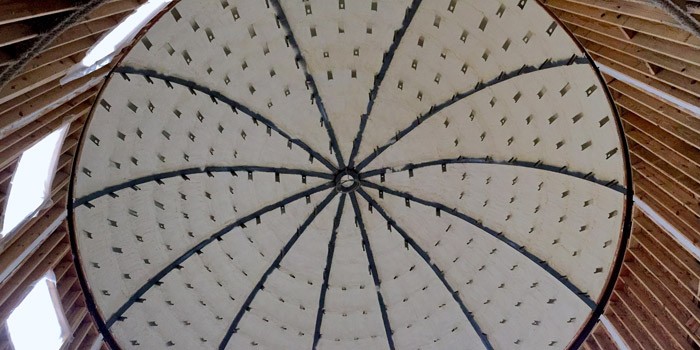
SFWW Contractors Corner: The Foamed Dome
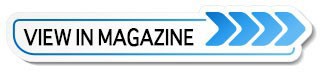
LOUISVILLE, KY – January 23, 2018 – Ben Monsma of Louisville Spray Foam Insulation (LSFI) went on Facebook hoping to find information pertaining to Lapolla’s FOAM-LOK 2000-4G closed-cell foam, which his team was looking to try out. He posted an open-ended question on Spray Foam World Wide—the Facebook group that serves as one of the social media arms of the spray foam (SPF) industry—and received responses almost instantaneously, followed by a private message from a Lapolla representative pointing Monsma in the right direction as to where to obtain the foam.
This connection resulted in LSFI applying the foam in most of their projects. One of these projects involved insulating the underside of the roof of a particular area inside a commercial building—this area happened to be shaped like a dome.
“The dome was part of new construction and expansion of the building that will serve as a meeting hall within the retirement center,” says Monsma. “We were hired to spray the dome-like vaulted ceilings of this area, and we needed to get it done as promptly as possible.”
RELATED Spray Foam World Wide Continues to Connect the SPF Industry, July/August 2017 Spray Foam Magazine Heats Up The Summer , Profoam Corporation Discusses New R-Value Requirements
LSFI and the general contractor thumbed through the blueprints and saw that the area called for an R-38 value. The FOAM-LOK 2000-4G formulated with Honeywell’s Solstice Liquid Blowing Agent fulfilled that specification, as it provides an R-7 value per inch and the LSFI crew applied 5.5 inches of foam to the roof deck.
A crew of three took on the job, which took place on a Saturday with no other trades present on site. In order to get to the application area, the LSFI crew used a scissor lift to rise 36 feet off the ground. The lift was closed up and the applicators wore body belts with a tether anchored to the boom of the basket for fall protection. Ventilation was consistent with the large doors surrounding the area were opened, plus the general contractor had placed industrial fans around the area, which were running throughout the entire spray foam application. The LSFI crew had their own exhaust fans going as well. The crew wore PPE consisting of Tyvek suits, fresh air-supplied respirators, gloves, and boots while they worked.
The LSFI crew spray-applied the 5.5 inches of foam in one pass, installing a total of 1.4 sets of foam throughout a six-hour period to complete the job.
“We were scheduled to use two sets at 4,000 board feet and we ended up using much less,” notes Monsma. “This was due to the high yield that the foam we used provided; we ended up using 25 percent less foam than anticipated.”
The right guidance plus the ideal material equated to a unique SPF project being completed in excellent time. Well done, LFSI!
Join the SFWW Facebook group »
Search “Spray Foam World Wide” or go to facebook.com/groups/1031962486856843