
Filling the Space Beneath
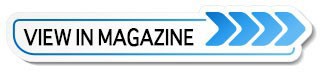
SPRAY FOAM MAGAZINE – Show Issue 2021 – Concrete can react to environmental conditions, like the weather, and therefore the permanency and duration of the material can be affected. What are these effects, and what solutions can SPF concrete lifting contractors provide?
New trip hazards, cracks, voids, gaps, and improper pitch of concrete can occur at any time with the most frequent causes being water/drainage, frost heave in cold climates, and poor compaction during initial installation. Beyond an unsightly appearance, the implications are lawsuits with nonconformance to the American Disabilities Act standards and extensive damage beyond the slab to a structure if water drainage is impacted.
Property owners, property managers, and contractors should occasionally check the pitch of the concrete around the property to make sure that it is sloped away from the foundation. If the concrete is pitched towards the foundation, there are two options to correct it. The concrete can either be replaced, which can be expensive, time-consuming, and disruptive or, by lifting the concrete. This method is normally half the cost of replacement and highly profitable for the service provider.
If the concrete is left as it is, it can lead to further damage and safety issues with the foundation itself. Cracking can also worsen, and if cracked beyond repair, it may not be able to be lifted. In short, time is of the essence.
Unfortunately, there is very little if anything that can be done to correct this issue during the winter months. In very cold weather there may be significant temperature differences between the concrete core and its exposed surfaces which may also lead to thermal cracking. That is why it is important to identify concrete problems in the spring, summer and fall before they get worse. If there are other related weather issues such as ocean tide, and seawall concerns, concrete lifting contractors have materials and processes to address this repair.
When the snow melts, companies like Foamjection, with certified concrete lifting contractors, are busy scheduling estimates to ensure work can be scheduled through the summer and fall.
Most concrete raising jobs will take approximately two hours, start to finish, and the concrete will be ready for use immediately. First ⅝” injection holes (size of a dime) are strategically drilled around the sunken concrete areas which require lifting. Once everything is prepped and the hose and materials are in place, the polyurethane foam is injected through the holes which fills the space underneath the concrete slab, using the concrete slab itself to drive the foam into the crevices, thereby lifting the concrete back to its original, correct level.
Upon completion of leveling the concrete, the injection hole(s) are filled discreetly with new cement, making them nearly invisible and allowing you to use your surface immediately. It’s as simple as drill, pump and patch.
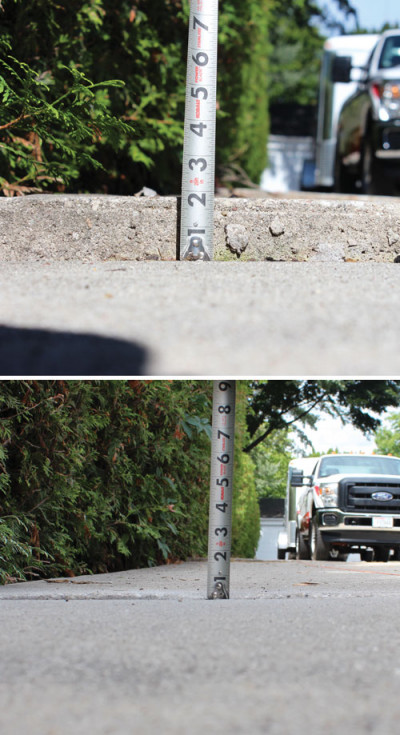
Top: before concrete lifting process; Bottom: after
Certified contractors are using the equipment normally associated with spray foam applications. The difference is the actual material (specially formulated polyurethane) and the gun. A switch over of equipment is fast and easy to add diversity to a spray foam business. With additional training and investment, spray foam contractors can add concrete lifting to their list of services.
Foamjection contractors use HMI polyurethane foams which consist of 39-49% renewable and recycled materials. This polyurethane material is permanent and weighs roughly two pounds per cubic foot, compared to traditional mudjacking material which weighs on average 100 lbs. per cubic foot.
The concrete raising equipment is contained in a truck, van, or trailer and has a sufficient length of hose to accommodate most locations without disrupting any landscaping. Versus heavy, destructive equipment needed to rip out concrete and repour. The system is comparable to spray foam industry standards with the major difference being the foam and the gun.
Stating that something is permanent is not possible as the subsoils below the concrete may move over time. Heavy rains, drought, inappropriate water management, and recurrent frost can all lead to an additional settlement. Systems like ‘deep-injection’ can also offer a potential solution to this issue by stabilizing the soils by grouting polyurethane into the soil concerns below the concrete before the concrete is even lifted.
Temperature variations, particularly cold weather and water to cement ratio can cause the concrete to contract and in turn lead to cracking, sinking and spalling. If there are frequent freeze and thaw cycles combined with water, this can have damaging effects on concrete.
Science and product development have come a long way in recent years but unfortunately those attributes cannot control the weather. What certified SPF concrete lifting contractors can do is offer their clients a cost-effective solution to many of the main issues caused by weather beaten concrete, in addition to saving their client’s money. That fact alone will bring out the sunshine on an otherwise cloudy day and level up the playing field with mother nature.