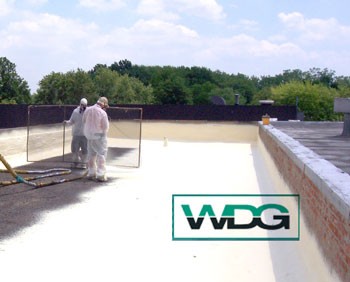
How Green is Green? - Using LEED to Measure Spray Polyurethane Foam (SPF) and the Green Roofing Market
February 24, 2009 - LaGrange, OH - What do most people visualize when they hear or read the phrase green roofing? Usually it conjures up images of an aesthetically pleasing roof on top of a building in an urban area covered with soil and vegetation. Or maybe one thinks of an array of solar panels. Are either of these examples the ultimate in green roofing?
Maybe not; let’s consider a few questions first.
What materials were used as the waterproofing membrane or the insulation? What is the life cycle of the roof? What was the carbon footprint of the installation, the cost, and the amount of necessary on-going maintenance? What is the roof’s long-term viability? As you can see, there are many shades of green.
What is the definition of green in the construction industry? Is it a roof with vegetation, or a roof with solar panels? Yes and yes. But is there a textbook definition? Not one that I’m aware of.
To paraphrase what U.S. Supreme Court Justice Potter Stewart famously stated in 1964, he could provide no better definition for obscenity other than, “I know it when I see it.”
The same line of thinking can be applied to defining a green roof. Each person has his or her own idea of what is logical. Most people use logic to determine what is green and what is not. Clearly defining the green aspects of a product or system – in this case, roofing – with supporting documentation helps make the product or system a logical choice for those who want to be ecoLOGICally correct.
Logic, however, isn’t always enough for choosing or measuring the positive effects of green technology. Recent advancements in green design and construction practices are blurring the dividing line between urban park space that is ecologically beneficial and buildings that are often ecologically harmful. But the question remains, how do we measure and quantify green advancements?
Leadership in Energy and Environmental Design (LEED)
The most widely used method of measuring greenness in the construction industry is LEED. Government entities, architects, engineers, developers, and specifiers use Leadership in Energy and Environmental Design principles to measure greenness. The LEED Green Building Rating System is governed by the U.S. Green Building Council (visit their web site at www.USGBC.org to get information and to locate the chapter near you).
By following LEED construction principles, a building can be rated for its greenness. If it meets enough of the criteria on the checklist, it is awarded a LEED certified status. Obviously, green buildings are good for the environment, but additional benefits of going green include lower operating costs of buildings (e.g., better insulated building mean less energy use), increased overall value of buildings, increased resale opportunities, possible tax incentives, and access to construction grant money.
LEED Certification Process
LEED Certification Process
|
To earn LEED certification, a project must satisfy all prerequisites and a minimum number of points outlined in the LEED rating system. There are two LEED checklists of design considerations that are used to determine the total number of points earned: LEED for New Construction (v2.2) and LEED for Existing Buildings (v2.0). There are six primary categories:
1. Sustainable Sites
2. Water Efficiency
3. Energy and Atmosphere
4. Materials and Resources
5. Indoor Environmental Quality
6. Innovation and Design Process
Architects and builders try to get as many LEED points as possible from all aspects of the building. Until now, roofs typically contributed to the heat-island effect and, occasionally to the regional manufacturing credit. But today, green roof systems, such as the West Development Group (WDG) System 14?, contribute to a building’s LEED status in multiple ways.
Let’s examine the possibilities of using a soy-based, spray foam (SPF) insulation and a silicon/EPDM roof system coating.
Sustainable Sites – Within this category, LEED addresses the heat island effect. Traditional roofing materials absorb the sun’s radiation and release it as heat, sometimes making our cities as much a 7 degrees Fahrenheit warmer than surrounding areas. The intent of this credit is “to reduce building heat islands to minimize impact on microclimate and human and animal habitat.” To earn this credit (1 credit point), a roof must have a Solar Reflective Index (SRI) of 78 over at least 75% of the building’s roof.
WDG’s System 14 qualifies with a reflectance of 80.67% and emissivity of 0.94. Many coating manufacturers provide SRI data about their products as well.
Energy and Atmosphere – LEED’s minimum energy performance prerequisite establishes a minimum level of energy efficiency for the proposed or existing building and systems. Up to 10 credit points are available under the Optimize Energy Performance within this category, which was set up to achieve increasing levels of energy performance beyond the baseline in the performance prerequisite standard. The intent is to reduce environmental and economic impacts associated with excessive energy use. Because of its high thermal value, lack of fasteners, seams, and a range of positive attributes, spray foam is a valuable component in a building’s design to help the building achieve optimum energy performance.
