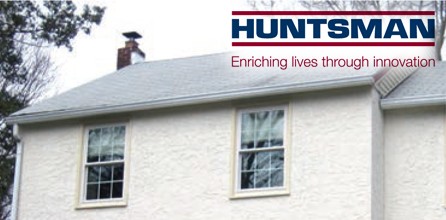
Reducing Energy and Improving Comfort with Closed-cell Spray Foam Insulation
In a typical neighborhood, a typical 1950s house stood: under-insulated, leaky and uncomfortable with high heating and cooling bills. The owners kept the thermostat setting conservative, because setting it higher was "a waste of energy."
To reduce energy and improve comfort, the homeowners turned to CertainTeed CertaSpray® Closed Cell Spray Polyurethane Foam (SPF), which was used to insulate the attic, basement walls and above-garage floor. In the process, the air infiltration rate was reduced by ~25%, duct leakage to the outside improved significantly, and an overall 30% reduction of energy was achieved.
According to the Department of Energy, about 60 million U.S. homes are underinsulated. Retrofits offer a significant opportunity to reduce energy; however they should not be taken lightly, as there are a number of issues to be addressed – combustion safety, ventilation and building science. A Building Performance Institute (BPI)-certified analyst from Reclaimed Energy was on hand to ensure the retrofit did not potentially harm the structure or occupants.
Pre-Retrofit Energy Audit
An energy audit conducted by Reclaimed Energy found the home had a HERS index of 140, meaning it used 40% more energy than a similar home built to the IECC 2006 Energy Code. A blower door test found the house to be very leaky, with more than 60% of its air being replaced with outside air every hour. Additionally, a duct blaster test found the duct leakage to the outside was so high, a good reading could not be obtained.
The Attic
This home had a walk-up, ventilated attic with access from the office located above the garage. There were no ducts or recessed lights in the attic. During the initial blower door test, air rushed into the home through this door. Two potential insulation schemes were discussed – a hybrid foam/fiberglass solution on the attic floor or an all-SPF solution on the underside of the roof deck.
Both solutions would be an energy-efficiency upgrade from existing conditions. Without ducts in the attic, creating an all-SPF unvented attic typically would not provide energy benefits over a well-sealed, SPF/fiberglass hybrid attic floor. In addition, an attic floor solution would be less expensive.
However, the decision was made to convert the existing vented attic into an unvented attic for two reasons – avoiding a costly wiring upgrade and the potential to finish out a 200 sqft. attic space into an extra room, adding $30,000 to $40,000 to the home's value. A sprayable intumescent paint tested as a 15-minute thermal barrier was applied to the SPF sprayed in the attic. This was a conservative measure, as code only requires passing the ignition barrier test for non-storage attic space.
The Above-Garage Floor
The office space above the garage was the most uncomfortable room in the house. Not surprising, as it is bounded on five out of six sides with exterior walls. Pilot holes drilled in the ceiling above the garage and below the office revealed that there was no insulation or subflooring beneath the hard wood floors and one of the stud bays was being used as a cold air return without ducting. The homeowner's desire to retain the current stucco garage ceiling played a role in the retrofit approach.
To insulate and air seal the area between the hardwood floor and the garage ceiling, fibrous insulation was installed through holes drilled in each bay (taking caution not to fill the bay being used as the cold air return). This put insulation in contact with all six sides of the bay including the office floor.
To air seal the garage ceiling, three inches of CertaSpray Closed Cell SPF was added on the underside of the ceiling, covering the installation holes and any gaps at the top plate connection.
With this hybrid approach, closed cell SPF, a vapor retarder, was placed on the cold side of this assembly. Therefore, three inches of the SPF were used to ensure the interface between the garage ceiling and fibrous insulation would stay warm enough to eliminate condensation concerns. As required by code, a 15-minute sprayable thermal barrier coating was applied to the SPF.
The Basement
The existing basement and subfloor contained no insulation at all. The decision was between insulating the subfloor or the basement walls. Because the ducts were in the basement, the decision was made to insulate basement walls with one-and-a-half inches of CertaSpray Closed Cell SPF directly onto the concrete masonry units, thereby putting the ducts into conditioned space. This approach was expected to have a more significant impact on the home's energy efficiency and comfort. Like the garage and basement applications, the SPF was covered with a 15-minute sprayable thermal barrier. Electrical, gas and plumbing items were protected from SPF using polyethylene sheeting.
Post-Retrofit Audit
Two safety concerns needed to be checked upon completion of the retrofit – ventilation needs and combustion safety. A blower door test revealed that natural ventilation to the home still met ASHRAE 62.2 recommendations. The auditor also performed combustion safety testing in the basement's combustion appliance zone (CAZ). The high-efficiency furnace was sealed combustion and not of concern. However, the water heater was naturally drafting and had to be checked. The CAZ was under slightly negative pressure of -2 Pascals (Pa) normally and depressurized further to -4 Pa under worst case conditions. Both values were within BPI standards. When operating, the water heater was drafting at 9 Pa compared to ambient pressure, suggesting good drafting and minimal chance for back drafting or flue gas spillage.
Pre- and post-retrofit blower door tests showed a reduction of 23% in air infiltration due to the SPF measures. This added significant savings in utility costs, as each cubic foot of air entering the house via infiltration must then be heated/cooled to get the house back to its thermostat set point. Further reduction opportunities were noted (particularly replacement of the original basement windows), with the caveat that any additional tightening should be accompanied with another CAZ test.
Prior to the retrofit, the duct system was too leaky to be pressurized to 25 Pa with respect to the outside, causing a significant source of energy consumption. Following the retrofit, the auditor was able to reach 25 Pa, and found the outside duct leakage to be 90 CFM. Even though the ducts were still leaky, a much larger portion of the duct leakage remained within the home, a significant positive for energy efficiency. Further duct sealing of exposed ducts in the basement was recommended to improve comfort and supply throughout the house.
Following the retrofits, Reclaimed Energy calculated the home's new HERS index of 98 and an energy reduction of 43 MMBTU per year, a reduction of 29% compared to typical annual usage. The modeled reduction in heating and cooling demand was 48%. The primary reduction contributors were bringing the ducts in conditioned space by insulating the basement, reducing energy loss from air infiltration and reducing the conductive heat losses through the roof and ceiling.
Conclusion
The SPF retrofits will enable the owners to save over $630 annually in utility bills. More importantly, they now have a new level of comfort without drafts and cold uninsulated surfaces. The owner said, "the house just feels warmer and quieter too." Lastly, the retrofit enables an additional 200 sqft. of living space, potentially increasing the home's value. While retrofits present challenges, having a BPIcertified contractor on-hand helps ensure combustion safety, ventilation and building science concerns are addressed.