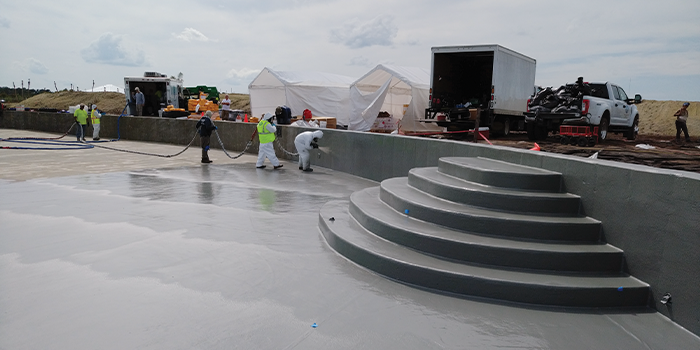
Getting Started in Polyurea
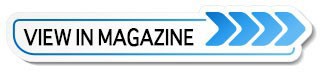
Spray Foam Magazine – So, you want to be in the polyurea spray elastomer coating and lining application business? Maybe you already are, or are in the spray-foam business, or have other coating technology application experience. That’s great! Are you obtaining and using the proper equipment to ensure a successful application? Hopefully so, but there are some issues that most people take for granted that usually end up costing time or money before the project is complete.
Selection of the proper application equipment, surface preparation techniques, auxiliary equipment and proper training will be crucial to application success. Proper organization and pre-application preparation will assist in a professional installation. Remember you are the one making the coating system.
WHAT IS POLYUREA?
The term “polyurea” is still often misused in this industry today. Polyurea, just like Polyurethane or Epoxy for example, is a description of a technology, and not necessarily a coating or lining system. Material suppliers don’t sell “polyurea,” well except for the solid polyurea powder used in grease thickening manufacture and as drilling fluid proppants or fillers. You acquire 2-liquid components and then process these to form the polyurea polymer. So, you the applicator are the one making polyurea.
There are a variety of systems, all designed for specific application areas as there is no “one-size fits all” so to speak. This system can be fast or slow setting; aromatic or aliphatic based (corresponding to UV color stability requirements); elastomeric and non-elastomeric; immersion use or ambient exposure applications; and can be plural spray applied, slow-set joint sealant or hand mix roller or brush applied. And yes, polyaspartic or aspartic ester systems are in fact a polyurea, a decorative, thin-film aliphatic version. Therefore, the selection of the proper systems for the specific application use is crucial. For example, bedliner systems are great as for the designed application, but generally are not suited for high-end application work such as tank lining chemical immersion use.
THE 3-C’S FOR SUCCESS
We often use the terms “applicator” or “contractor” interchangeably, but they are not really the same. With respect to polyurea work, an applicator would be an individual or company that only applies the coating systems. That work is their primary mission, and when large projects come to be, things like surface preparation or repair work is subbed to another trade. A contractor on the other hand has polyurea as part of their complete arsenal of scope of work and may not be applying polyurea system on a weekly or monthly basis. Often, an applicator may in fact have better spray technique and consistency in application over a contractor. Why? Well, an applicator typically has more “trigger time” than the contracting company.
Many years ago, a very wise Malaysian contractor businessman shared with me the secret to success in this business, noted as the 3-C’s. That being Commitment, Competent, and Character. Whether you fit as an applicator or contractor, these same rules would apply.
COMMITMENT
Commitment is having the complete, proper equipment as well as manpower to perform the work. Not only does this include the spray equipment, but any auxiliary equipment required, including PROPER Safety equipment and use, along with follow-up inspection equipment.
Many may be wanting to transition spray foam for polyurea spray, and that is great! A side piece of history here as the polyurea spray technology was originally developed and designed as a superior protective coating system for application over rigid spray foam. There have been some very false claims that the technology was developed for bedliner application or edge-coating for OSB or other pressed board applications, and that is not true. Those applications came later.
Your current spray foam equipment may in fact properly process most fast set polyurea systems. The main component characteristics are:
- Ability to develop high pressure, typically about 2000 psi (~140 bar);
- Develop high, consistent flow rate (proportioning unit needs to be able to deliver more material to the spray gun than the spray gun setup is designed to handle);
- Develop High Heat, lowers the mix viscosity and allows for proper spray atomization (typically 150 – 160° F / 65 – 70° C). Ensure that the heating capability of the unit is designed for the delta-T (change in temperature) at the flow rate you will be applying the material.