For example, SPF dramatically improves a roof’s insulation value with an R-value of approximately 6.25 per one inch of thickness, providing more thermal resistance with less material than other roof systems.
Materials and Resources – One credit point is available for Construction Waste Management. The LEED intent is to divert construction, demolition, and land-clearing debris from disposal in landfills and incinerators. This helps redirect recovered, recyclable materials back to the manufacturing process and appropriate construction sites. SPF can contribute to this process in many ways. System 14, for example, uses spray foam and silicone coating products that are fluid-applied, producing minimal construction waste. Some SPF coatings, such as those produced by WDG, use recycled construction waste (e.g., EPDM) in their systems to reduce overall waste to landfills. Some manufacturers also recycle and/or refill material drums. WDG’s System 14 silicone membrane contains 16.5 % recycled EPDM recovered from roof demolition and diverted from landfill disposal.
Using this recycled material gains credit points for the Construction Waste Management (as noted above), Material Reuse, and Recycled Content categories.
Two points are available for Material Reuse of building materials and products in order to reduce both the demand for virgin materials and the amount of waste. An example of significant reuse is the recycled content used in WDG’s spray foam, which is greater than 10% post-industrial material. The silicone membrane is 16.5% post-consumer EPDM. Aged EPDM from an existing building is ideal for use in coating applications because roofing EPDM is formulated for exposure to an outside, harsh environment that includes UV rays, ozone, water and ice, etc.
Up to two points are available for Recycled Content. As illustrated with the examples above, both SPF and the membrane coatings may contain a substantial percentage of recycled materials to help reduce the negative impacts of ever-larger landfills and the extraction and processing of virgin materials.
New, green roofing systems also deliver LEED points in the categories of Regional Materials and Rapidly Renewable Materials. To help increase the demand for building materials and products extracted and manufactured within the region, two points are available for buildings that use indigenous resources that reduce environmental impact resulting from transportation. Reviews are done case by case and materials must originate within 500 miles of the building project (up to two points).
One LEED point is available for replacing finite raw materials and long-cycle renewable material with rapidly renewable material. A WDG example of complying with this category is the company’s spray foam, which is manufactured from soy-based polyol in lieu of petroleum-based polyol. Approximately 25% of the standard polyol used in the insulation manufacturing process is renewable. To provide environmental benefits and to offset the continually rising cost of petroleum, other manufacturers are also making SPF with agricultural-based polyols and surfactants.
Innovation and Design – This category, which is worth one to four points, is an opportunity for design teams and projects to be awarded points for exceptional performance above and beyond the LEED rating system and/or innovative performance in green building categories not specifically addressed by the LEED system.
Innovation and Design credits provide architects, engineers, and specifiers to opportunity to promote the exclusive merits of SPF roof systems. Contractors, when they call on customers, now have a way to measure and illustrate how green SPF roofs are.
SPF has these measurable qualities when compared against other roof assemblies:
- Life Cycle (once installed, recoating and not recycling)
- Reuse of Existing Roofs (limited tear off)
- Variable and Renewable Raw Material Sources (e.g., soy)
- Superior Energy Efficiency (seamless; no fasteners)
- Reduced Freight (carbon footprint – one truckload of SPF is equal to four truckloads of board stock)
LEED Building Status Levels and Green Opportunities
There are four levels of LEED certification. Clearly, SPF roofing systems can earn credits in multiple categories to contribute significantly to a building’s status level:
- Certified (26-32 points)
- Silver (33-38 points)
- Gold (39-51 points)
- Platinum (52-69 points)
There are numerous state, local, and federal programs involved in green construction promotion, including regulations, tax incentives, grants, loans, as well as reduced building permit costs and approval times.
Studies indicate that the value of green building contracts will exceed $12 billion in 2008 and is projected to increase to $60 billion by 2010. By 2009, 80% of corporate America is expected to be engaged in green activities at least 16% of the time, and 20% engaged in green 60% of the time.
Many opportunities exist for SPF roofing professionals. Look for opportunities, especially in major metropolitan areas. Contractors should identify architects, engineers, and specifiers that are LEED accredited professionals. They should also notify government agencies, such as city planners, school districts, and building planner, about how SPF roof systems help achieve LEED certification.
To ensure that SPF green-roof systems succeed for the long term, they must be sustainable. Green sustainability is achievable if the roof system is environmentally beneficial, functionally equivalent to the material being replaced, and economically viable. Using LEED to provide measurable green SPF roof system is good for a contractor’s business, his customers, and the planet.
Contact:
West Development Group
300 Commerce Drive
PO Box 646
LaGrange, OH 44050 U.S.A.
Toll Free: 866.924.4585
440.355.4682
fax 440.355.4276
Email: info@wdgsilicones.com
Visit Website: www.wdgsilicones.com