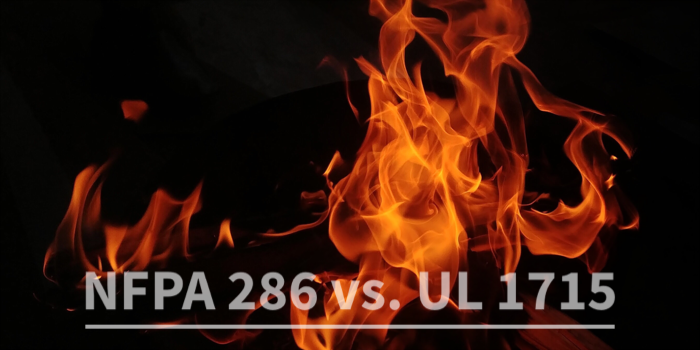
NFPA 286 and UL 1715: What’s The Difference?
IRVINE, CA – October 9, 2019 – In the world of material testing, there are many tests which seem to be identical or very similar. Room corner tests are no different in this regard. For example, many blur the line between NFPA 286 and UL 1715 referring to them as identical when, in fact, they are quite different in the methodology and examination of the results.
Brad Glazier, Technical Director and Vice President of Testing and Accreditation at International Fireproof Technology Inc. (IFTI) explains, "These differences between NFPA 286 and UL 1715 are why we choose to test our DC315 to the more stringent NFPA 286 in lieu of UL 1715." DC315 is IFTI's intumescent coating 15-minute thermal barrier and Ignition barrier fire protection of spray foam insulation.
NFPA 286 is a life safety test and widely known as the defacto room corner test (also referred to as the interior finish test or 286 or Appendix X, etc.). The room itself is constructed as specified by the standard but in general incorporates an eight (8) foot by twelve (12) foot room, drywall lined stud walls and joist ceilings with the cavities full-filled with either open or closed cell spray foam.
NFPA 286:
The thickness of foam installed is required to be the maximum thickness for which certification is sought, in other words you can’t install 4” of foam and be approved over 8” of foam. The foam is installed in the full area of the walls and ceilings to completely encase the room with foam. Of particular note - ALL of the foam in the 286 room is exposed to the fire, there is no drywall covering any portion of the foam.
The room has a calibrated gas burner which must be placed in full contact with either of the two back room corners (opposite side from the door) and is computer controlled to ensure consistent flame intensity and heat output from test to test. Instrumentation wise, the room has six (6) thermocouples mounted in the ceiling at the exposed face of the foam and one (1) thermocouple over the door to measure room temperatures.
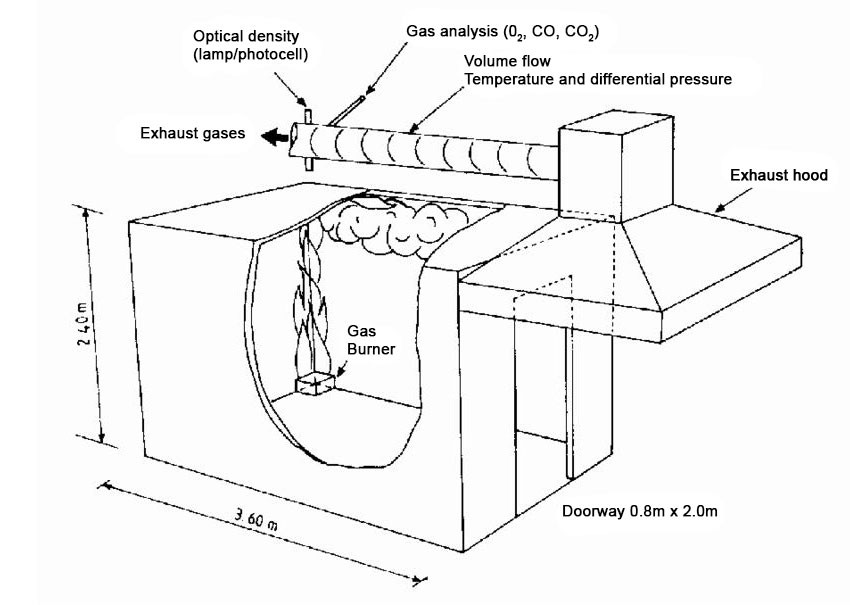
There is a radiometer on the floor as well as paper targets intended to give a visual observation of spontaneous combustion. There is a large exhaust hood over the door with a ducted exhaust system containing a light sensor continually checking smoke output and density, along with gas monitors to measure O2, CO and CO2 in the smoke plume. The entire process is filmed for archival purposes as well as closely monitored with specific software that is recording the data from the thermocouples, radiometer, flame source, smoke development, and timers.
