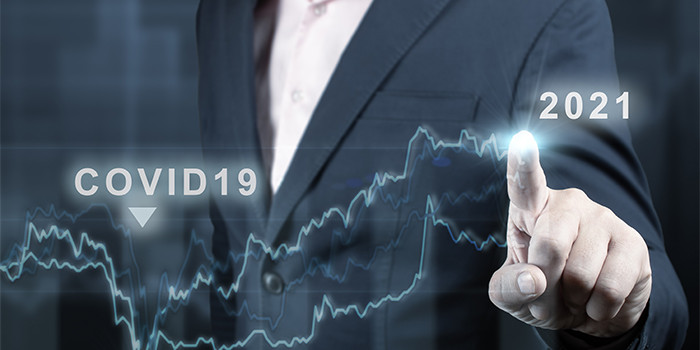
Mid-Year SPF Industry Outlook
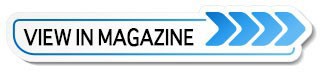
Spray Foam Magazine – Summer Issue 2021 – As we enter the second half of 2021, what are your thoughts on the overall state of the spray foam industry?
Simon Baker: We are facing some challenges, however it’s not all bad. Market demand is very strong, driven by surging new home construction. 1.7 million housing starts were announced last month in the U.S. The energy efficiency focus and the stimulus package also fare well for spray foam. These dynamics are positive. However, the industry must catch up to meet the demand. There are some challenges to overcome including materials shortages, pandemic impacts and labor availability.
Are you seeing improvements in the industry with the rollout of the vaccines?
SB: HBS operated during the pandemic and our folks were on the road visiting customers throughout. Restrictions made their day-to-day business challenging, however, now a lot of the population are getting vaccinated, confidence is growing.
Additionally, rules surrounding social distancing and getting onto job sites are easing. It’s becoming easier to conduct business all around.
Do you feel that the pandemic has changed the ways contractors are conducting business? If so, how?
SB: We know contractors to be a robust and practical group of people. From what we’ve seen over the last year, they’ve generally tried to continue to conduct business as usual, while respecting their regional mandates. They have really tried to do their best considering the circumstances.
Material shortages are on everyone’s mind. What can you tell us about the cause(s) of the issue and possible timing of resolution?
SB: This issue dates back to 2020. There have been a series of events that combined to create a perfect storm. At the end of 2020, MDI went into tight supply. A number of U.S. suppliers struggled with maintenance and materials in their plants, slowing production during heightened demand.
We also started to see port congestion. Surely many people have seen photos of all of the ships waiting offshore at the Ports of Long Beach and Los Angeles. The backlog is driven by everybody at home, during the pandemic, ordering everything from new furniture and entertainment to any number of consumer goods. Many of these items are imported and demand has jammed up global supply chains. At various points, we have seen anywhere from 30-40 vessels offshore waiting to be unloaded. The infrastructure in LA and Long Beach can’t cope with it. They are working hard to clear vessels, but sheer volume is in the way.
Additionally, the winter storm Uri hit Texas hard in February. I live in Texas and was amazed at how quickly it hit and how cold it became. Texas is used to warm weather and a lot of the petrochemical plants are based here. Unfortunately, they weren’t prepared for the storm’s intensity. It only lasted a few days, but the ramifications were huge. A number of suppliers declared force majeure, meaning they were unable to fulfill contractual supply obligations. Some force majeure declarations are still in place and we are struggling to get the raw materials that we need to keep the industry going.
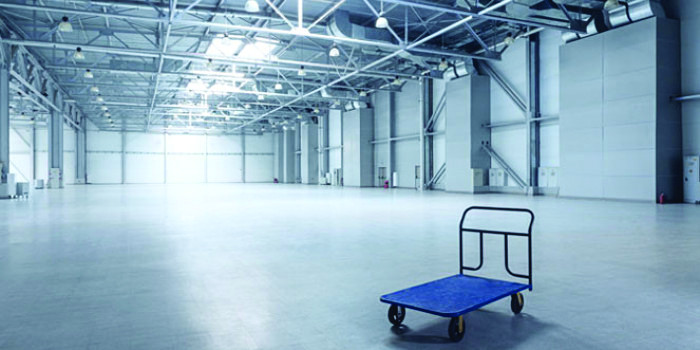
There are serious impacts across the whole polyurethanes world, not just spray foam. Car manufacturers are struggling to manufacture their seating. Mattress producers are also under pressure.
Midway through the year we are still unfortunately tight on raw materials and we are doing our best to keep customers supplied.
How is HBS currently assisting its contractors during this time?
SB: We are trying to be as fair as possible and doing our best to keep customers going by spreading product across as many contractors as possible. You might not be able to place a huge order, however we’ll supply you with smaller amounts on a regular basis to keep you going.
We had a brief disruption in our production in Arlington, Texas during the winter storm and were down for about three or four days. However, we kept our plants running throughout the pandemic and the supply crisis. Ultimately, we’re doing everything we can to keep product flowing. We are also communicating openly about the situation so customers can plan ahead and make the best decisions for their respective businesses.
Our transparency is also helpful as we communicate with customers about price increases. Nobody likes increases; however, they are inevitable from time to time. Today they are occurring across numerous construction materials, not just spray foam. The price of lumber, shingles, and piping are all climbing. We try to be as open about pricing as possible, giving contractors sufficient notice so they can plan ahead on their end.
What areas of construction do you feel are driving demand for spray foam today?
SB: New build residential is driving a lot of demand. We are seeing demand from public works projects like schools. Commercial is harder hit by COVID, as offices and hotels sit vacant. In roofing today, demand for spray foam is driven by retrofits. Roofing season is starting, and many are fixing existing roofs.
The U.S. is once again on track to shift spray foam to HFO-based solutions. What should contractors know about this?
SB: The shift to HFO-based spray foams is happening and it’s internationally driven. January 1st in Canada, the move away from HFC SPFs became an official mandate as HFO options have a much more benign impact on the environment.
In the U.S., seven states have adopted HFO, and you can no longer use HFC systems there. Additionally, the new administration is focused on the environment and we wouldn’t be surprised if federal legislation is on the horizon.
The good news is that HBS has developed an HFO solution that works well and receives positive reviews. Demand for it is high in states not yet mandating HFO spray foam. Unfortunately, the HFO product has been somewhat affected by the supply shortages so it’s a bit challenging at the moment but we are working with the supplier to get through that. We anticipate normal service will resume by the end of the second quarter.