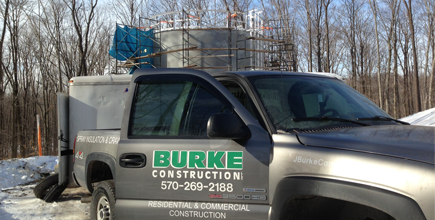
Water Tower At Explosives Factory Insulated With Closed-Cell Spray Polyurethane Foam
GOULDSBORO, PA – March 21, 2013 – Pocal Industries, Inc. is the world’s largest producer of non-lethal, mortar training ammunition for the U.S. Army and international governments. The facility was expanding its operation and needed to install a new water tower to accommodate its sprinkler system. Although the new tower contained a large metal coil heating system that would prevent 100,000-plus gallons of water from freezing during Pennsylvania’s cold winters, the company decided to apply insulation as an added buffer to prevent condensation from forming and to limit the amount of maintenance the tank would need.
Pocal had the option of installing foam panels to insulate the tank, or to install spray polyurethane foam. Since panels were costly, Pocal considered spray foam as an alternative. The local certified sprinkler company contacted Burke Construction, LLC, a contractor specializing in commercial construction, spray foam, and coating applications. The sprinkler company had worked with Burke before on previous construction projects.
Matt Bauman, Burke Construction’s General Manager, said the cost of installing spray foam would be about half of what it would cost Pocal to install the panels.
“It would’ve saved them time to go the other way, but they were still building the new facility and weren’t ready to move in,” he said. “It saved money and worked out better financially.”
Upon arrival at the jobsite, crewmembers had to be screened before entering the premises as a security measure required by the explosives factory.
“There was a brigadier general there and we weren’t allowed in certain areas of the compound,” said Bauman. “There were areas where you couldn’t park your vehicle within 50 ft. of the building.”
Since the water tower was located about 100 ft. from the main facility, crewmembers did not have difficulty parking their spray foam rig within a reasonable distance of the water tower.
A significant amount of prep work had to be done on the 27-ft. tower before spray foam application could take place. Crewmembers put scaffolding up around the circumference of the tower, which took about two days. Although the use of a boom lift could have saved a day or two of setup according to Bauman, the land surrounding the tower would have made it difficult to maneuver. They used tarps and hung plastic to protect nearby buildings from overspray. Parts of the tower itself also needed protection. There were two hatches on the structure, a ladder on the side of the tower, and breathers at the top of the tower that had to be covered.
After preparations were complete, crewmembers employed a Graco Reactor E-20 to apply Bayer MaterialScience’s Bayseal CC Polar 2 lb. closed-cell spray foam. Crewmembers made four 0.5-inch passes until the foam reached a nominal 2 inches. The foam thickness varied at the base and top of the structure. Near the bottom of the tower where the concrete met the tower base, the flange, the foam thickness was sprayed in several passes to attain a thickness of 3 inches. Crewmembers pitched the roof to allow for drainage. They applied about 3 inches of foam to the center, and only about 2 inches to the edge to create the pitch.
According to Bauman, the weather was awful during application. The location of the tower was near the highest point in the Poconos – one of the highest areas in the state.
“It was brutally cold,” he said. “We kept having to put it off because we couldn’t heat the tank since it would void the warranty. It was only 40 degrees when we were finally spraying and there was rain, snow, and it was windy.”
Due to the conditions, crewmembers had to wait a couple of weeks between their spray foam and coating applications, covering the tower in plastic for protection. Once the weather finally cooperated, crewmembers applied POLAROOF RAC, a single component urethane, modified with bright aluminum flakes and fire retardant chemicals, manufactured by Andek Performance Coatings and Sealant Systems. The coating was used primarily to provide UV protection, according to Bauman. The mil-thickness was 30. It took three crewmembers about three days to complete the spray foam application in February of 2013. The total spray area of the job was just under 3,000 square feet. The final results of the water tower application proved successful. Bauman said Pocal was pleased.
“The only challenge was fighting weather that didn’t cooperate, but ultimately we got it done and everyone was satisfied,” he said. This was Burke Construction’s first water tower project and they hope to do more similar projects in the future.
About Burke Construction LLC: Burke Construction LLC owns and maintains its own spray insulation equipment. With trained technicians and comprehensive energy analysis, they offer money saving, green energy building products to homeowners and contractors. Burke Construction LLC installs open- and closed-cell insulation for new construction and existing homes. The company can help design, develop, and implement large-scale commercial project management to home additions and renovations. For more information about Burke Construction LLC, please use the contact details and links provided below.