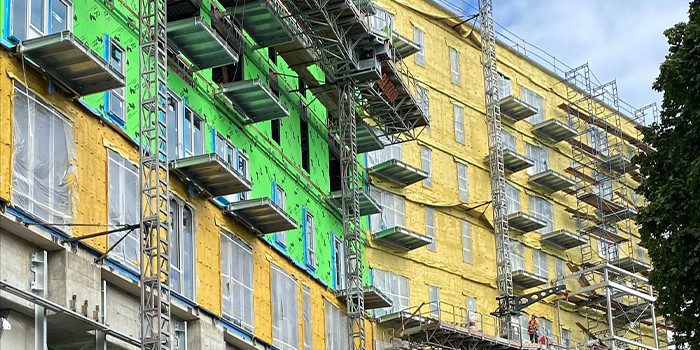
The Quebec Check
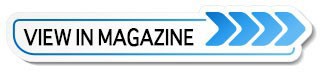
Spray Foam Magazine – Fall 2022 – Project ‘Ilot Rosemont’ is one of the largest building projects in Quebec. It was completed in partnership with the spray foam installer and with the “Accès Logis” program, which is a financial assistance program adopting collaboration among public, community and private resources. The program’s purpose is to create social and community housing for low, or modest-income households, or people with specific housing needs.
The Ilot Rosemont project’s objective was to construct a building adjacent to the Rosemont metro station. The building is comprised of 193 senior housing units and offices that are the administrative center for the Office Municipal d’habitation de Montréal, whose mission is to improve the living conditions of low- and moderate-income individuals and families by providing them with quality subsidized housing. The building’s design is in the shape of a square, open to Boulevard Rosemont and the Marc-Favreau library with a forecourt creating an inviting public square, showcasing the new library. The building is also divided into two wings, one to the west with 10 floors, and the other to the south side with eight floors.
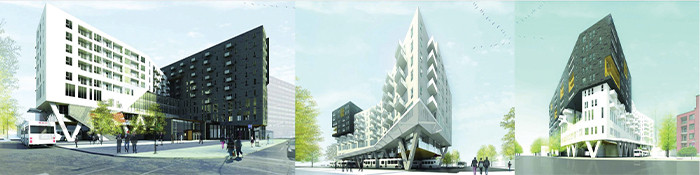
Ilot Rosemont final construction rendering which will be comprised of 193 senior housing units and offices for the administrative center for the Office Municipal d’habitation de Montréal.
The project presented many logistical challenges arising from the structure of the building itself. Some of these features included: two divided wings, a 10-story wing on the west side, an eight-story wing on the south side, a V-shaped support column two-storeys high supporting the building with connecting beams and many beams on level three, including five for which have post-tensioning work. Another feature of this project is the slab on a steel deck over a large area of level two, and a concrete structural slab on level three over the entire surface of the building. The thermal resistance also needed to be high for Quebec’s climate, and SPF would help meet the insulation requirements.
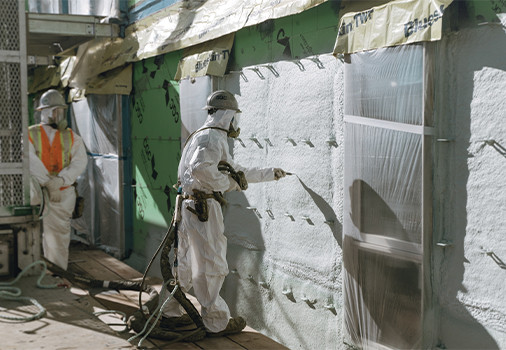
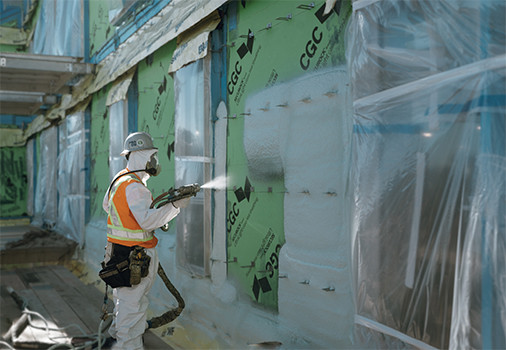
TOP: Huntsman Building Solutions’ Heatlok Soya HFO installed by IMS for the Ilot Rosemont building project; BOTTOM: Testing the depth of the foam after application
Isolation Multi-Services Inc. (IMS) were hired to install spray foam insulation to this epic project. With many years of experience in residential, commercial, and institutional insulation, the owners of IMS, Vincent Brouillette and Martin Côté clarified by adding, “Isolation Multi-Services specializes in residential and commercial insulation, membrane installation, soundproofing, and leading-edge services. Our clients in Montreal, Laval, the North Shore, and the South Shore know that they can count on our experience, expertise, and the outstanding quality of our insulation products for optimal results.”
The main objective for Isolation Multi-Services Inc on this project was to achieve, with Huntsman Building Solutions (HBS) products, the best building envelope possible. They like to work with HBS for their product's performance, the quick application of the material and the energy savings it creates for their client. Since the envelope was insulated with SPF, both the manufacturer and the installer needed to work closely together all throughout the project to ensure the best results. They had numerous meetings, evaluations, and inspections through the duration of the construction to insure the project would be delivered as expected.
Both HBS and IMS decided that the Heatlok Soya HFO foam was the best choice for this project, due to its air and vapor barrier, high R-value, and weather resistive barrier. It has one of the lowest environmental impacts compared with many insulation products, and there was no need for full surface membranes which would take time to install.
Making the spray foam insulation quick to install and durable. During construction, the SPF resisted well to water and high winds, so there was less product to replace and therefore less downtime involved. Long term, the product will also last for the lifetime of the building. It will also resist water and mold and can withstand higher wind loads.
The project was one year behind schedule, so when IMS arrived the pressure was on to try to save time. Due to the complexity of the architecture and its unique design, including suspended levels, the project was a welcomed challenge. The crew from IMS applied HBS Heatlok Soya HFO with three inches on all exterior façades of the building, sprayed on concrete, BlueSkin membrane and Securock panels.
IMS was able to save time by using their Graco E-30E, one extra spray team and the HBS Heatlok Soya HFO foam. Completing the project including the spray foam, cement plaster and membrane, took the crew ten months. Owners of IMS, Vincent Brouillette and Martin Côté commented after the application saying, “The rapid growth of our company in recent years has allowed us to move into a new state-of-the art facility fitted with cutting-edge equipment. Our impressive fleet of trucks also allows for more rapid response times and overall customer service. There were also many complicated details where the continuity of the building envelope would have been hard to achieve without Heatlok Soya HFO closed-cell spray foam. The client is very happy due to the quickness of installation and the high quality of the work.”
Having the manufacturer and installer working together on this complex design, ensured the job was completed on time and to a high standard. Leaving everyone satisfied with the great result. It proves once again, having a superior product and a good relationship between all parties is key to a successful project.