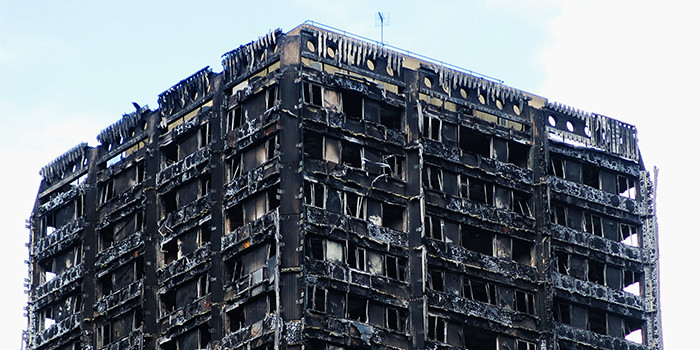
High Standards
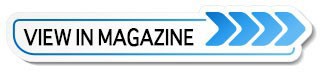
Author’s Note: An ongoing investigation into the Grenfell Tower tragedy in London, UK includes sensitive material; we have therefore decided to leave out specific names associated directly with this inquiry.
Spray Foam Magazine – Summer Issue 2021 – The Grenfell Tower is seen as one of the UK’s worst modern disasters, which could and should have been prevented. This tragedy has resulted in a proposed adjustment for UK Construction, in particular the effects that the delivery of an air gap can have in a structure.
The materials installed in Grenfell have since been under much scrutiny and the Spray Foam Magazine team wanted to investigate why and how such a disaster happened and could such an event ever happen in the U.S.
On June 14, 2017, a fire broke out in the kitchen of a fourth-floor apartment in a 23-level tower block in North Kensington, West London. The tower was built in 1974 as council housing (the equivalent of U.S. public housing) and underwent a multi-million-pound refurbishment from 2015 to 2016 where the cladding was replaced.
The fire was believed to have started behind a fridge-freezer in a fourth-floor apartment and took only a few minutes for the fire to shoot up the exterior of the structure and engulf all four sides of the tower. The fire escaped into the cladding through gaps which opened up around the kitchen windows due to the materials rapidly distorting in the heat of the fire. Two hours after the fire started, the upper floors were engulfed resulting in 72 people dying.
An air gap is not required in an SPF application as the liquid is applied using high pressure equipment, directly to the surface. After which it expands and sets becoming an extension of the substrate on which it’s applied, this result leaves no possibility for moisture to become trapped.
The alternative to this is a pre-manufactured variety of insulation which is installed to a large concrete soffit, and therefore should provide room for an air gap between the substrate and the insulation board. This is how the effect of any moisture becoming trapped within the fabric of the building is prevented. The issue with this form of insulation is when an air gap is postulated it can perform as a chimney, permitting the potential for the rapid and uncontrollable spread of fire as it did at Grenfell Tower.
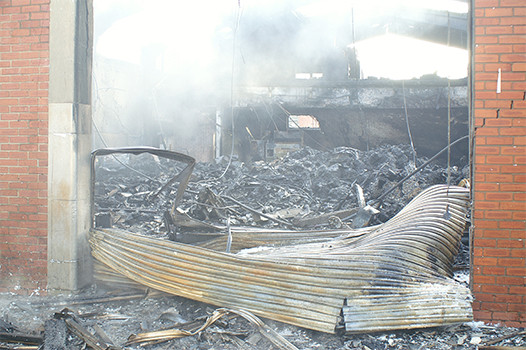
The official inquiry (phase 1) of the Grenfell fire, concluded that the ‘rapid spread of the fire was due to the presence of aluminum composite rainscreen panels containing a polyethylene core, which is highly combustible with the insulation boards and other combustible materials also making a contribution.’ Once the fire had escaped through the plastic window frames, the heat was so high on the outside of the building that the glazing broke and the fire entered separate apartments.
Refurbishment of Grenfell Tower was carried out between 2012 and 2016. The updated building regulations of 2010 did not contain certain technical requirements but set out a series of functional requirements which must be achieved, thereby allowing flexibility in the means by which the requirements are satisfied.
The major refurbishment included the addition of a ventilated rainscreen insulation and cladding system. A new external wall was created by attaching a number of components to the existing concrete facade. From floors 4 to 23, they consisted of insulation materials, new windows, new window infill panels, and outer aluminum composite material (ACM) rainscreen panels.
The outer layer of the new external facade, which covered the existing concrete spandrel panels and the columns, included the ventilated rainscreen panels made of aluminum composite material. Before being fitted to the building, the panels were fabricated into “cassettes” or three-dimensional shapes which can be hung on steel or aluminum supports fixed to the aluminum composite panel. Typically, this kind of system is called a “ventilated rainscreen system” because it is designed to protect the building from the bulk of direct rainfall but has gaps designed to permit the ventilation of the cavity behind the panels to guarantee that water is collected and drained away.
