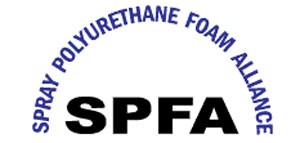
ICC-ES Approves New Fire Test Protocol for Spray Applied Polyurethane Foam in AC377
Birmingham, AL. June 3, 2009, the International Code Council Evaluation Service (ICC-ES) approved changes in AC-377, Acceptance Criteria for Spray Allied Polyurethane Foam. This approval had the effect of sun-setting a previous fire testing method and implementing a new one, with phaseout milestones extending to December 2010.
The new fire testing protocol, an NFPA 286 test modified for the purposes of testing alternative ignition barriers for SPF, becomes one of several available tests recognized within the AC-377.
This document will provide a background of the issue, as well as a summary of the outcome. It is also available for pdf download at www.sprayfoam.org/ac377.
Background
In 2000, a letter from ICC-ES defined the fire test baseline configuration using fiberglass batts in the SwRI 99-02 test procedure (one of several procedures available). The testing laboratories conducted these tests with the kraft facing towards the fire side of the test module. Spray foam outperformed this product in comparative tests and received approval for this application in Evaluation Services Reports (ESRs). It was later determined that the fiberglass assembly represented a non-code-compliant assembly for baseline testing purposes. The test eventually lost support and a new test protocol was desired.
The Industry Challenge
Nearly eighteen months ago, International Code Council Evaluation Services (ICC-ES), the division that manages product acceptance criteria and evaluation, came to SPFA with a challenging request: Lead the industry to resolve existing issues with a fire test used to qualify SPF for attic and crawlspace applications. SPFA answered the call, creating a task force of more than 43 contributing members, representing 24 member companies.
This task force, lead by Mac Sheldon of Demilec USA LLC, first negotiated a 1-year interim testing solution accepted by ICC-ES which went into effect in June 2008 (see the Appendix B '3/12' criteria added to AC-377). This interim test was a step in the right direction, removing much of the test's variability and simplifying interpretation using a time-based pass/fail criterion. This approach proved to be a precursor to the final industry protocol. With the deadline of developing a more permanent testing solution by June 2009, the task force went into full gear in the summer of 2008.
The Industry Solution
Understanding that a new method to qualify alternative ignition barrier systems was needed within a year, SPFA hired fire testing consultant Jess Beitel of Hughes Associates. Working under Mr. Beitel's expert guidance, as well as in concert with permanent ICC staff engineer liaison Si Farvardin, the task force considered several options including small-scale qualification tests, room-corner burn tests and full-scale attic mockup tests. Realizing the need to have a repeatable, reliable test method ready to go in less than a year, the task force agreed by consensus to use an existing room corner burn test (NFPA 286) with a few minor refinements.
In October, SPFA received pledges totaling $150,000 from 16 supplier members to support the testing program and consultant fees. From November of 2008 through January 2009, three series of fire tests were performed at Southwest Research Institute in San Antonio, TX. Tests included evaluating low and medium density wall foams with intumescent coatings (code-approved alternative ignition barriers), as well as a code-prescribed ignition barrier (1/4" plywood). The research program also investigated different burner spacing and flame sizes. All variables were considered and debated among all parties involved to assure development of the most comprehensive test possible.
After review of the test results, the task force developed a new test procedure in February 2009. The result was a test that provided consistent scientific data to define the baseline performance of a code-prescribed ignition barrier - in this case a ¼" plywood ignition barrier over SPF baseline to comparatively test alternative ignition barrier coatings.
This established baseline sets the standard by which all alternative ignition barrier systems can be measured: If the modified NFPA 286 test of the alternative ignition barrier takes longer to flash over than the plywood baseline (4 minutes and 18 seconds), then the system can be used in all attic and crawl space applications regardless of size or geometry. The net result to the industry is that suppliers will no longer need to test baselines every time they qualify a new ignition barrier system - the common baseline has been established. It also makes it easier for code officials to interpret ESRs, since successfully passing this test allows the system to be installed in any attic or crawlspace regardless of size or orientation of the interior surface.
Review & Hearing Outcome
The Task Force finalized the test procedure proposal in March 2009. This final proposal was agreed to by a consensus voting process - one member/one vote. It received internal Task Force approval, was reviewed by the Building Envelope and Technical Committees, and was unanimously endorsed by the SPFA Board of Directors. Once the procedure was finalized, it was sent to ICC-ES for review in early March. During the month of May, it entered the public
review process. While in public review, the proposal received endorsements from the rest of the foam plastic industry, including PIMA, XPSA, EPSMA and CPI. With a dialog between ICC-ES and the SPFA task force, it underwent minor changes - the source of the final version can be found at: www.icc-es.org/Criteria_Development/0906-pre/memos/AC377-0609_staff_memo.pdf.