The burner is ignited, and the fire is brought rapidly up to the prescriptive heat output of a 40kW fire, essentially simulating a trashcan fire in the corner of a room. This burner heat output lasts for 5 minutes (note* stop here for Appendix X compliance as an ignition barrier) for a full NFPA 286 test, the burner is then increased to 160kW for an additional 10 minutes. The full 15-minute-long test is what is required to be considered an alternative thermal barrier.
The pass/fail criteria on NFPA 286 is not subjective in the least. Failure criteria are clearly defined in Building Codes and includes ANY of the following criteria –
- the fire hits the ceiling during the first 5 minutes,
- the flame reaches the extremity of any wall or ceiling,
- part of the fire reaches or crosses the door threshold – termed “flamesout the door”,
- thermocouples show a heat rise over a specific targeted number, or
- the smoke discharged is in excess of the tolerance allowed.
Any of these criteria occurring would cause a failure of the test.
NFPA 286 is very prescriptive in the build, burn, and analysis of the data received. There is zero wiggle room with the numbers and no way to legitimately have the results open to interpretation or overridden by a third-party engineer… the data speaks for itself and is a very clear statement of passing or failing the test.
UL 1715:
By comparison, the UL 1715 test is also a life safety test, considerably less structured, and much ‘easier’ to pass. The room is constructed similarly to the NFPA 286 with a few glaring differences. For example, 1715 allows oversized framing where the stud cavities do not need to be fully filled with foam. Why does this matter? The oversized framing and less than full filled cavities provide fire breaks trapping the fire in the cavities as opposed to allowing the fire to ‘see’ all of the foam surface. The framing members are allowed to be installed parallel to the front wall containing the doorway to restrict the ability for the flame to spread across the foam surface. Further, there are only exposed foam cavities along the eight (8) foot wide back wall and the first eight (8) feet of a single twelve (12) foot long side wall. All of the opposite wall and the last four (4) feet of the foamed wall and ceiling are covered with either drywall or calcium silicate board…. both non-combustible materials. The image below shows the eight (8) foot by eight (8) foot area of the specimen along the back and side wall located within the overall room.
The flame source in the UL 1715 room is a stacked wood ‘crib’ which is placed in the back corner but is allowed to be spaced away from the wall instead of in full contact as in NFPA 286. The wood crib is lit and allowed to burn at an unspecified rate and intensity – in other words, there is no way to regulate the temperature rise, intensity, or duration it all depends on how the wood burns.
