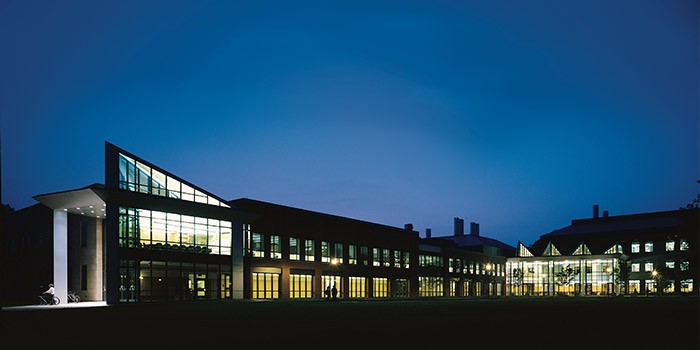
Inside and Out
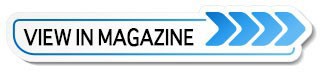
OBERLIN, OH – May 3, 2018 – Oberlin College and Conservatory is more than just a mere collegiate institution, it is a hub for the arts located 35 miles southwest of Cleveland, Ohio that rounds up numerous creative beings from all parts to fine-tune and exploit their talents. The college highlights one specific, inspiring motto: “Think one person can change the world? So do we.” Ingrained in Oberlin’s DNA is music, as they boast having one, if not the only, music program in the country that focuses exclusively on undergraduate education, and their College of Arts and Sciences includes over 50 different majors, minors, and concentrations for undergraduate enrollment of approximately 2,895 students.
But it’s not only the students that are making a difference in the world—it’s the campus itself. In 2006, Oberlin became one of the charter institutions to sign The American College & University Presidents’ Climate Commitment (ACUPCC) and set a target climate neutrality date for 2025. Therefore, many of the buildings within the 440-acre suburban campus have been either built or renovated with sustainability in mind since then. Recently, they added one more building to that list. Oberlin’s Health & Wellness building was having a 12,000 square-foot addition to their fitness center that specified for, among several energy-efficient materials, spray foam insulation (SPF).
The insulation contractor that performed the SPF installation for this addition, OCP Contractors Inc., had actually already insulated three other buildings within Oberlin’s campus over the course of the past five years. OCP’s unique and effective insulation package that involved the application of SPF to the inside and the outside of the building had proven to seal the building envelope of each structure and increase its energy efficiency. Evidently, the school was pleased with the results. It was Oberlin’s job to maintain their streak and keep SPF’s reputation intact in the process.
NCFI’s InsulBloc closed-cell spray foam was installed to the exterior of the building; The interior open-cell SPF application provided a greater R-value for optimal building performance
“The purpose of this job was to create a continuous building envelope on the new portion of the building,” says OCP’s Project Manager, Matthew Giambrone. “Having worked on a few others buildings in the Oberlin campus, they really liked the way our system performed and made sure to include spray foam in this addition’s specifications.”
The system in question was comprised of two types of SPF formulated by NCFI Polyurethanes: InsulBloc, a 2 lb. closed-cell SPF, applied to the exterior of the building, and Sealite 0.5 lb. open-cell SPF on the interior of the building.
Giambrone explains the system’s efficacy. “The closed-cell spray foam has a high R-value per inch, so it decreases the size—if you will—of the cavity of the building and it provides a vapor barrier, so it essentially allows you to create a continuous building envelope in one step. The open-cell spray foam on the interior further adds a higher R-value per inch, as well as an airtight seal to the building from the inside by filling the wall cavities between the studs completely. NCFI provides materials of exceptional quality, which is what makes this system perform so well; we thank them for their continued support.”
But that’s not the only materials that OCP used during the project. As a matter of fact, the crew got technical and specific with detail work prior to the foam application. They core-drilled holes into the top of the steel beam underneath the window heads, and applied Fomo’s Handi-Foam Channel Fill Pour-In-Place foam, filling the inside of the tube steel to eliminate thermal breaks. On the outside, the OCP crew installed Prosocco’s Fast Flash, a moisture-curing liquid flashing membrane, that was used to detail around the windows, doors, penetrations, and blocking.
