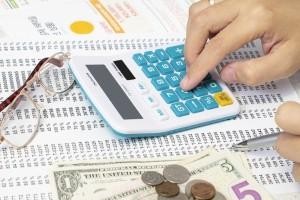
Consulting Firm Sees Strong Growth in Insulation Markets, Particular for Spray Foam
February 15, 2011 - The financial consulting firm Principia has issued a new report which projects that the North American market for insulation products will grow after several years of steep contraction.
Last year, the total insulation products market - including both commercial and residential applications - comprised 5.8 billion pounds of product with a net value of more than $5.2 billion. According to Principia, this represents a 30 percent decrease in demand over the last 4-year period.
Much of the drop was driven by the crunch in the real estate markets, which put thousands of individuals and companies in the construction and real estate industries out of business. Now, however, home values are recovering in many key areas, mortgage rates are rising and new building activity is coming back on line.
In addition, energy is getting more expensive, as gas and fuel oil rise alongside crude oil futures. That makes better insulation more appealing, and it decreases the payback time of investments into renewable energy sources, energy-efficient fixtures and spray foam insulation.
"With rising energy prices and uncertainty about future fossil fuel costs, payback periods for higher-cost foam insulations are becoming shorter, estimated at an average five years at present," reports Principa's Ken Jacobson. "Even though spray foam insulation, for example, can be three to five times the installed cost of fiberglass, it remains a small part of the cost of these projects, which are often financed with home equity and commercial loans."
The consultancy believes that the North American market for spray foam and other types of insulation material will grow to $6.3 billion next year, as both contractor enthusiasm and consumer awareness of the benefits of a tight building envelope grow. In an environment characterized by concerns about both global warming and rising carbon costs, it makes sense that anyone building or buying a new home will want it to be as efficient and snug as possible.
New technologies are also helping, by making spray foam installations both cheaper and more environmentally friendly. New propellants have less impact on the ozone layer, while manufacturing and deployment innovations will help reduce the total cost of such applications.
Around the country, developers are displaying their wares in model homes that make building envelope improvement a centerpiece of the company's presentation.
It's time for spray foam to step up and take its place as one of the most important tools in the building industry's quest for greater sustainability.