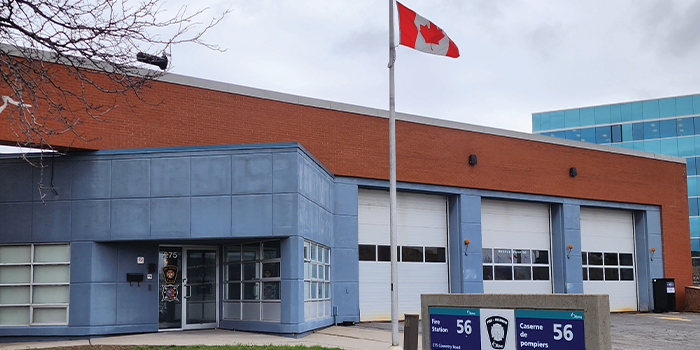
Rising Strong
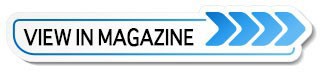
SPRAY FOAM MAGAZINE – An ounce of prevention is worth a pound of cure, and no one knows that better than firefighters and city planners. So, when a construction crew located cracks in the concrete floor of the Ottawa Fire Hall’s Station 56 during a remodel, the City of Ottawa acted fast. An engineering report determined that the cracking had not yet affected the building’s structural integrity, but indicated it was only a matter of time.
Traditional repairs would involve excavating the fire station’s floor, removing the old concrete slab, and re-compacting the soil before pouring new concrete. This intrusive repair could take up to a month to complete and would involve the unthinkable, decommissioning entire sections of the fire hall for days at a time. There had to be another way.
Dan Sills, owner of 1000 Islands Spray Foam in nearby Elizabethtown, Ontario, received a call from ANS Construction, whom he had previously worked with on a fireproofing project. ANS had discovered the cracked fire station floor and wanted to discuss the feasibility of subcontracting 1000 Islands to perform deep-injection polyurethane slab jacking to repair the station’s floor without disrupting the station’s operations and generating
a massive repair bill.
At the time, Dan and his team had yet to take on a polyjacking job. Nonetheless, Dan jumped at the opportunity to try something new to take his spray foam operation to the next level. He recalls, “We met with representatives from the City of Ottawa to get everyone on the same page about procedures, and we also did a lot of planning on how to mitigate risks.”
Soil naturally deteriorates over the sources of decades, causing subsurface voids that can destabilize slab foundations. Deep soil injection both fixes and prevents these cavities. Unlike organic soil, the synthetic foam does not break down, allowing for a permanently stable and level foundation with no excavation necessary. It was just what the fire hall needed.
In April 2023, Dan and his crew of three sprayers visited Station 56 to assess the extent of the issues. He describes, “They were experiencing not only cosmetic issues with the building, but it was becoming a health and safety issue due to tripping hazards from the floor cracking across hallway corridors.” The area in need of leveling work spanned about 250 square feet and spanned across well-traversed areas like the captain's office, bathroom, and through hallways.
Dan knew that polyjacking was the correct choice. He explains, “I’d heard of deep injection jobs stabilizing things like highways, where they must inject at depths of 20-30 feet. In our case, we only had to go down as far as the organic material beneath the slab.” With that in mind, Dan was confident his team could deliver excellent results.
Throughout the injection process, Dan had an arsenal of slab jacking and spray foam professionals in his corner. Their supplier PolySource Industries provided the lifting foam and representatives were on call throughout the project to answer any questions. They used a hydrophobic polyurethane system called Polysource 3.5DI, a Canadian rebrand of NCFI Terrathane specially formulated for ground stabilization work.
Over the course of six days, the 1000 Islands team and the ANS Construction team worked in tandem on the deep injection process. First, ANS drilled holes into the floor and placed copper pipes through which to inject the foam. Before injecting, Dan’s team used a borescope inspection camera to examine the subsurface, checking for voids and cavities.
While injecting the foam, they used a laser tripod and detection units to monitor the slab and prevent over-lifting. The sprayers used a PMC PH-40 Proportioner with Graco T2 transfer pumps connected to a SDMO diesel generator. The proportioner included a stroke counter, enabling more control over the amount of foam injected. They injected the foam into the ground using a long tip affixed to a Graco GX-7A Slab Jacking Gun and injected the foam in precise four-second intervals at varying metered depths in the soil beneath the concrete slab.
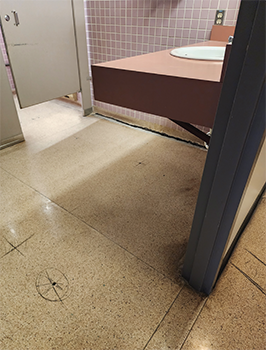
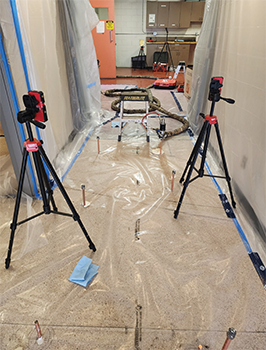
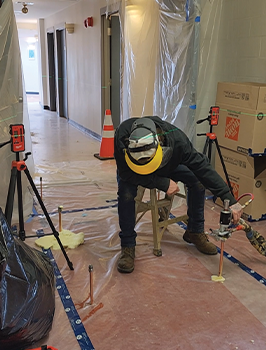
To level the station’s floor, the 1000 Island Spray Foam team inserted copper pipes into drilled holes to convey foam from the gun into the soil
After injecting, they had to stop and wait for an additional four seconds to give the foam time to expand and settle. This delicate process required good timing, because stopping for too long could cause the foam to settle in the pipe rather than beneath the ground, yet not stopping could cause the slab to over-lift, causing even more leveling problems.
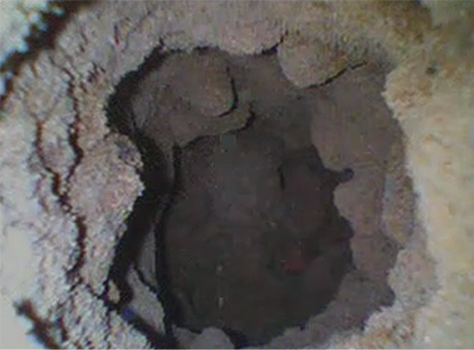
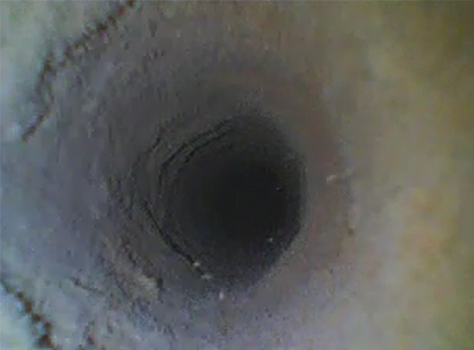
ABOVE: Before; BELOW: After
Unlike a standard spray foam job, deep injection jobs have less risk of airborne particle inhalation, though injecting foam too fast still carries the risk of a blowout, in which the pressurized foam bursts from the pipe. To safeguard against this possibility, the team wore masks and face shields, and covered the interior of the fire station in protective plastic. At the end of the injection process, they re-inserted the borescope camera into the test holes to ensure that the soil was well-compacted. The borescope camera allowed them to compare their pre-injection fill status with the post-injection fill status, providing everyone involved with assurance of a floor well-leveled, and a job well-done.
For use by SprayFoamMagazine.com & Spray Foam Magazine