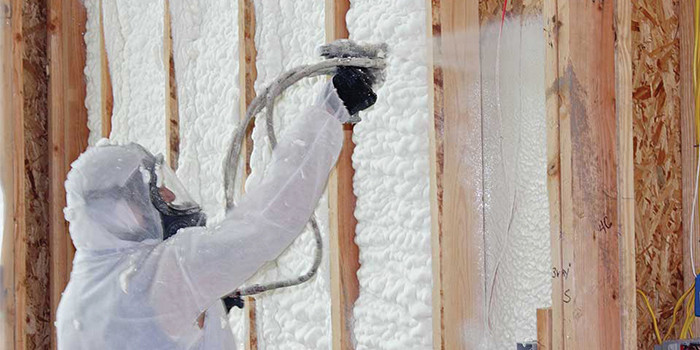
Efficiency Techniques
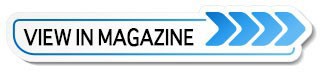
Spray Foam Magazine – Summer Issue 2022 – What is efficiency? This term gets used a lot, especially when it comes to the subject of increasing your bottom line, but what does it really mean as a spray foam contractor and why does it matter? A lot of talk around efficiency in our industry centers on the energy savings that spray foam provides to the consumer, but for contractor’s, efficiency is the ability to deliver their services in a cost-effective way while maintaining quality.
Focusing on efficiency can not only increase your bottom line, but also drive down the overall cost of spray foam for consumers. Spray foam currently accounts for only 20% of the overall insulation industry, meaning there is a lot of market to grow into. Continuously becoming more price competitive with other types of insulation aids in this growth, ultimately providing more business and opportunity for spray foam contractors.
Opportunities to improve efficiency need to be looked at before, during, and after spraying at the jobsite.
Before any product has been sprayed you can improve efficiency by streamlining processes starting with training, estimating, and pre-conditioning. These steps are arguably the most overlooked areas when it comes to improving overall efficiency. Ongoing training is important to keeping both sprayers and administrative staff current on techniques, technologies, learning, software, and processes. Choosing the right product can also impact your performance and profitability for a job. Contractors should seek out manufacturers and business partners that are focused on providing products that align with improving efficiency and provide features that drive this improvement such as improving yields.
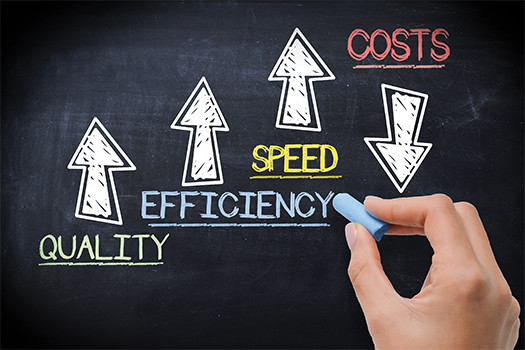
Another pre-jobsite area that is often overlooked is the pre-conditioning and preparation of material. Preparing before arrival to a jobsite increases trigger time. Preparing can include pre-heating the material, implementing temperature control on the rig, and utilizing barrel blankets or blazers.
There are many processes that take place on a jobsite, and they all offer opportunities for greater efficiency. Some areas of focus include setup time, trigger time, stroke count, density checks, yield measurements, and tracking waste. All of these data points should be recorded to discover areas for future refinement.
Post analysis should reveal processes where efficiency can be improved. For example, maximizing trigger time/stroke count by ensuring an open and clear work space, improving spray technique to minimize waste, and product yield ensuring you’re getting the maximum out of the material.
When talking about waste we don’t just mean spray foam, we also refer to commonly used items on jobsites. Waste can include anything from the foam itself to tape and staples, but the largest spends should be paid attention to the most. For example, watch the foam closely monitoring the amount of waste caused by overspray, poor technique, or from overfilling the cavity.
Other areas that are often overlooked that provide valuable data and can drive efficiency include rig staging and loading time, transit time, vehicle tracking and telemetry, production time, and material usage. After a job is complete it is important to not miss opportunities to refine processes. The easiest way to refine is by having the data points available to analyze. The areas previously mentioned should be recorded daily, preferably digitally so that information sharing is easy and consistent across your team/organization.
In addition to debriefing jobsite data, it is imperative to be consistent with preventative maintenance on all equipment. A weekly, monthly, quarterly, and annual plan should be developed, implemented, and tracked. Staying up-to-date with all maintenance ensures less downtime due to equipment issues.
It may seem overwhelming to discover all the ways you can improve efficiency for your operation, but you don’t need to track and fix everything all at once. Even small adjustments over time can add up to a positive impact to your bottom line.
Direct any questions you have about statements made in this article to SWD:
800-828-1394 // marketing@swdurethane.com
*Spray Foam Magazine does not take editorial positions on promotional or sponsored; individual contributions to the magazine express the opinions of discrete authors unless explicitly labeled or otherwise stated. The inclusion of a particular piece in the magazine does not mean that individual staff members or editors concur with the editorial positions represented therein.