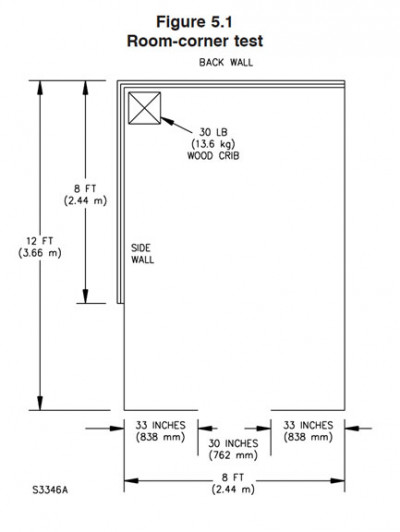
Fire test of interior finish material - UL 1715
There is also a risk of a ‘cool’ fire or something less than a prescriptive 40kW fire, plus the fire is spaced away from the wall resulting in a less severe thermal attack on the foam. Monitoring the fire is also less restrictive using only an instrument tree along the back wall behind the ‘crib’, this temperature tree is only there for information and not to show any required fire rate. There is no in-room monitoring, no radiometer, no paper targets, and no monitor over the door. Further, there is no smoke hood required for the test so there is no measurement of smoke development collected, observed, or reported. The only method of failure specifically stated in the standard is flames shall not exit the door or spread to the extremity of the sample. Remembering the last 4’ of the room towards the door is covered in non-combustible material and contains no foam there is an inherent barrier to flames being able to even reach the doorway, essentially meaning the foam can be on fire, the heat can exceed the temp limit under the 286, and as long as the fire doesn’t exit the room it is a pass. Considering the intent of the protective covering is to delay the involvement of foam from contributing to a fire one has to question if this even comes close to demonstrating that intent has been met.
Finally, the pass/fail result is highly subjective with the main decision riding on the observation of the video archive of the test as viewed by a third-party observer determining if the amount of smoke created/released could be considered “High” what does that even equate too? Your interpretation of high levels of smoke could be totally different than mine, or the observer so who is right?. This methodology is highly subjective, depends on the video quality, computer monitor quality, lighting, and observation(s) of the third-party.
Glazier concludes, "We at IFTI Take life safety seriously. VERY seriously. Why would we want to test to a looser standard, a more subjective test, and one that is ‘easier’ to pass? We firmly believe in testing to the more stringent NFPA 286 methodology. Lives are at stake and we always err on the side of caution and conservatism when it comes to life safety. Sacrificing this is not justified by seeking a cheaper price."
Following is a side-by-side comparison of some major differences between NFPA 286 and UL 1715.
NFPA 286 | UL 1715 | |
---|---|---|
Room Information | All cavities of the wall and ceiling are fully filled in with foam; no wall areas are covered by gypsum board or calcium silicate | Oversized framing members with cavities allowed to be half-filled allowing a type of firebreak to exist; roof framing is perpendicular to the flame source and again not fill filled cavities allowing firebreaks to exist; the last 4’ of the 12’ walls are coveredwith gypsum board or calcium silicate; |
Flame Source | Gas fed, calibrated, computer- controlled burner capable of a 40 kW (+/- 1kW) up to 160 kW flame(+/- 5kW) | 30-pound wood crib |
Fire Characteristics | Flame is computer controlled to ensure standard burn characteristics. Exact duration and rate/flame intensity arespecified. | Wood crib is ignited with accelerant and allowed to burn at an unspecified rate and duration. Potential for a ‘cool burn’ with indirect flames on the specimen wall and/orceiling. |
Thermal Monitoring | 4 thermocouples mounted in the ceiling; 1 over the door; in-floorcalorimeter. | Single “TC” tree in room corner; no temperature or heat output minimum |
Instrumentation | 4 thermocouples mounted in the ceiling; 1 over the door; in-floor calorimeter; paper targets on floor. Smoke hood is required | No in-room radiometer or paper targets used; no way to measure flashover potential or secondary ignition of other elements in the room; smoke hood measuring smokerelease is optional for use |
Pass/Fail Criteria | Via instrumentation during/post burn as well as visual observations including ‘fire out of the door’. Mass flow rate of combustion gasses; smoke measurement; burner gas flow; time history of the Total Heat Flux to Floor; Time history of the Fire Growth; Time History ofSmoke Obscuration; | NO heat failure in 1715; nearly impossible to have ‘fire out of the door’ failure as there is gypsum/calcium silicate board present in the last 4’ of the room by the door; PASS/FAIL determined via video playback which is highly subjective and depends on video equipment, playback equipment, and viewers’ expertise level; use of smoke hood is optional and rarely used |