, fully adhered, and has extremely high R-value per inch. In thinner assemblies, it can even act as all four necessary controls–a water barrier, an air barrier, a vapor retarder, and as thermal insulation. Needless to say, any difference in cost of spray foam versus a cheap fibrous insulation is quickly returned through energy savings, and you get to keep the building because it won’t rot away from moisture damage.
And then there are floods where keeping water out of the building is impossible. FEMA recognizes the value of closed-cell spray foam in flood zones and approves it because it’s durable, cleanable, and doesn’t absorb water and the pollutants carried by the flood. Sure, the gypsum board will need to be removed and the foam surface must be washed and dried, but closed-cell foam won’t have to be removed and replaced like fibrous insulation.
Building durable homes and buildings in extreme climates requires careful attention to each of the First Principles of Building Science:
- Heat energy moves from high to lower
- Water moves from wetter to drier
- Air moves from higher to lower pressure
- Water vapor moves from higher to lower concentration
- Gravity acts down
If we don’t build robust assemblies to control problems associated with each of these First Principles, our buildings will not last. In extreme climates the rate of failure and cost to repair goes up exponentially.
Spray foam, with its high R-value, insulates to control the flow of heat into and out of our buildings. Water will find even the tiniest crack or gap to move from wetter outside to drier inside, but closed-cell spray foam is impenetrable to water. Wind can blow a gale, ripping at our roofs and driving rain right through our claddings.
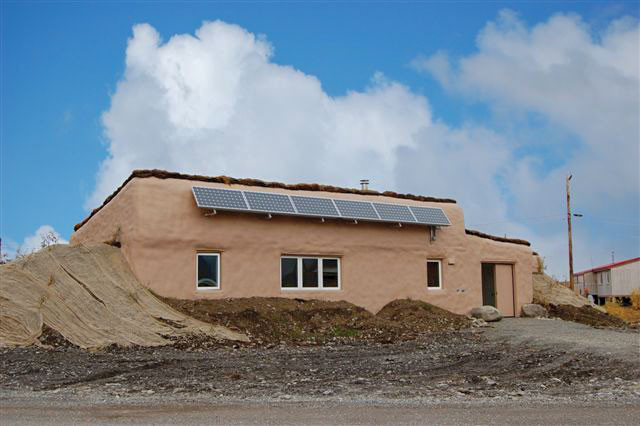
This house built in Anaktuvuk Pass, 150 miles north of the Arctic Circle used 8-sets of spray foam applied to the exterior with polyurea as the cladding. It uses less than 25% as much energy as the other homes in the community.
Spray foam is a powerful air barrier and since it fills voids, gaps, cracks and many other construction defects, it can save a building from near certain destruction. Water vapor diffusion can be a significant problem in extreme climates but closed-cell SPF is a strong vapor retarder and usually solves the problem without additional materials. Gravity pulls liquid water down and it also pulls fibrous insulation down. Not spray foam though. Both open-cell and closed-cell are fully-adhered and self-supporting so they do not settle, sag or shift over time. Closed-cell foam is also a water resistive barrier and sheds water extremely effectively.
Spray foam is the most valuable insulation and air sealing material for extreme climates, but not all spray foams are created equal. If water in any form is an issue, only closed-cell spray foam is the solution. If air sealing a building that is otherwise protected from liquid and vapor water, open-cell foam is arguably an even better air barrier material than closed-cell because it stays liquid longer as it’s sprayed in place. Open-cell tends to flow more easily into the smallest nooks and crannies yet it doesn’t have enough expansion pressure to move properly fastened framing members. Open-cell foam is also highly dimensionally stable.
Where it’s really, really, really cold, spray foam shines even through the darkness of winter. Some closed-cell foam works better than others, and SES NexSeal has proven performance under the most extreme real-world conditions. SES tested NexSeal for dimensional stability and R-value retention in Fairbanks, Alaska where it frequently dips to negative 40°F and lower. NexSeal is certified as Arctic Tested, Alaska Tough.
Sweltering heat, frigid and dry, soaking wet, howling winds, humidity off the charts. There are no weather-related building performance problems that can’t be solved using spray polyurethane foam!