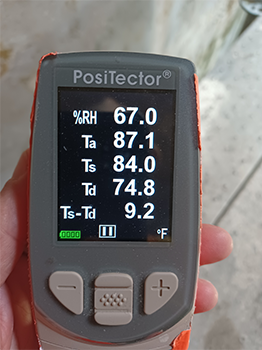
Performing and understanding Environmental Condition Assessment on the job site.
One important piece of the material flow area, and often overlooked, are the material supply pumps. These need to be able to provide more flow to the proportioning unit, than that unit is supplying to the spray gun. This becomes especially true and problematic when working in colder environments, due to increased viscosity (reduced flow) of the system liquid components.
Unlike spray foam systems, for polyurea workings the ISO side is typically higher than the Resin component side. Consequently, one may in fact note a higher processing pressure on the ISO side as compared to the Resin side. This is perfectly normal, if the pressures are consistent, and stable during application.
Best advice, check with the polyurea system supplier to make sure your equipment is suitable for proper application of their system. I can make many things come out of the spray gun and “spray,” but I want to ensure that the proper mix is occurring, not just spraying.
COMPETENT
Competent means having the proper information, training, and skills to successfully perform the desired work. So social media is great, but very disturbing at times for me. On various Facebook groups, Iconstantly see post that ask: “I am getting E24 code, what do I need to do?” or, “My ISO pressure is higher than my Resin pressure, I checked my y-strainer and it is clean. What could be wrong?” or, “What size drill bit do I need for a certain mix chamber?” All of this information, or answers to the questions, are part of official training on the equipment and material, or even found in the equipment manuals or product Tech Data Sheets. The time it took to access Facebook, post the question, then wait for a response (of which there will be various), one could have easily and quickly found it in the related documentation.
Whatever your experience level is, one should continue their education and attend a variety of training courses available to our industry. In most polyurea work where there is a specification present (and that is a very important document), it will note the requirement that the applicator/contractor possess a valid certification or qualification to perform the application work. This could be an official training from a 3rd party institution such as PDA: Polyurea Development Association or AMPP: Association for Materials Protection and Performance (formerly the merged SSPC / NACE group) to note a few.
Training is not just on the “spraying” part, but will include safety, as well as substrate identification, preparation, and repair work. Communicate with your supplier.
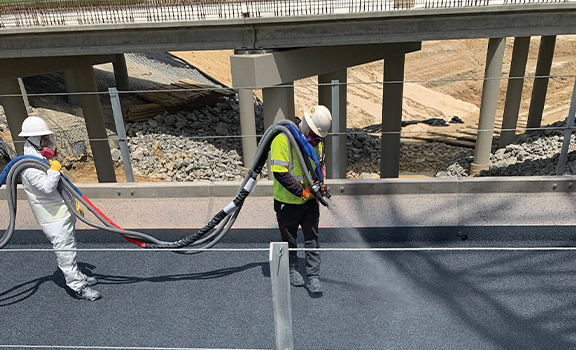
Installing a Duplex Polyurea System requires properly trained applicators.
CHARACTER
Probably the most important is Character, which also ties in with Commitment and Competence. Don’t take short-cuts, ignore proper safety protocols, or get in a hurry, it will cost you later. Use the proper material for the application project. Just because you have some “polyurea” left over from another project, does not mean that system is suitable for the next application project.
One of the keys to a successful installation is being prepared and ready for that installation, plan ahead and be organized. Don’t wait till the last minute and try and secure material, or price shop. Use the type of material designed for the project.
To have a top-notch, quality organization, there are a few quality and record keeping issues that should be used when applying these coating systems. To protect your interests as the applicator, the application and the integrity of the coating system, records of the application, material used, and inspection of the work shall be noted. By having and implementing a Quality Control Program, you can ensure application to application consistency and performance.
By following these simple steps, one can become a successful applicator or contractor with polyurea based coating and lining systems. The spray polyurea elastomer technology requires the contractor to pay closer attention to detail than other materials. For proper application of polyurea spray elastomer coating and lining systems, it’s not just having the spray equipment that makes one an applicator. It’s that plus all the accessory materials, training, organization, and record keeping that go along.
For use by SprayFoamMagazine.com & Spray Foam Magazine