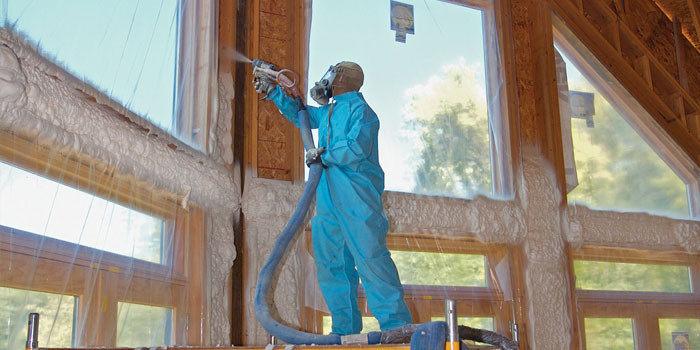
Ratio Assurance for SPF
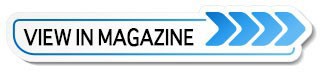
SUMMER ISSUE 2019 (Spray Foam Magazine) – As an insulation contractor, understanding the spray foam installation parameters including temperatures, pressures, and ratio are becoming more and more important. Builders, homeowners, and architects are more often now requesting spray foam as their choice for insulation. They have educated themselves on the process and are now asking for assurance the job is being installed correctly.
Being able to show proof that the job was sprayed on ratio enables you to deliver a more attractive bid upfront and offer peace of mind to the customer when the job is complete. Ultimately, that’s what Graco’s Ratio Assurance System provides—documentation to the customer in the form of ratio reports, which can be created directly from the Reactor mobile app that is connected to your Reactor 2 proportioner.
The Need for Ratio Assurance
The spray foam industry has grown due to the superior insulating benefits offered by the product, the push for homes and buildings to be more energy efficient, and new building codes requiring tighter more energy-efficient standards. The properties that make spray foam such a good insulator require it to be manufactured on-site, therefore it is essential to have the proper controls in place to assure it is manufactured correctly.
Properly mixing two components on-site requires professional equipment. Most spray foam chemistries today require a 1:1 ratio to mix properly and to obtain the optimal properties the material manufacturers design their chemistries to achieve. Spray foam, if misapplied, may cause issues that become hard and expensive to remedy. Having spray foam equipment that is designed to mitigate the risk of spraying “bad foam” is critical.
The system should have the capability of detecting possible issues with the equipment, process, and chemicals. It should also save and provide the data in a usable format should customers request this information. Graco’s spray foam equipment is designed to mitigate potential issues with a robust design and software that monitors and controls pressures and temperatures. It is also designed to alert the operator and shut down the machine if potential issues are detected. Many of the bad foam related issues are not due to equipment problems but rather things under the control of the insulation contractor, such as improperly conditioned chemical and using too large of a mix chamber for their feed system.
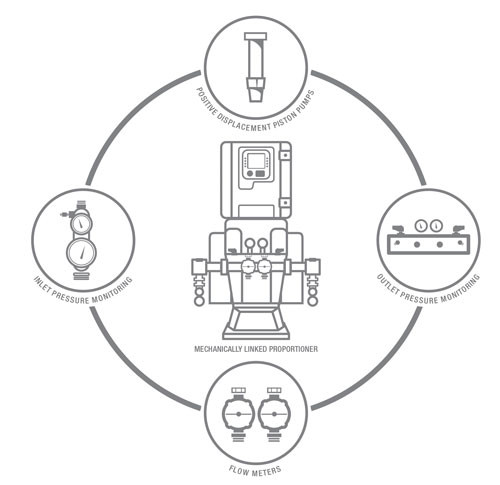
Ratio Assurance System
Single-Point Variables
It is important to understand the types of issues that may cause off-ratio foam to be sprayed. These types of issues are called single-point variables. Single-point variables can fall into six main categories.
By understanding the different single-point variables, detection methods can be designed for each. Once the variable type can be detected, it can be monitored. The goal is to monitor each of these variables and shut the proportioner down if one is detected, thereby preventing off-ratio foam from being sprayed. The operator can then make updates or perform necessary maintenance to eliminate the issue causing the off-ratio condition. There are a number of individual single-point variables that may cause off-ratio dispensing. There isn’t one method that is best to detect all possible issues, so it is important to have a robust multi-tiered ratio assurance system that incorporates both pressure and flow meter monitoring.
In order to minimize the frequency of being shut down for some off-ratio conditions caused by feed pump issues, Graco has developed new software for Reactor 2 electric models called “Reactor Smart Control.” Reactor Smart Control mode will automatically make adjustments to the Reactor to attempt to prevent off-ratio dispensing.
