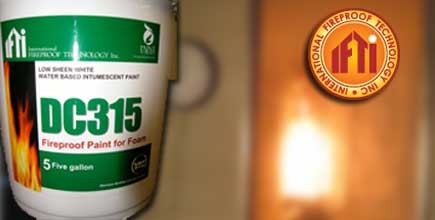
Fire Protective Coatings Provide Quality Assurance To the Spray Polyurethane Foam Industry
IRVINE, CA – May 14, 2014 – When fire protective coatings are used as ignition barriers (in certain attics and crawlspaces) over spray polyurethane foam (SPF), the risk of fire to occupants and structures is minimal. Various building codes recognize this by allowing the omission of a thermal barrier in these circumstances. The Acceptance Criteria for Spray-Applied Foam Plastic Insulation (Appendix X of AC377) provides a methodology for alternative materials in lieu of using building code prescribed ignition barrier protection. The trends within the SPF industry are focused more towards foams that can pass Appendix X testing, without being covered at all.
However, as SPF's have become more flame retardant and fire protective coatings have become more capable, coated SPF assemblies are passing the significantly more rigorous 15-minute NFPA 286 room corner test. Therefore, coated SPF assemblies are meeting the requirements of the International Building Code for interior wall or ceiling finish material [per 2012 IBC Section 802.1.2 and per 2012 IBC Section 2603.10 special approvals, other room corner tests may qualify these assemblies as well]. Coated SPF assemblies are now being approved and installed without the fire protection provided by 1/2-inch gypsum wallboard, the traditional code-prescribed thermal barrier.
The use of SPF in occupied spaces offers a significantly greater risk to occupants and property, than the use of SPF in entry-limited attics and crawlspaces. Hence building codes require SPF to "be separated from the interior of a building by an approved thermal barrier of 1/2-inch gypsum wallboard…" [2012 IBC, Sect. 2603.4]. Gypsum wallboard is qualified under Chapter 25 of the IBC and alternative thermal barrier materials may be qualified using NFPA 275 [2012 IBC, Sect. 2603.4].
The "special approval" section of building codes [for example: 2012 IBC, Sect. 2603.10] may be used to qualify the use of SPF assemblies without a thermal barrier; these are termed "alternate assemblies." Fire protective coatings and SPF are being qualified as "alternative assemblies." (That is, no prescriptive thermal barrier is being used). Evaluation reports list these alternative assemblies based on individual fire test results and "agreements" between material manufacturers. ICC Evaluation Service, for example, provides for fire protective coatings to be incorporated into spray foam evaluation reports as "proprietary components." This, in essence, requires that the evaluation report holder (that is, the SPF manufacturer) to assure that the fire protective coating system being sold on the market is as fire tested over that particular SPF listing in the report. Neither the building codes nor acceptance criteria require third-party quality assurance of fire protective coatings used in alternate assemblies, leaving a gaping hole in the fire risk reduction efforts of the SPF industry.
Many AHJs (Authorities Having Jurisdiction or building officials) are left confused by the lack of product information: SPFs are required to "bear the label of an approved agency … sufficient to determine that the end use will comply with code requirements [2012 IBC, Sect. 2603.2] but fire protective coatings do not. This confusion can cause extra work, cost and delays for builders and SPF contractors alike.
As of today, International Fireproof Technology, Inc.'s DC315 fire protective coating is the ONLY alternative assembly coating listed in ICC-ES Evaluation Reports that is marked and listed under a third-party quality assurance program. One proposal to rectify this situation in the future would be to require the "inspection and marking" of fire protective coatings used in SPF assemblies. Specifically, a program of this nature could be developed through ICC Evaluation Service.
In the meantime, one way to maintain the integrity of using coatings over SPF, assist with AHJs, customers, and architects is to use DC315; a coating that meets tomorrows needs today and plugs this gaping hole. Using a coating that meets these requirements assist with:
- Faster Approvals (AHJs are efficiently able to complete front and backside approval of your jobs.)
- Easier Insurance Approvals
- Less Liability (via proof the coating being used is the coating that was tested).
- Close More Bids (clients are assured they are getting what they paid for and avoid issues with inspections in the future).
Characteristics and Advantages of DC315:
- DC315 is a one part water based acrylic latex paint simply stir and spray
- DC315 has passed over 112 separate NFPA 286 room corner for alternative thermal barrier and ignition barrier test using over 29 of the largest foam manufacturers in the SPF industry.
- DC315 is 3rd party certified as a one coat application when applied up to 24 Mils WFT, proving to be a true onecoat application (includes ceilings).
- DC315 is the most used, trusted and approved product in the U.S.A.
Remember the PROOF IS IN THE TESTING, and now you can PROVE THE COATING BEING APPLIED IS WHAT WAS TESTED!!!
About International Fireproof Technology, Inc.: IFTI manufactures state-of-the-art intumescent fire retardants and thermal barrier coatings. Designed and tested for the global market, IFTI's products are widely used in hospitals, restaurants, nursing facilities, commercial buildings, and residential homes. IFTI's products, including DC315, fall under the Paint to Protect brand, and have been developed to provide superior cost-effective fire protection over spray polyurethane foam. for more information, please use the contact details and links provided below.