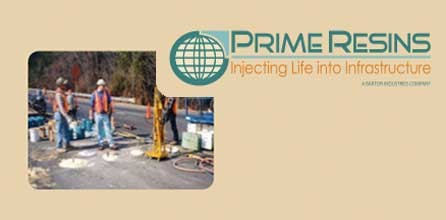
Polyurethane Grout Resolves Highway Settling
Problem: During the winter of the year 2000, a pipe contractor was attempting to bore under Highway 78, a five lane major artery carrying commuters to and from the eastern suburbs of Atlanta. The bore was to be about 12’ below the surface of the highway and nearly 200’ in length. At first the 36” boring auger made effortless progress through the wet, sandy, clay-like substrate that was full of partially decomposed vegetation and other biodegradable materials. The contractor’s hopes of completing the boring ahead of schedule were dashed when the auger struck a large vein of Georgia Blue Granite.
The initial portion of the bore was enlarged to 48” to accommodate hand digging, transforming the boring operation into a tunneling operation. Explosives were used to break the rock into small pieces that could be removed by hand. Due to the small diameter of the bore and the density of the granite, progress under the highway was slow. After completing about one half of the total distance, it was detected that the asphalt above the tunneling operation was sinking dramatically, creating a dangerous dip that affected the two westbound lanes of the highway. Tunneling was halted immediately and officials with the Georgia department of transportation were called in to assess the situation.
Solution: After their initial inspection, Barton Southern Company, a local contractor experienced with chemical grout injection for the purpose of soil stabilization, was called in to determine what had caused the dip in the asphalt and discuss possible solutions. After drilling several holes through the 12” thick asphalt highway, it was determined that the substrate had settled beneath the asphalt about 8” directly over the centerline of the tunneling operation. The reason for this settlement was most likely due to existing voids created by decaying biodegradable materials in the soft, sandy substrate that collapsed during the blasting portion of the tunneling operation.
In order to stabilize this situation, one inch holes were drilled in a grid, five feet on center, beginning over the centerline of the tunnel and offset to either side. Prime Flex 920, a hydrophobic, water-activated polyurethane grout, was injected through ¾” black iron pipes driven to an elevation just over the top of the tunnel casing. In its raw form the Prime Flex 920 penetrated the void areas and bad soil easily. Water in the substrate activated the grout, causing it to expand and form rigid foam that filled the voids and consolidated the loose and sandy soil to hardness similar to that of sandstone. The grout was placed in lifts from the top of the tunnel casing up to the top of the substrate. As each of the one inch holes were grouted the gap between the substrate and the asphalt began to decrease. This told us that the collapsed voids created by bio-degradable materials were being ?lled and consolidated, and that the natural expansion of the grout was rebuilding solid mass back into the substrate. The process took just five days and the highway remained open the entire time. Tunneling resumed after the initial grouting had taken place and it was deemed safe by Barton Southern and the D.O.T. After the soil stabilization process was complete, a paving contractor milled and inlayed the remaining dip in the pavement creating a once again smooth and safe roadway for the public. The work passed D.O.T. inspection and the tunneling project was completed shortly thereafter.
Benefit: Chemical grout injection for the purpose of soil stabilization, in this case, saved the pipe contractor time, money and public scrutiny. An open ditch restoration, which was the alternative solution to this problem, would have taken considerably more time and money to complete, not to mention endless aggravation from the motorists that rely on this stretch of highway to get to and from work. After the soil stabilization process was complete, a paving contractor milled and inlayed the remaining dip in the pavement. Once again the public had a smooth and safe roadway.
About Prime Resins: Established in 1982, Prime Resins manufactures polyurethane foams, epoxy injection resins, and polyurea coatings. With in-house R&D labs, formulation, packaging and technical support offered 24/7, Prime Resins has everything customers and partners need to help solve problems. Specified by engineers, injected by specialty contractors, and distributed through building suppliers, Prime Resins products are used primarily to stop leaks, stabilize soils, strengthen and protect concrete. For more information about Prime Resins, please click the link below to visit their website, or call 855 875 7612.