Graco’s Multi-Tiered Ratio Assurance System
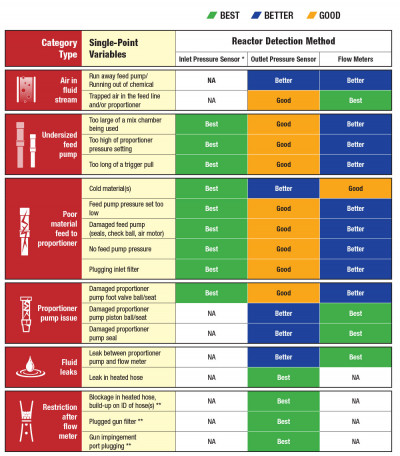
Single-Point Variables
A robust ratio control system must be multi-tiered and more than just flow meters. The foundation of the system starts with mechanically linked pumps and then adds positive displacement piston pumps, pressure monitoring, and flow meters to provide a ratio assurance system with built in redundancies. This will provide unsurpassed results in detecting off-ratio conditions.
Mechanically Linked Pumps
At the foundation of every Reactor are mechanically linked pumps. This includes the pumps on all electric, hydraulic, and pneumatic Reactors. The term “mechanically linked pumps” simply means that both the A and B pumps are connected together either with a shaft or a yoke so that both pumps stroke evenly at the same rate. By mechanically linking the pumps each time the A pump is cycled, the B pump must also cycle. This forces the pumps to cycle evenly and equally resulting in the pumps wanting to pump on-ratio. Graco has always believed that mechanically linking the A and B pumps provides a robust system designed for 1:1 ratio spraying.
Positive Displacement Piston Pumps
The type of pumps used for spray foam and coating applications is also important. Positive displacement piston pumps are a proven design that Graco believes is the best type of pumps for this application.
They provide consistent volumetric performance over a large range of temperatures, pressures, and viscosities. Piston pumps are more accurate for use in start and stop applications and for maintaining stall pressure. Piston pumps can maintain accurate volume per cycle over long periods of use even with aggressive fluids.
Graco’s piston pumps are precision machined with state of the art CNC machining equipment. They are held to very tight tolerances assuring consistency from pump to pump. This is important when depending on two pumps in a system for equal volumes of material. Graco’s tolerance between pumps is held to less than 1%.
Inlet Pressure Monitoring
Monitoring changes in inlet pressure is a quick and reliable way to detect certain potential off-ratio causing issues. Inlet pressure monitoring is a standard feature on Reactor 2 elite models.
Inlet monitoring is the best way to detect most feed pump and material feed related issues. By monitoring when inlet pressure falls below an acceptable pressure, a problem can be detected and the user alerted. Although flow meters and outlet pressure monitoring may also be able to detect feed related issues, inlet pressure monitoring is the most accurate and quickest responding method of detection.
Some of the most common ratio causing conditions including running out of chemical, cold chemical, or the feed pump(s) being undersized for the required demand are all best detected using inlet pressure monitoring.
Outlet Pressure Monitoring
Outlet pressure monitoring is standard on all electric and hydraulic Reactors. Graco has always used the pressure differential between the A and B chemicals as a way to detect and prevent off-ratio spraying. Reactors have a pressure differential alarm default setting of 500 psi (customers have the option of changing this value to best suit their needs). Once the pressure differential between the A and B chemicals exceeds 500 psi the Reactor will shut down. Using pressure monitoring has always been the way to detect the majority of off-ratio conditions. Although this rule of thumb works in most cases, there are exceptions.
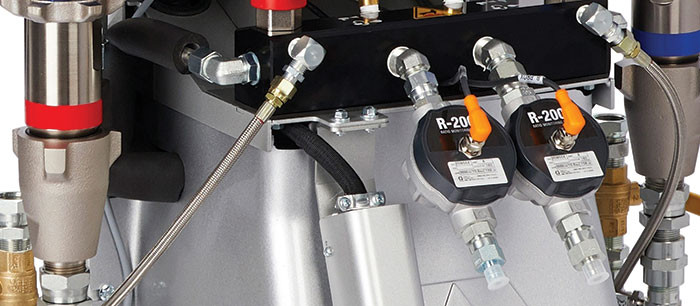
Reactor 2 E-30 Elite with Flow Meters installed (Flow Meters ship with all new Reactor 2 elite models and retrofit kits are available for current Reactor 2 models.)
Flow Meters
Flow meters can detect certain conditions that may cause off-ratio dispensing that may not be caught using inlet or outlet pressure monitoring alone. Flow meters are best at detecting issues related to the proportioner pumps, air in the feed lines/system, and some fluid leaks. Adding flow meters to the strong Reactor foundation of mechanically linked positive displacement piston pumps and inlet and outlet pressure monitoring provides an additional level of ratio assurance protection to the system.
Flow meters tie the complete system together with the ability to measure, monitor, and record true volumes of the A and B materials. By knowing the true volumes dispensed, this data can be made available to the customer.
Competitive Advantage
Having the right equipment to monitor and detect possible issues and having the ability to collect the required information to provide proof of installation is important. A contractor that understands the potential issues, knows how to minimize the occurrence of these problems, and knows how to quickly resolve them, will set themselves apart from their competition.