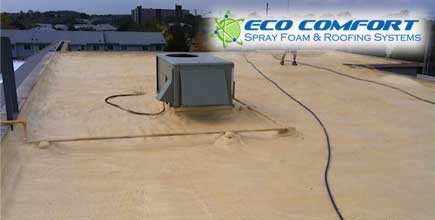
Damaged Roof of Fitness Center Gets Restored With Closed-Cell Spray Polyurethane Foam
LONDON, ON - June 12, 2013 - It's hard to get a good workout in with water leaking on you. This was a predicament the owners of an Ontario fitness center faced as their old roof system had deteriorated to the point where fractures caused by pooled water had been formed, which gave way to severe leaking and, consequently, a loss of some gym's customers. Finally, Eco Comfort Spray Foam (ECSF), a spray polyurethane foam insulation and roof system contractor, came to the rescue by taking on a project to restore the gymnasium's roof to provide a proper exercising milieu.
Prior to the involvement of ECSF, the owner had been fixing the building intermittently, almost on a weekly basis before finding out how to obtain a more resilient and longer lasting roof. ECSF's Leeann Sigurdson explained that SPF roof systems in southern Ontario, in contrast to most US states, have recently began to grow in demand as building owners and contractors become more educated on their benefits.
"It's up and coming," said Sigurdson. "Around here, old tar roofs are still being used and they generate pooling and leaking. Some literally don't have any insulation protection, so all the hot air and cold air is just going straight through the roof. With a spray foam roof, they can avoid all that and wind up paying the same price."
The project consisted of removing the existing stone aggregate system from the tar roof and applying a new system of spray polyurethane foam to the tar substrate.
According to Sigurdson, the main problem came from the roof's solar panels, which generated heat for the building's boiler system that powers the fitness center from the spa to the pools.
"The panels had been there since the 1980's," said Sigurdson. "When the crew got up there, they noticed most of the leaking came through the solar panels' pipe penetrations that ran into the building."
The team used a man-lift to get all materials up to the roof. After the gravel was removed and dumped off site, the ECSF team inspected the tar roof surface, the flashings, and the vents for any structural damage, they tested the roof for moisture retention, which was greater than 10%. Sigurdson explained that because the roof more than 10% in moisture retention, a gas-powered blower had to be used to dry the roof, letting moisture escape and making the roof surface clean.
Sigurdson said that the biggest challenge the ECSF team dealer with was working around the solar panels.
"They were very tight and it was hard working around those boilers without disturbing or breaking anything." said Sigurdson "Cleaning the aggregate from underneath the boiler was pretty much the most challenging part of the job; we had to be extra careful with them"
For overspray protection, the crew used a wind screen, which resembled an oversized hockey net with rollers on the bottom. The screen would go over the spray gun and the crew would push in concordance to the spray line so that overspray was caught in the net. Since the project took place during daylight hours, a plastic barrier was put in place along the roofline for extra safety, which kept the overspray on the roof and not damaging the cars parked below in the lot in front of the building. The crew wore fresh air respirators and jumpsuits during the application.
The ECSF team had one rig on site equipped with a Graco Gusmer H-20/35 proportioner. They applied between two to three inches of FE 348, a 3 lb. closed-cell foam made by BASF, to the flat roof, parapet walls and HVAC units using a Graco GX-7 spray gun. The spray area encompassed 9,300 sq. ft. The variation of SPF thickness fluctuated to even out low spots where water collected so as to eliminate those spots. The foam was tapered down for maximum water drainage.
After the SPF was applied, the crew installed 20 mils of white Safe-T-Plex 520, an acrylic elastomeric roof coating, on the flat roof. Sigurdson said that the coating provides a 10-year warranty that virtually turns into a lifetime warranty if proper maintenance is provided to the roof.
"The warranty stipulates that recoating has to be done at 10 years, otherwise it's broken down," said Sigurdson. "Upon recoating, the roof owners get another 10 years after that and so on. It's a low maintenance cost for a big building owner."
The 15-man crew was able to complete the job from the removal of the aggregate system to the coating application in one week. The project progressed as daily operations of the gym carried on normally; the crew worked in the midst of heavy foot traffic and a busy parking lot without incident.
Sigurdson noted that the client followed up with ECSF and provided positive feedback about the project.
"After the job was done, they contacted us and said that there was no leaking and that the operation cost of the building has gone down, which made them real happy" said Sigurdson.
Sigurdson pointed out that because of the leaks, the fitness center had lost some of its customers and that they are now moving forward with their clientele once again.
"There are no more buckets inside the building anymore," said Sigurdson. "People can exercise normally."
Sigurdson said that what sets this roof apart from any other system the client could have used is that it is seamless, and it is only by way of SPF application that a seamless roof is attained.
"The tar system they were using will break down over time, the spray foam doesn't," said Sigurdson. "Nothing is able to escape through it."
Sigurdson also added that SPF roof systems not only give out customer satisfaction by bolstering
their roofs, it also provides better insulation inside the building, which saves the customer so much money in energy bills that, over time, it pays for the roof back.
About Eco Comfort Spray Foam Insulation and Roof Systems: With well over a decade of experience in the industry, Eco Comfort has firmly established itself as an industry leader and Niagara Region’s premier spray foam company. Servicing Niagara, GTA, Hamilton and all surrounding areas, Eco Comfort is setting the high water mark with their hands on approach and commitment to customer satisfaction driven by their no nonsense satisfaction guarantee.
In addition to the necessary industry accreditation and a long list of customer referrals, Eco Comfort has been recognized by industry trade magazines, industry related web sites and regional newspapers alike.
Eco Comfort is proud to be the first company in the Niagara Region & GTA to offer 3 lb. spray foam roofing systems, backed up with a non prorated 10 year warranty.