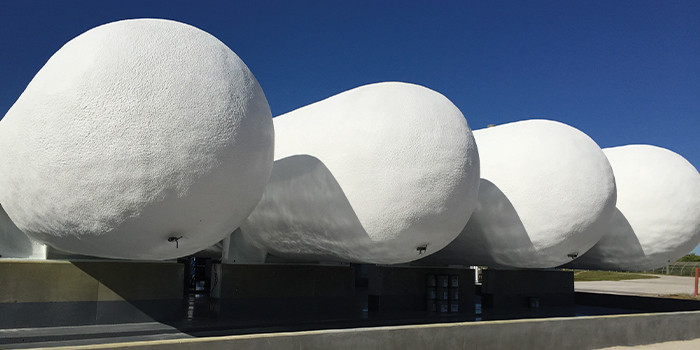
More Space for Tanks
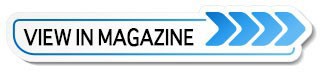
Spray Foam Magazine – Late Summer 2022 – Dreaming of heading to space is a reality for the lucky few who have been hand-picked by space enterprises to go on these missions. What part is spray foam playing in the quest of heading to the stars? A spray foam contractor on the Space Coast, whose hard work and determination, is taking our technology through the stratosphere.
Central Florida Spray Foam LLC is an owner-operated local business doing their fair share to deliver professional spray polyurethane foam insulation services in Central Florida. They have worked in polyurethanes, polyurea, and numerous waterproofing and coating materials for over 20 years, and it’s this experience with specific materials and machinery that ensure they provide the highest level of service and quality. They have worked on at least 10,000 homes, hundreds of steel structures, and thousands of additional commercial projects. This project was concentrating purely on tanks, and although the identity of the customers cannot be divulged, these tanks were connected to the aerospace industry. The application of spray foam within this industry has increased since the race to space in the private sector has taken off.
Anyone who has ever sprayed a tank will appreciate the workmanship that goes into getting the job done perfectly. The aerospace industry in Florida has used spray foam in some manner since the 1960s. Whether it’s spraying a shipping container, metal building, or items on launch pads and rockets, the material is the same. When using fuels of any kind for propulsion, thermal barriers are most always a requirement, and spray foam is increasingly used in these kinds of projects.
These fuel tanks were for an aerospace customer on the Space Coast of Florida, and a very precise application was required. Closed-cell is often used for exterior thermal protection due to it being vapor semi-impermeable, rigid, and able to withstand greater pressure. It’s four times denser than open-cell foam, resulting in the right choice for these fuel tanks. SPF will provide thermal protection for every rocket part, big and small, including these tanks.
The fuel that powers the rockets must also stay extremely cold to remain liquid. If these cryogenic temperatures rise too high, the fuel will become a gas and it could lead to a failure.
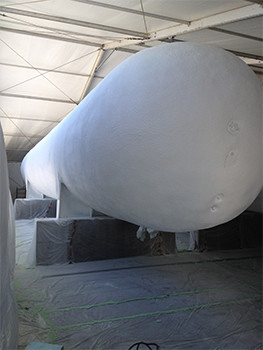
Christopher Paoli and his crew from Central Florida Spray Foam LLC have completed several tanks around the same complex for different companies. However, these four tanks were particularly interesting and challenging to the crew due to the crew having to have security clearances, the periodic adjacent launches that required them to evacuate the site, the safety training, and the size of the project.
On the site, there were aerospace technicians checking the crew periodically to make sure the job was moving along accordingly. Paoli emphasizes, “When we deal with these rocket techs, they’re usually half my age, but ten times as smart. So, we normally hand them the Technical Data Sheet (TDS) and let them pick and choose a foam or polyurea/coating of their liking since they’re also concerned with tensile and compressive strengths.”
Before starting the job, the crew washed down the tanks from any debris following their road travel across the country. After the tanks dried in the Florida heat, the crew then prepped the floor and pilons with plastic. They also had to cover the valves and instruments on the exterior for future access. The rocket fuel tanks also needed a 40-ft high, 7000 sq.ft. circus tent to cover them from the wind and rain showers of Florida’s East Coast. This was challenging to the crew due to the overspray having the potential to ruin the sidewalls of the tent. Their solution to this was to ask their local tent company to supply them with the oldest, yet most waterproof tent they had, and they obliged.
For this project, the tanks were going to be used to hold fuel for rocket launches. They were approximately 70 ft. long, 4.5 ft. off the ground, and 12 ft. in diameter. They needed approximately three inches of closed-cell foam to be applied and a protective coating to help shield the tanks from the hot Florida sun and the torrential rainstorms. The technicians decided to go with Paoli’s recommendation of Demilec’s Heatlok Soy 200 Closed-Cell and Lapolla’s RCS 600, both now under the Huntsman Building Solutions label.
To keep these future tank jobs going elsewhere, Paoli had to ensure the tanks were perfectly sprayed so he hired an old friend from Northern California, Ernesto Gaytan. Gaytan has decades of experience spraying tanks for the wine industry with insulating foam and makes the process look easy. His only request to Paoli was that he purchase a Graco GX-7 spray gun to ensure a smooth round pattern. Paoli usually sprays with the typical Graco Fusion AP gun, but as Paoli stated, “This job called for a sustained perfect pattern with little down time for cleaning.”
The crew applied approximately 10 to 12 sets of foam, with one complete set calculated to be on the ground stuck to the plastic from the overspray of feathering the foam onto the tank. The crew found it hard to keep track of the exact total material usage because they were spraying smaller items on site at the same time.
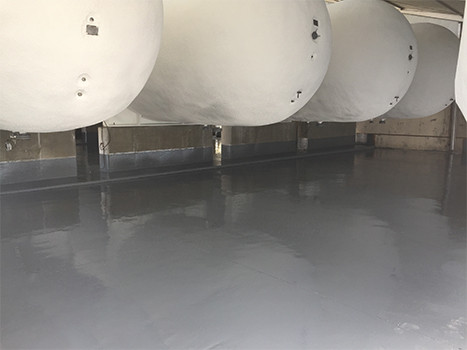
Roughly three inches of closed-cell foam and a protective coating were applied to the tanks to protect them from the sun and extreme weather. After the foam was installed, they also added the containment coating to the ground to protect against a possible tank rupture.
The crew learned very quickly that a quick flash of foam from a six to eight feet setback is a good way to lay a base layer of super thin foam to adhere the next three inches without bubbling or peel back. Especially since the inside of the tanks were cooler than the ambient air. The topcoat applied was a typical elastomeric from Lapolla of which the crew added at least three heavy coats. This was applied with a Graco 695 airless sprayer with the filters removed.
After the foam was installed, they added the containment coating to protect the ground from a possible tank rupture. That was applied with a roll on two-part Polyspec 100EX epoxy primer and topped with a two-part Polyspec Thiokol FEC 2233 flexible epoxy coating that cured within minutes.
The job took the aerospace technicians a week to complete. Every few years the crew will conduct maintenance by doing exploratory holes to see if there is any surface corrosion and if so, Paoli will quickly patch it up and coat it.
The crew completed the tank job to a high standard using the correct material and a precise technique. Leaving the client’s technicians very impressed with the results. The crew has since worked with numerous local aerospace companies. Proving that if a job is done well, completed on time and within budget, they always ask you back.
Paoli summarizes the experience of working on this project by saying, “It’s a neat feeling to know that people who have left the earth are utilizing the benefits of the spray foam insulation and coatings that we provided.”