Though majority consensus was reached, there was not unanimous support within the SPFA membership regarding this proposal. A minority of SPFA members were in favor of delaying adoption of the proposed test while a new full-scale test method could be developed. But due to the timeline expectations of the ICC, as well as the substantial additional cost, complexity and duration of additional alternative testing, it was determined to move forward with the current proposal and agree to examine further options.
On June 3, ICC-ES held a hearing to review this proposal In Birmingham, AL. The hearing committee consisted of more than a dozen building code officials from around the U.S. In addition, the hearing was well attended with representatives from 15 SPFA member companies. In addition, two staff from SPFA and a representative for CPI were present. After hearing several hours of testimony from both the proponents and opponents of the proposal, the hearing committee unanimously agreed to approve the change.
What's Next
As presented in several Spray Foam Magazine articles and as presentations during the Spray Foam 2009 Conference, the new test procedure adopted for AC-377 will have an impact on how SPF products are approved for attics and crawlspaces.
The new test became part of AC 377 immediately. Until June of 2010, either Appendix A or X can be used. After December 31, 2010, Appendix A 1.2 will sunset (be removed), leaving only Appendix X.
Additionally, ICC-ES has established the following sunset schedule for attic and crawlspace test data and ESR updates:
- As of June 1, 2009, ICC-ES will no longer accept test data based on the '3/12' interim criteria or Appendix B (per decision during the ICC-ES June 2008 hearing)
- As of December 31, 2009, ICC-ES evaluation reports (ESRs) that use test methods that are based on either a crawlspace comparative test in which the baseline test was kraft-faced fiberglass or a crawlspace test with the "3/12" conditions of acceptance, will be modified to delete the section(s) of the report that are based on this testing.
- On June 1, 2010, the testing requirements described in Section A1.2.2 will expire, and ICC-ES will no longer accept ESR applications using this test data after that date. ESR's written to this standard will be valid until December 31, 2010. All applicable evaluation reports will be revised by December 31, 2010 to delete assemblies based on this testing. Report holders can submit data from new test methods (A1.2.1 or Appendix X) to attain compliance with the new standard.
The recent changes to AC-377 do not specifically require that all foams must be covered with intumescent coatings - it simply provides a method to compare foam systems to code-prescribed ignition barriers. While the outcome of the June 2009 hearings will set the standards for attic and crawlspace fire testing for the next several years, SPFA will continue to work with its members to refine these test methods, as well as examine the viability of other new tests (including examining possible tests for full attic assemblies and attic floors). SPFA members interested in becoming involved in this continuing development process should contact Rick Duncan, SPFA Technical Director. Please direct inquiries on ICC-ES or ESR specifics to an ICC-ES staff engineer.
Conclusion
Knowing that the industry will continue to grow rapidly, now was the time to address this complex task. The code for foam plastic insulation is already very demanding, and the industry acknowledged that SPF has fantastic performance capabilities and a track record of being an extremely safe product. Still, members agreed upon a testing change that raises the bar even further for SPF resulting in product fire testing that is more advanced and comprehensive than the testing other similar-application building products must endure. Even with the added requirements, the SPF industry is so confident in the value-proposition of SPF and the technological advancements in product development that it foresees continued growth and increased customer satisfaction and safety.
For additional resources, ICC Reasoning Statement, a downloadable document format covering the content of this email, and information on this, or other code issues please visit www.sprayfoam.org/ac377.
Sponsors
This important project, as well as the required several-rounds of 3rd-party fire testing, was possible only through the foresight and contribution of SPFA member companies, their funding and time commitment, and the partners that SPFA worked with.
TIER I Sponsors:
BASF
BaySystems
BioBased Insulation
CertainTeed
Demilec USA
Dow
Foametix / Burtin Polymer
RTC / Henry
Honeywell
Huntsman
Icynene
Lapolla
NCFI
TIER II Sponsors:
Aldo Products
Flame Control Coatings
Preferred Solutions (PSI)
Special Thanks
to Mac Sheldon, Demilec USA for his leadership Chairing the SPFA Task Force.
to Jess Beitel, Hughes Associates, for his expertise and patience.
to Si Farvardin, ICC Staff Engineer for his time spent working with the Task Force.
to SwRI Testing Labs for working with the industry to complete these challenging tests.