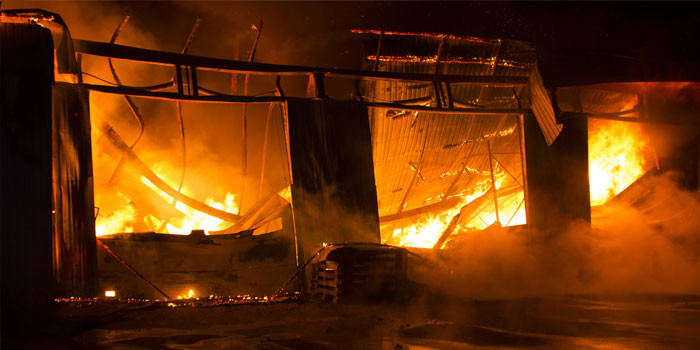
Meeting Fire and Life Safety Goals
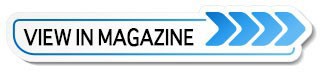
Spring 2020 – Spray Foam Magazine – Fire and safety codes are essential to the welfare of everyone who lives or works in any kind of structure. How codes and tests change and develop is due to material innovations, research and unfortunately learning from mistakes and tragedies of the past. These tragic events happen if codes are ignored or a new issue is discovered through a catastrophic event.
The Station nightclub fire occurred on February 20, 2003 in West Warwick, Rhode Island. The fire killed 100 people with many of the survivors left injured either from burns, smoke inhalation, thermal trauma, or trampling. This horrific fire was caused by pyrotechnics being set off, during the rock performance, which then ignited two layers of an acoustic foam, an outer layer of urethane foam sprayed over a base of polyurethane foam which had been crudely applied on the walls of the venue. It should also be noted that the building was required to have a sprinkler system, but this was not in place.
The manufacturers of the foam settled out of court for $25 million and the state of Rhode Island and the town of West Warwick for $10 million. Owners of the nightclub were also charged with involuntary manslaughter. Fire and safety codes were greatly improved after this terrible incident and within weeks of the disaster, an emergency meeting was called for the National Fire Protection Association (NFPA) committee handling code for “assembly occupancies.”
This resulted in Tentative Interim Amendments (TIAs) being issued for the national standard “Life Safety Code” (NFPA 101) in July 2003. The TIAs required automatic fire sprinklers in all existing nightclubs and similar settings that accommodate more than 100 occupants and all new sites in the same categories. The TIAs also required extra crowd manager personnel. These TIAs were subsequently incorporated into the 2006 edition of NFPA 101, along with additional exit requirements for new nightclub occupancies. Since these changes, every state and or local authority is to legally legislate and enforce current code changes.
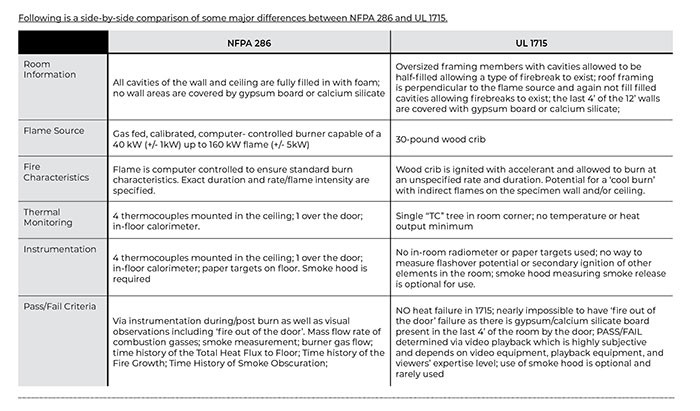
It is therefore imperative for tests and comparisons to still be investigated to limit future catastrophes.
Contractors who install materials have a duty to make sure the applications they install follow specifications appropriate to the updated codes and standards. Engineers, architects, and other design specialists need to keep in touch with any comparison tests or codes and implement these in their designs. To ensure fire codes and safety standards are always being re-accessed and improved, it is imperative to compare testing methods.
Jensen Hughes, a global leader in safety, security, risk-based engineering, consulting, and codes and standards revisions have recently highlighted the engineering comparison between testing to NFPA 286 vs UL 1715, highlighting 11 major differences between the two methods. Everyone in the spray foam industry must be aware of these tests, whether they are a manufacturer or a contractor. The tests not only provide an indication of the materials reaction to fire and intense heat, but these answers are needed to help product development and answer contractor and even consumer questions on spray foam safety.
Existing building and life safety codes specify that interior materials undergo a room corner fire test, before being adopted for use. The codes allow for two different standardized test methods.depending on the application. Jensen analyzed the NFPA 286 and UL 1715 tests. There are a number of variances between the two with the outcomes not exactly the same for certain materials. The tests were both carried out in an enclosed room with a single door, with the walls and ceilings being covered with an interior finish material.
Jensen Hughes made the conclusion that NFPA 286 provided a significantly superior fire test than the UL 1715 for the measurement of flame and fire growth of materials within a compartment. The ignition source, compartment geometry, and sample configuration of the NFPA 286 test facilitate a more severe thermal environment than that of the UL 1715 test. Furthermore, the NFPA 286 test provides significantly better quantitative measurements for heat release, flashover and smoke generation. These measurements provide the basis for the pass/fail criteria required in the codes and standards. The UL 1715 provides information based solely on observations made during the test and/or from photographic data. It should be noted that these observations can be highly subjective and may not be consistent from test to test.
The conclusion of this investigation highlights an issue which needs to be addressed by everyone in the spray foam industry, why accept the overwhelming reduction in life safety or place your company in a position where your liability is open to a “Subjective Review?” The massive increase in accountability and ultimate hazard provided to the industry by supporting a low benchmark “Subjective” UL 1715 Test Method, when a superior overwhelmingly demanding NFPA 286 test exists, is illogical for business owners and the industry as a whole.