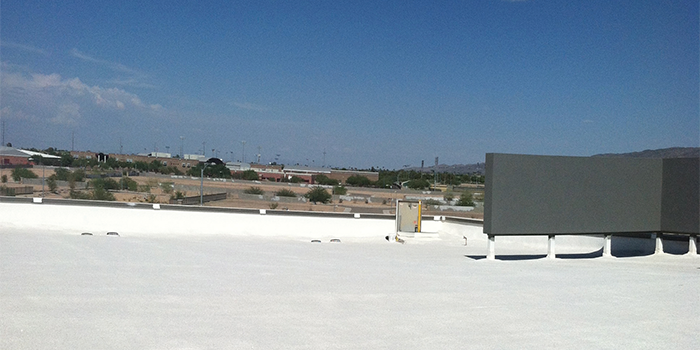
Roofing Lifespans Unveiled
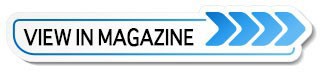
SPRAY FOAM MAGAZINE – The last 30 years have brought amazing advances in commercial roof technology. New products, processes, maintenance schedules, protective coatings, and more should have roofs lasting longer than ever before. However, while warranties have indeed increased from 5 years to 10 years to
15 to 20 and even 30 years, commercial roofs are replaced, on average, every 10 to 15 years. This is the same lifespan as 20 to 30 years ago.
Spray polyurethane foam roof systems consistently average over 20 years before replacement. I have personally installed SPF roofing systems in the 1970s that are still performing today.
This article discusses the real costs of membrane roof systems compared to SPF roof systems over 30 years.
Life Cycle Cost Analysis
In 2000, the Spray Polyurethane Foam Alliance (SPFA) hired Michelson Technology LLC to conduct a life cycle assessment of SPF roofing systems to compare them to conventional membrane insulated roofing systems. The study was conducted by Dr. Theodore Michelsen, former Executive Director of the Roofing Industry Educational Institute (RIEI). The study was conducted in accordance with ASTM Standard ASTM E 917 - 02 “Standard Practice for Measuring Life-Cycle Costs of Buildings and Building Systems.” Dr. Michelsen used a 20,000 sq.ft. roof as a basis for comparisons.
The results showed Spray Polyurethane Foam having a 30-year life cycle cost advantage over membrane roofs from a low of 12 percent using a six-year recoat schedule to over 59 percent for a SPF system that is recoated on a 15-year schedule.
2023 Updated Data:
What about today? Using prices reported in the 2023 edition of the Building Construction Cost with RS Means data* and validating the prices reported in the “Estimator” by a survey of roofing contractors across the country and websites such as RoofCalc.com, the authors were able to develop cost comparisons that showed significant differences.
*RS Means data for TPO membranes, acrylic and silicone coatings was incomplete for the purpose of this analysis. The tables displayed above were completed using information provided by various manufacturers, roofing contractors, and then compared with websites such as RoofingCalc.com. Costs did not include details such as flashing, gutters, etc.
After crunching the numbers, costs of membrane roofs to SPF roofs had increased on the low end and came closer on the high end. The membrane roofs averaged a premium of 23 percent to 42 percent over SPF roofing depending on the type of system. It should be noted that SPF roofing systems costs were calculated at two-inch thickness providing an R-value of 13 while the membrane roofs were calculated with no insulation.
Code Required costs of Insulation
However, recent building codes require a significant amount of insulation for new roof systems—from a low of R-20 to a high of R-40. When R-28 ($4.28/sq.ft.) is added to the systems, the 30 year costs skyrocket, often more than doubling the cost of a membrane system each time it is replaced.
It is not only added insulation that increases the costs. Tear-off at the 10 and 15 year intervals ($1.97/sq.ft.) significantly raised the 30-year costs of the membrane systems, ranging between $39,400 for a 15 year system to $78,800 for a 10 year system.
Added insulation costs, plus tear-offs, increase the 30 year costs of membrane systems from a low of $392,000 to a high of $505,000, compared to a SPF roofing system with R- 28 that can range from a low of $192,600 to a high of $224,800 over a 30-year lifespan.
The cost data shows that membrane systems insulated to recent building codes cost 90 percent to 250 percent more over a 30-year lifespan than a SPF roof system. These costs expand considerably if the membrane roof is replaced at the 10 year mark.
Why does SPF Roofing cost less over 30 years?
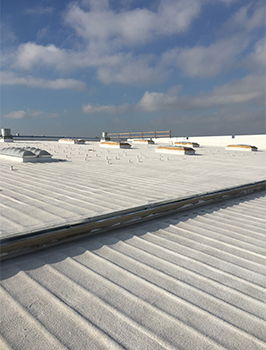
The data shows insulated membrane systems costing from close to one to two and a half times the cost of a SPF roof system over 30 years.
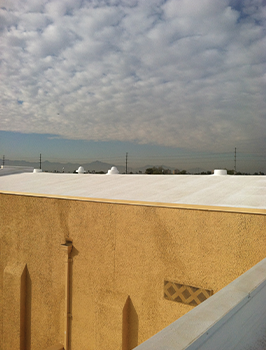
No Tear-off and Replacement:
The main reason SPF roofing systems cost less over a 30 year timeframe is that the roofs don’t require a tear off if installed and maintained correctly. Spray polyurethane foam (SPF) does not age over time, but it can deteriorate from UV exposure. So long as the foam is protected from the sun, the physical properties of SPF remain consistently the same.
In 1997, and again in 2003, Dr. Rene Dupuis of Structural Research Inc. was commissioned by the National Roofing Foundation to conduct research on SPF roofing systems in six different climate zones in the United States. Based on inspections and sampling of over 300 SPF roofing systems, Dr. Dupuis concluded that SPF roofs have an effective service life of more than 30 years. The research also shows that the physical properties of the foam change very little with age. This indicates that the life expectancy of an SPF roof system depends primarily on the original application and long-term maintenance.
In the first study, Dupuis reported the average service life of the SPF roofing systems before recoating was 11 years. In the subsequent study in 2003, the average recoat cycle had increased to 15 years. Based on the results of the 1997 study, Dr Dupuis reported “SPF Roofing Systems are one of the most sustainable systems to date.”
No Need to Replace Insulation
R-value for new and replacement roofing have increased every building code cycle in the last 15 years. The newest building codes call for increasing R-value on recovery systems as well.
R-value requirements vary from state to state. The lowest are in Louisiana and Arkansas with an R-value requirement of 20, while the highest are in Alaska and Vermont with an R-value requirement of 40. The mean R-value across the U.S. is 28. For the purposes of this article, R-28 is used for new roof systems.
R-28 would require four inches of polyiso insulation board. According to RS Means, four inches of polyiso insulation board installed would cost an average of $4.28/sq ft.
Environments Costs
Raw Material Extraction, Processing and Disposal:
According to the National Roofing Contractors annual surveys, more than 68 percent of the low-slope re-roofing market included tear-off and replacement of the existing roof membrane.
The amount of debris from a 20,000 sq ft roof tear-off ranges between 10 and 20 cubic yards of material. All that material must be not only disposed of in landfills, but new materials extracted and processed for the new roof. The environmental costs of energy to extract and process raw materials combined with the depletion of resources are enormous if roofs are replaced every 10-15 years.
Conclusion
As building codes require more insulation on roofs and the cost of materials and landfills goes up, the difference in costs over 30 years between membrane roofs and SPF roofs has become greater. The data shows insulated membrane systems costing from close to one to two and a half times the cost of a SPF roof system over 30 years.
For use by SprayFoamMagazine.com & Spray Foam Magazine