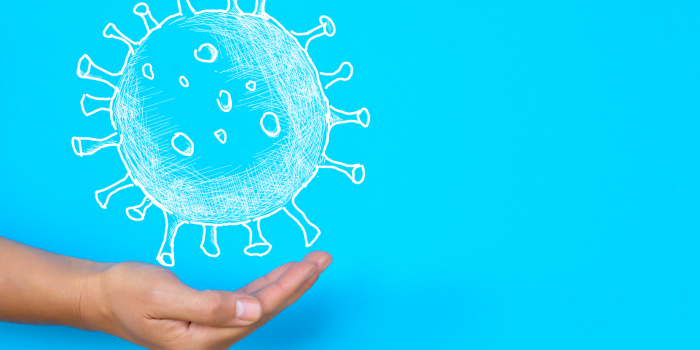
Prevent Contamination in Your SPF Equipment
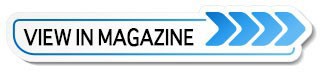
SPRAY FOAM MAGAZINE – Spray foam professionals, are you inadvertently contaminating your materials without realizing it? In the world of spray foam insulation, vigilance is key to ensuring consistent and reliable results. One often overlooked aspect is the potential leakage of seals or check balls in your transfer pump, leading to contamination issues that may go unnoticed until it’s too late.
Typically, when seals or check balls in the transfer pump start leaking, the fluid that seeps out can flow back into the drum without being visible to the operator. This issue might not seem problematic initially, especially if the pump can maintain the required output for the equipment. If you’re consistently using the same material, a small leakage might not raise immediate concern.
However, the real trouble begins when you switch between different products. The leaks from previous use can contaminate the new material, unbeknownst to the operator. Even attempts to drain the pump by engaging the bottom check ball may only remove fluid from below the bottom seal, leaving the material above the seal susceptible to contamination.
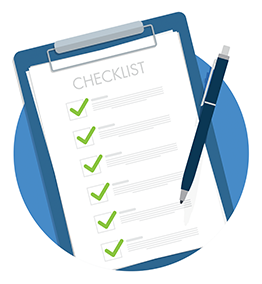
To mitigate this risk, it’s highly advisable to proactively replace pump seals and the lower check ball every six months. This preventive maintenance routine can significantly reduce the potential for cross-contamination between materials and ensure the integrity of your spray foam applications.
Regularly inspecting and replacing seals and check balls in your pump is a crucial step towards maintaining the quality and effectiveness of your spray foam projects. Additionally, thorough cleaning of equipment and pumps between material changes is imperative to ensure that no residual material or contaminants remain, further safeguarding the quality of your work.
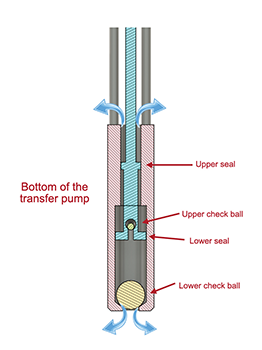
By being diligent and proactive in your maintenance practices, you can uphold the highest standards of quality in your spray foam applications, avoiding potential material contamination and the associated challenges it can pose. Keep your equipment in top-notch condition to achieve optimal performance and deliver exceptional results with every spray.
About the Author: Ken Anderson is currently the Technical Director for Profoam. After a career in engineering, Ken started a successful spray foam contracting business. Eight years later, he transitioned to tech service, helping other contractors be successful in their businesses. Ken has been with foam distributors and foam manufactures gaining experience along the way and has been with Profoam for the last three years.
For use by SprayFoamMagazine.com & Spray Foam Magazine