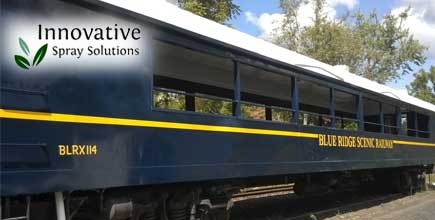
Spray Polyurethane Foam and Polyurea Help Turn Aging Train Into Scenic Rail Car
BLUE RIDGE, GA – October 30, 2013 – Nowadays, contractors are finding different settings where spray polyurethane foam can be beneficial aside from commercial building or residential home projects. In a recent extensive project that involved retrofitting an open rail car, spray foam played an important role.
The Georgia Northeast Rail Road (GNRR) Blue Ridge Scenic Railway is one of the top tourist attractions in northern Georgia, taking people on both climate-controlled trains and open-air rail cars on scenic rides from Blue Ridge to McCaysville, which borders the Georgia/Tennessee state line. Since the open rail car option had become increasingly popular among their customers, the GNRR opted to get another rail car on the track. Instead of constructing a new train, the GNRR decided to retrofit one of their retired mail cars known as "The Brittany" and convert it into an open rail car.
In order to accomplish a successful facelift for The Brittany, different materials were used in the project, including SPF. The GNRR brought in Innovative Spray Solutions (ISS) for the job, which consisted of applying SPF, polyurea, and polyurethane enamel coatings on different sections of The Brittany throughout its restoration. The restoration also included adding new benches with cushions and a brand new lighting and sound system.
The project took place outdoors in a designated train work era of the GNRR rail yard. Since The Brittany was previously used as a mail carrying car and it was closed up, the 80-foot long by 9 feet-wide train car had to have its sides cut out to transform it into an open-air car. The crew was outfitted with Tyvek spray suits, face masks, gloves, and goggles for the duration of the project.
Prior to the materials being applied, the ISS crew masked and taped off the side openings to avoid overspray damage. On the outside of the train, the crew sandblasted the old paint and rust, and then applied phosphoric acid with a hand sprayer so that the steel substrate would not rust in exposed weather. The crew also sanded the surface and applied Sherwin Williams Kem Kromik primer to promote adhesion to the substrate. Then, the crew removed the existing floor boards, which had rotted over time, from the interior of the train, and replaced them with framed, two-by-four wood subflooring.
Then, the crew installed five inches of Thermoseal 500, a 0.5 lb. open-cell spray polyurethane foam made by Spray Foam Polymers, to fill up the cavities between the floor joists. After the foam had cured, the crew installed 3/4 AdvanTech wood flooring to protect the foam. Then, the crew applied 90 dry mils of grey polyurea supplied by SPEC Technologies.
ISS' Kelly Daugherty said that even though the spray foam application was a small part of the project, it was absolutely essential for the restoration, as the new benches needed a strong, long-lasting flooring for them to be installed on.
"The combination of spray foam and polyurea installed in this project provided added support," said Daugherty. "It also provided sound attenuation, which makes for a much more pleasant train ride."
The Brittany's restoration also included the application of polyurea on the train's roof. Then, a coat of white HSS 535 solvent-free silicone roof coating was applied on top of the polyurea to seal and waterproof the roof.
The interior and exterior of the Brittany was finished with different colors of DuPont Imron AF700, a polyurethane enamel coating made by DuPont. The train's exterior sides, as well as the interior sidewalls were sprayed with a top coat of blue polyurethane enamel coating. A white polyurethane enamel coating was applied to the inside ceiling and the endwalls.
The benches were fabricated at a separate facility, two miles off site. During their production, they were spray coated with black polyurethane enamel coating and then installed inside The Brittany at the end of the project to keep them from getting damaged by overspray.
The crew had one rig on site equipped with a SFE 5/12 K Boss proportioner, a 2.5 gallon Binks Pressure Pot paint sprayer, a 250-foot heated hose, a Graco Fusion Pro air-purge spray foam gun, and a DeVilbiss spray finishing gun. The Boss proportioner and the Fusion spray gun were used for the SPF and polyurea applications, whereas the Pressure Pot paint sprayer and the DeVilbiss spray gun were utilized for the priming and top coat applications.
It took the four-man crew five months to finish the Brittany's retrofit project. According to Daugherty, the project took longer than expected because the crew was faced with intermittent, unexpected humid and rainy days that caused downtime in the applications
With a restoration facilitated by SPF and polyurea that included three new bathrooms, new lights, a better sound system, and cushioned benches, the Brittany was added back to the Blue Ridge Scenic Train Concession in early October 2013.
About Innovative Spray Solutions, Inc.: Innovative provides customers with a reliable and eco-friendly product that withstands everyday usage for residential, commercial, and industrial settings. Innovative installs open and closed-cell spray foam insulation for homes or businesses. The company is family-owned and operated in Blue Ridge, Georgia. For more information about Innovative Spray Solutions, Inc., please use the contact details and links provided below.