“Detailing with the liquid flashing membrane on the exterior is important so that when we spray foam we make a connection to the membrane. When the openings get set, all the glazer had to caulk the window to achieve a complete and continuous building envelope with that system,” notes Giambrone.
The exterior of the addition had a liquid-flashing membrane installed that would connect with the spray foam to form a continuous building envelope
The application took a total of five weeks to complete —and the weather changed drastically during that time period. The job was completed with two men manning one rig, which was equipped with a Graco E-30 proportioner, a Graco Fusion AP gun, and 300 feet of hose. The crew utilized 20-foot electric scissor lift with fall protection to work from the floor to the higher areas along the ceiling on both the interior and the exterior applications. The crew wore PPE consisting of Tyvek coveralls, powered air-purifying respirators (PAPRs) units connected to their hard hats, gloves, and no-cut boots during both phases of the project.
"There’s no question that this system is going to provide the type of savings that are not possible with any other material."
The OCP crew completed the SPF application to the exterior of the building first before the winter season. They prepped the outside of the building by cordoning off the entire area with caution tape and covering structural exposed columns, fixtures, and other workers’ staging areas with plastic sheeting to prevent overspray damage. They installed two inches of InsulBloc to the exterior perimeter of the building, which included the Bison board walls and the overhangs of the metal roof deck. The two-inch depth of InsulBloc provided structural rigidity and nearly an R-14 value to the exterior of the building. While spraying, the crew kept an idea of wind speeds and would halt the application altogether if conditions weren’t favorable. By the time they had finished the exterior application, they had gone through six sets, which equates to 24,000 board feet, of InsulBloc and the cold weather had set in and snow had hit the ground.
“We sealed directly to the decking from the exterior and encased the beams that came through with the closed-cell foam to eliminate any thermal bridging into the building,” explains Giambrone.
Oberlin College and Conservatory of Music hosts well over 500 concerts and performances a year. While taking a stroll through the campus, you might hear sounds from all different kinds of music genres coming from the buildings, from classical to rock—even acapella performances out in the open.
Giambrone recounts that because of the superior insulation that the closed-cell on the outside provided, the crew was able to heat the inside of the building with ease before the insulation application got underway. The crew used three-mil plastic sheeting to close off each respective spray area they worked on from other trades working onsite and further used the sheeting to cover the temp windows and floors of each area for overspray damage protection. They also placed industrial exhaust fans around the site to for ventilation. In addition to this, OCP opted to have their crew only work during the second work shift, which started at 2:30 p.m., to avoid having to work around other trades that preferred the morning shift and maintain safety in the workplace. Giambrone notes that OCP had the whole building to themselves in the afternoon.
“Working during the second shift allowed us to work without disturbing any other trades and reduce downtime and safety concerns while working inside,” affirms Giambrone.
Then, after executing a changeover from closed-cell to Sealite open-cell foam in their E-30 proportioner, the OCP crew proceeded to apply four inches of foam to the exterior walls, utilizing four sets of Sealite in total. The total spray area of the application encompassed 24,000 square feet.
The combination of closed-cell and open-cell foam continues to provide the results that are conducive to the quality standards that Oberlin besets as a significant proponent of green building and sustainability. As far as cost-effectiveness and energy efficiency is concerned, the insulation properties of this fitness center addition will produce remarkable results, according to Giambrone.
“There’s no question that this system is going to provide the type of savings that are not possible with any other material,” says Giambrone. “The system will pay for itself in under three years. It’s going to contain moisture and air infiltration, and it’s going to provide a comfortable indoor environment for gym goers and students that work in the wellness center.”
For more information, visit www.ocpcoc.com and www.ncfi.com.