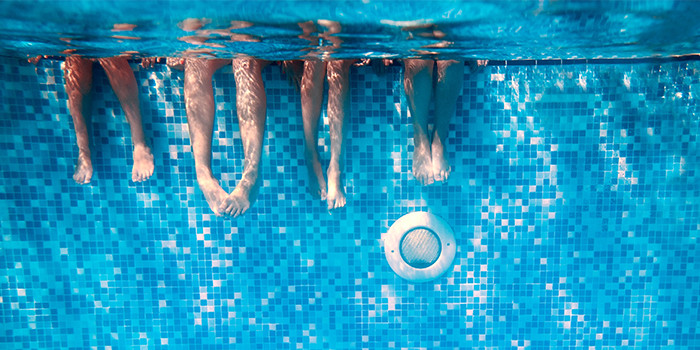
Splashing Into Pool Insulation
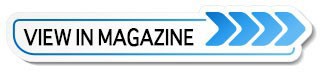
Spray Foam Magazine – Summer Issue 2021 – The clouds are melting away and the sunbeams are finally shooting through what has been a testing year for many. This particular pool and indoor swim spa with hot tub is located in Langley, BC, Canada and is sure to make someone’s summer extra special this year.
It’s commonplace to put in a pool in warmer climates like Florida, so the Spray Foam Magazine team was keen to find out about this pool project in Canada. The winters can be brutally cold there with snow, ice, and rain with the summers being warm and pleasant. Langley is a township with a collection of seven communities roughly 30 minutes east of Vancouver and additionally recognized as the Fraser Valley's wine country.
Owner of Newco Spray Foam, John Larochelle, is a veteran in theSPF industry with an impressive 40 years under his gun with Newco—installing batt, rigid foam board, and blown-in fiberglass insulation.
John’s son, Derrick, joined the family business in 2006 and started spraying in 2008 when he took the certification courses, and has now been spraying for 13 years. His dad is always there to offer advice, guidance and the occasional spraying assistance on a job.
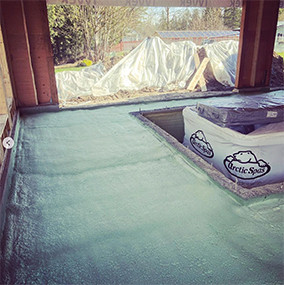
Newco Spray Foam landed a job to spray foam the concrete and gravel base of a pool with the client wanting to achieve the highest R-value possible in the smallest amount of space. The Newco crew worked alongside a builder on this particular job. Derrick said, “It was a pleasure working with Michael Koutnik from Koutnik Construction Ltd. As a builder he is always looking to stay a step ahead of others by constructing energy-efficient homes using superior products to deliver a high-quality home to his clients.”
The Newco crew loaded up their 20-foot cargo trailer, which was custom built by Pinnacle West, with a Graco Reactor 2 E-30 proportioner (260 feet of hose), Probler P2 Elite spray gun, and a 40kw Generator Air Compressor and Dryer and headed to the site.
Derrick Larochelle was the main sprayer on this project and made it clear that they take safety very seriously, “Our company is very safety conscious. We are a family run business and are always looking out for everyone’s safety. Our mornings consist of a Job Hazard Assessment on the project to identify the immediate hazards including fall protection requirements, other contractors, access/egress, ventilation and lighting issues etc.
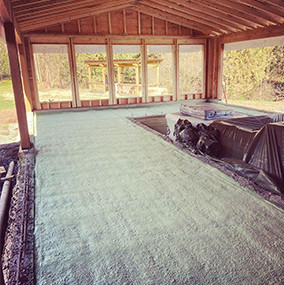
By installing SPF to the concrete and gravel base around a pool, one can hope to achieve the highest R-value possible in the smallest amount of space.
We also complete a daily inspection of all our PPE to ensure that they are in perfect working condition. Extra supplies are always on hand in case a repair or replacement is necessary. It is always our goal to introduce engineering controls as our first line of defense to reduce the risk not only to the workers within our company but all the other contractors on the job site.” Derrick wore a full-face respirator, supplied fresh air, long sleeve apparel, CSA approved steel toed boots and non-permeable gloves. His dad, John was his assistant and not in the immediate spray area, he wore a half-mask respirator with OV/P100 cartridges, long sleeve apparel, CSA approved steel toed boots and non-permeable gloves.
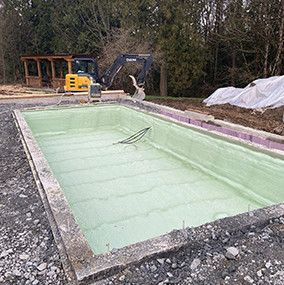
The reason this job materialized in the first place was that it was determined that in comparison to other materials such as Styrofoam board stock, including labor costs, spray foam was a superior product for both material value, R-value, and installation costs. The SPF was installed as per the Envelope Architects requirement for effective RSI value. This job was unique due to the client ordering a Blower Door Test to conclude and achieve airtightness. All the utilities in the pool house were electric, including the boiler for the radiant in-floor heat and pool heater. Both the Koutnik and Newco crew wanted to provide the client with the highest R-value possible to additionally ensure the most efficient use of energy.
The Newco crew sprayed SES Nexseal 2.0 CDN (HFO) to the 3,500 sq.ft. area in January 2021 when the weather was extremely challenging.
According to the crew, the ground was wet and cold, so not optimum spraying conditions and as the job was outside and not protected from the elements, the crew had to wait for a sunny day to begin spraying.
The crew noticed the gravel was saturated with rainwater and required heating to help with moisture levels. They therefore had to dry the gravel and concrete substrate with a propane tiger torch first to lower the moisture content and then allow for proper adhesion. Once the moisture levels were under control the job went very well with the crew applying two and a half inches and using two sets of foam, with the job taking a day and a half to complete. Derrick closed by saying, “This is the first time we have been able to use spray foam application on a pool project and we have since spoken with another pool contractor to do many more custom installations like this one.”
Diving into pool insulation with confidence, advanced application skills and using their preferred choice of product and equipment, this spray foam company’s dive into the deep end has paid off.