The rainscreen panels were manufactured as plain sheets and were used on the columns and for the spandrels at floors 4 and above. The “aluminum composite panels (ACP) were made up of 3mm thick core of polyethylene bonded between two 0.5mm thick sheets of aluminum with an external finish.
The inquiry noted that polyethylene is a combustible synthetic thermoplastic polymer which melts and drips on exposure to heat. It can flow while burning and generate burning droplets and has a high calorific value compared to other common construction materials. Additionally, it will provide a fuel source for a growing and spreading fire, melting at 130-135°C and igniting at around 377°C. 7 and on exposure to heat aluminum melts at approximately 660°C. It has a comparatively high coefficient of thermal expansion, which means that it can be expected to warp and deform under the influence of heat.
It was also noted that on all of the cut edges of the panels, the polyethylene core was exposed along the fold lines on the inside of each cassette. They were fixed to the building using steel-angle pieces (at the window head and sill), brackets and cladding rails on which the panels were hung.
According to the British Broadcasting Association, which carried out extensive research on the disaster, it was highlighted that the manufacturer of the cladding tiles was thought to have 'misled' the British Board of Agrément (BBA). They offer approval, testing, certification, and inspection services within the construction industry.
The BBA decided the evidence from the more successful European tests carried out on the cladding meant it “may be regarded” as having met the British standard. But the board was never shown the class E ratings for the cassette version of the cladding, and they knew nothing about them until a BBC investigation in 2018. The manufacturer was forced to admit at the inquiry that this would have "misled" anyone reading the certificate, including British architects. The Building Act 1984 and the Building Regulations 2010 states that external walls of buildings should be able to resist the spread of fire and that alterations made to existing buildings should not make the building noncompliant.
The documents obtained by the BBC implied the cladding fitted during its refurbishment was changed to a cheaper version. They show that the zinc cladding originally proposed was replaced with an aluminum type, which was less fire resistant, saving nearly £300,000. ($416,000). Cladding can create cavities which in some cases can cause a chimney effect, drawing flames up the cavity if there are no fire barriers. The BBC also discovered a series of poor fire tests reports commissioned by the cladding manufacturer, which have been at the heart of phase 1 of the inquiry. These tests were carried out in France, but were not published in the UK, and not passed to the British Board of Agrément. In March 2018 the BBC shared them with the Board, which confirmed the information crucial to the product certificate and this knowledge had never been handed over.
Fire Test Codes and Standards in the U.S.
According to the Council on Tall Buildings and Urban Habitat (CTBUH), there are currently 719 buildings taller than 150 meters, or 492 feet, under construction around the world, some of which will most likely include combustible exterior walls.
In the U.S, wall assemblies containing certain combustible materials need to comply with the NFPA 285 fire standard. Complying with such standards helps limit exterior fires to the point of origin and not spreading vertically or horizontally away from the source. NFPA 285 compliance appears in several chapters of the International Building Code (IBC). High-rise buildings commonly constructed under the IBC are developed collaboratively with code officials, fire departments, industry representatives, designers, and the public with these codes being adopted and enforced by state or local governments.
The International Building Code (IBC) stipulates, when spray foam insulation is installed within a building it is required to be separated from the building interior by means of a thermal barrier or ignition barrier, except for specific exempt situations (2015 IBC 2603.4). This commonly achieved by enclosing the foam in an intumescent paint tested via NFPA 275 Standard Method of Fire Tests for the Evaluation of Thermal Barriers; however, the presence of a barrier is not required if the materials themselves have been tested (in the manner intended for use) in accordance with NFPA 286 Standards The main reason for these requirements is to delay the involvement of the foam material in a fire.
A month after the Grenfell blaze, it took yet another media outlet, in this case a Baltimore local news source, to report that one of the city’s high-rises, a 32-story Marriott hotel, might be covered with the same aluminum composite panels that sheathed Grenfell. This may be due to some exterior wall assemblies being installed before NFPA 285 was available and referenced by the governing building codes with the first edition of NFPA 285 coming out in 1998. Additionally, when assemblies have been tested to NFPA 285, any modifications to them that deviate from the tested configuration could degrade fire behavior.
The NFPA 285, Fire Test Method for Evaluation of Fire Propagation Characteristics of Exterior Wall Assemblies Containing Combustible Components evaluates the potential for fire spread on the exterior of a building. Tracy Vecchiarelli, a Principal Engineer and Standards Lead for Building Fire Protection & Life Safety at the NFPA emphasizes, “As we saw in Grenfell and many other high-rise building fires, when the exterior cladding contains combustible material and has not passed appropriate fire tests, fire can spread uncontrollably and ultimately lead to loss of life. The NFPA has a long history of fire protection in high-rise buildings, but much of that history is limited to non-combustible construction. While we see great benefits with the new construction materials we have today, we need to be mindful of the fire risk they might present.”
Testing in the U.S.
