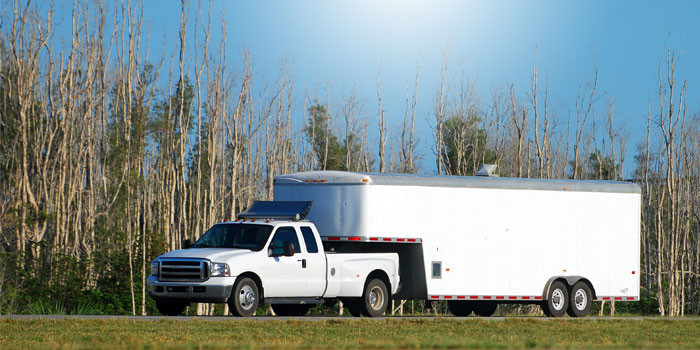
Give It Some Air
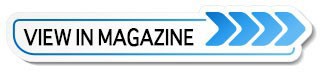
Summer 2020 – Spray Foam Magazine – Your air compressor is one of the most important pieces of equipment on your spray rig, so it is critical to make sure that your air compressor offers enough air to support all the equipment that is on your rig.
This could include:
- the spray gun,
- transfer pumps,
- air tools,
- coating pumps,
- mixers,
- fresh air system,
- and possibly the proportioner, if it is an air driven system
You need to identify the cfm requirement for each component on your rig and add up the requirements for all the devices that will be operating simultaneously.
For example, you might have these components on your rig. [TABLE 1]
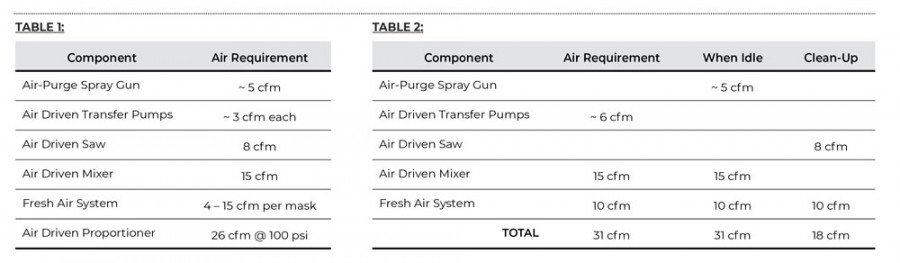
Luckily, most of you don’t have an air driven proportioner, those use a lot of air.
So, let’s take a look at the air operation of a rig assuming it has a hydraulic or electric proportioner.
It helps to understand that different components operate at different times during the operation of your rig – some components need air when you are spraying, some when you release the trigger, some during clean-up and others that you will use during all phases of operation.
You can use these phases to categorize how much air will be needed during each phase of operation and we will use the maximum amount of air needed to size the compressor.
TABLE 2 table categorizes each component based on when it will be used.
The highest total air requirement during these operation stages is approximately 31 cfm needed when spraying.
A typical piston compressor has a rated duty cycle around 75 percent, which means that we will calculate 31 cfm as 75 percent of the maximum output.
So, we divide 31 cfm by 0.75 and we get approximately 41 cfm.
Next, we divide 41 cfm by 4 cfm per HP, because a piston compressor typically offers about 4 cfm per HP.
When we divide 41 cfm by 4 cfm per HP we get 10.25 HP, so we would need a piston compressor at least 10 HP or bigger.
However, if we want to look at a rotary screw compressor, the calculation changes a little, because they can operate at a 100 percent duty cycle, so we can size it directly for the maximum air needed, which would be 31 cfm.
A screw compressor still delivers 4 cfm per HP, so 31 cfm divided by 4 cfm per HP is 7.75 HP. This means if we used a screw compressor, we could get an 8 HP or bigger.
Note, the fresh air system has one of the larger air requirements, so another option would be to have a separate, portable air compressor for your fresh air system, and this would lower the air requirement and the necessary size of the main compressor.
Now, your rig is probably already constructed, and hopefully someone already did these calculations, but if you are an owner, manager or supervisor I highly recommend taking inventory of the equipment on your rig and conducting your own calculation to see where you stand – to find out if you are pushing your compressor to the limits or if you have some extra air available on your rig.
About The Author
Robert Naini has a Bachelor’s of Science in Mechanical Engineering and an MBA from the University of Texas in Arlington. With more than a decade of experience on the cutting edge of spray foam insulation, Robert has created Spray Foam Advisor to offer web-based training and education, with videos, articles, blogs and more, to help you get better. // Watch his latest Building Science webinar for FREE at www.bswebinar.com
Direct any questions you have about statements made in this article to Robert Naini: 817-983-3544 robert@sprayfoamadvisor.com
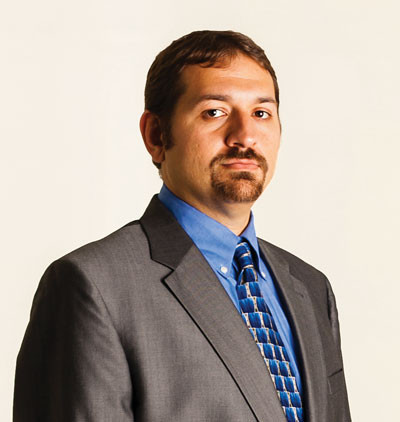
*Spray Foam Magazine does not take editorial positions on particular issues; individual contributions to the magazine express the opinions of discrete authors unless explicitly labeled or otherwise stated. The inclusion of a particular piece in the magazine does not mean that individual staff members or editors concur with the editorial positions represented therein.