The NFPA maintains the standard on the fire test, however, they do not perform the actual testing. This is carried out by OSHA's Nationally Recognized Testing Laboratory (NRTL) which identifies private sector organizations to perform certification for certain products to ensure that they meet the requirements of both the construction and general industry OSHA electrical standards.
Each NRTL has a scope of test standards that they are recognized for and each NRTL uses its own unique registered certification mark(s) to designate product conformance to the applicable product safety test standards. After certifying a product, the NRTL authorizes the manufacturer to apply a registered certification mark to the product. If the certification is done under the NRTL program, this mark signifies that the NRTL tested and certified the product, and that the product complies with the requirements of one or more appropriate product safety test standards.
Major manufacturers of sustainable spray polyurethane foam, for example Huntsman Building Solutions, clarify that they implement strict fire safety tests. Doug Brady, Vice President, Global Innovation and Product Management for Huntsman Building Solutions confirms, “Huntsman Building Solutions is committed to ensuring our premium products, such as Heatlok HFO Pro, are designed to pass the most rigorous fire safety tests. As our recent completion of two NFPA compliant wall designs demonstrate, we incorporate fire safety in all of our spray foam innovations.”
Guidance in the UK
Guidance, opposed to standards, is provided by the Secretary of State of Housing in the UK for communities and local government. This guidance, however, is not an obligation and a person designing a building may choose to use other methods and materials as long as the building conforms with the functional requirements of the building regulations.
The British Fire Brigade Union has called on the British government to remove flammable cladding from all tower blocks and public buildings. There are still 328 residential and public buildings in the UK using the same cladding as that on the Grenfell Tower, and 1,700 with other potentially combustible claddings. The union also asked for a new independent national body to oversee standards and best practices in fire service across the country. There is no national body to oversee fire and rescue service and fire policy. This means standards vary across authorities and lessons are not being learned.
Due to the recent pandemic, it is difficult to say with certainty when Phase 2 of the inquiry will conclude and be published. Phase 2 will investigate how the products were manufactured, tested and sold, and how the materials were presented to the market.
Steve Jewell, founder of Lapolla UK&EU offered his observation following the Grenfell tragedy, “Our clients often ask about any potential fire risks and this question has certainly been more frequent since the Grenfell Tower disaster. Thankfully, our agreement certification body has tested and addressed the safe use of our products in relation to fire safety and concluded that in a non-habited area, the spray foam is perfectly safe and can remain exposed without the requirement to use a thermal ignition barrier coating. In an inhabited area, the spray foam is also deemed to be safe as long as it is boarded over by a flame retardant material such as a plasterboard. The additional testing from a nationally recognized and reputable certification body gives customers the peace of mind they require, building faith in the product and the application methods. When dealing with areas that need stricter fire safety measures we are blessed because we have a fully certified Class 1 fire-rated spray foam on the market which has had a huge surge of interest in recent months as new legislation is talked about in relation to insulation in the commercial and industrial sectors. I suspect that the stipulations of this product may well become the norm in the near future as such legislations reinforce and strengthen.”
International compliance and communication
The ultimate question is where does the responsibility lie? Is it with the manufacturer, the body issuing the certification, or the law? Could this be a case of miscommunication or a deliberate way to save money on a project? After the Grenfell tragedy, the British government vowed, they would ensure that another fire like Grenfell would never happen again. However, four years later there are still over 500,000 people still living in unsafe buildings wrapped in flammable cladding in the UK.
Internationally there needs to be a large emphasis on quality of the installation of these systems. When using combustible materials, it is critical to ensure that they are protected from ignition and shielding methods such as fire prevention and barriers are all installed correctly. Therefore, the education of installers is imperative. If a material is not applied properly, there can be a massive negative influence on the performance of the insulation and cladding when exposed to fire. Ensuring trained and skilled installers is therefore paramount to maximize the safety of these systems.
In 2018 the NFPA published a Fire Risk Assessment tool named the EFFECT Tool which helps assess high rise buildings. This risk assessment methodology was written to assist global authorities to assess the risks and prioritize inspection/remediation efforts for the high-rise building inventory in their jurisdiction with exterior wall assemblies containing combustible component. This assessment tool follows internationally recognized risk assessment approaches. The NFPA has received international interest in the EFFECT tool and related reports but there is no data on whether authorities have acted on any of the recommendations.
The expectation of buildings to be energy-efficient, sustainable, and safe, balanced with an obtainable cost for manufacturers and developers is extremely demanding. However, the main priority for everyone from the manufacturer and supplier to the architect, builder, and material installers is to have a responsibility to the people who reside in these structures.
As the Grenfell inquiry continues, the question still remains for many—when will there be a coherent way of collecting international incident data on these tragedies rather than relying on media news outlets? Without this internationally collated data, how can we ensure that such a horrific tragedy will not happen again? The answer could be simple – being aware of safety standards and implementing these into testing, manufacturing, design and installing the correct insulation by certified professionals.