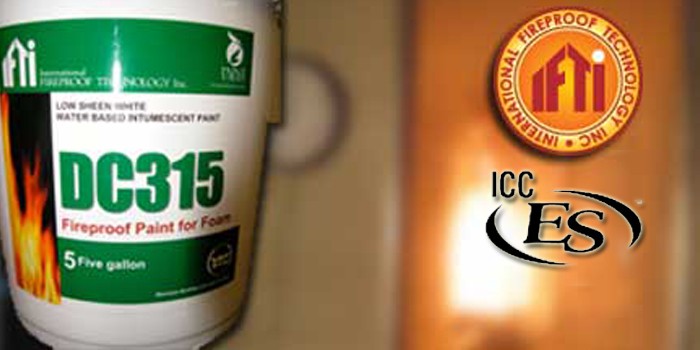
Code Compliance: The Next Step
IRVINE, CA – April 26, 2016 – When applying a thermal or an ignition barrier intumescent coating over spray polyurethane foam, the applicator directly assumes the responsibility of fire protecting the structure onto which that coating is applied. In other words, he has made sure that the product he applies has been properly tested to ensure the safety of the building occupants. In a perfect world, this is true… but how can he be sure that the product he is applying is code-compliant? To this day, there are many SPF contractors and code officials that have been misinformed about the proper way to go about installing ignition and thermal barrier coatings, and this has given way to dire repercussions derived from unethical practices, giving intumescent coatings a bad rap. The reason? There haven’t been any quality assurance requirements for intumescent coatings over spray polyurethane foam – until now.
Gary Wolfe, Executive Vice President of International Fireproof Technologies, Inc. (IFTI), has been a long-standing advocate for implementing criteria for intumescent coatings over foam that stipulates quality assurance of the coating that is utilized over SPF insulation by third-party testing validation. His efforts have since paid off. While working with the International Code Council-Evaluation Services (ICC-ES) to ensure that the testing criteria for both the SPF and coatings is one in the same, a new ICC-ES Acceptance Criteria – the AC456 – came into fruition.
Wolfe’s mantra has long been “the proof is in the testing,” a theme that he puts into practice daily when enlightening industry members about his company’s staple intumescent coating product, DC315 – which has now received the ESR# 3702 ICC-ES evaluation report for compliance with the new AC456 standard and International Building Code (IBC) and International Residential Code (IRC) codes. SprayFoam.com recently caught up with Wolfe, who is nothing short of jubilant that DC315 has met the criteria for this compliance report.
RELATED IFTI Reveals How Firestop Systems Can Compliment Spray Polyurethane Foam Businesses , ICC-ES ESR# 3702 Verifies that IFTI's DC315 Meets Code Requirements, IFTI Goes Above and Beyond Building Code Requirements
SprayFoam.com: AC456 is a big step for intumescent coatings. Could you elaborate on what it entails?
Gary Wolfe: AC456 establishes criteria for Coatings over SPF ensuring that the product tested is the same product that is used on the jobsite. This is being added to AC377, the Acceptance Criteria that establishes the fire protection for spray-applied polyurethane foam plastic insulation to ensure that it is tested as an assembly with a compliant coating. In other words, A= Foam + B= Coating = C Assembly.
SF.com: When will AC456 go into effect?
GW: Well, October 2017 is when it will be officially codified, and as of that date, all testing that has not been performed in accordance with AC85 Section 3.1 will be removed from all SPF evaluation reports. However, we feel that as word gets out about AC456, more and more code officials will get on the ball effective immediately. It’s like if I told you that you are required to wear a life jacket on your private boat as of October of next year, would you take a chance on drowning or wearing one? Since AC456 fills a gaping hole in industry safety, folks in the industry will want to get onboard as soon as possible. IFTI recently had all of its testing since 2008 audited at Intertek and QAL, and all were found to meet the new AC456 criteria.
SF.com: What does it mean for IFTI’s DC315 to receive the ICC-ES Evaluation Report?
GW: It means that DC315 fire protective coating meets the requirements and intent of AC456. When used and tested as a component of an assembly with specific spray polyurethane foam (SPF) systems, that assembly does not require the thermal barrier specified in IBC Section 2603.2, IRC Section R326.4 or AC377 Section 3.2.3.2. With this report, building officials, architects, contractors, specifiers, and designers can provide a basis for using or approving DC315 in construction projects under the IBC and IRC codes.
SF.com: Given this, how can a contractor or code official make sure they are complying with codes pertaining to thermal or ignition barrier coatings over SPF?
GW: Excellent question. IFTI feels that the best way to do that is to insist that the coatings manufacturer supplies them with an evaluation report on their intumescent coating product itself, as well as a report with test validation of the coating and specific brand and type of foam being tested as an assembly using the 15-minute, NFPA 286 full-scale room corner test or equivalent. Having a full-scale assembly test plus an evaluation report is bulletproof for a contractor, code official, or fire marshal in terms of code compliance.
SF.com: Why is there a lack of understanding in the SPF industry about code compliance?
GW: I think there’s a great deal of misinformation going around about what the code allows such as ignition barrier tests being used as a thermal barrier test or if a certain SPF passes one test then it is assumed any other foam could probably pass the same test. Without a coating company evaluation report and third party auditing, as well as sampling and manufacturing that is accountable to a quality assurance manual and program, how would a contractor know? This creates confusion and lack of trust where there shouldn’t be. The code doesn’t have wiggle room - which was a big reason for our big push for AC456 – it is a more consistent message for the intumescent coating and spray foam industries. Now, there will be a requirement to meet the criteria of AC456. But just like our motto says, “the proof is in the testing” coating manufacturers should have test reports to back up their product 100 percent of the time.
SF.com: Sounds like IFTI has gone through great lengths to educate others about code compliance and promote DC315 as the product that sets the standard in code compliance.
GW: Yes, we feel that the more tests we have to back our product, the more worldwide acceptance it generates. Therefore, we have conducted over 200 fire tests (over SPF) worldwide. We believe that we cover the majority, if not all of the major foam companies in the United States, Canada, and abroad. In actuality, all the testing that we have done in the last nine years complied with AC456 before we received the ICC-ES Evaluation Report. Additionally, we have over 100, third-party tests for performance and use of DC315 outside of NFPA 286 that involve properties such as health, longevity, humidity, impact, toxicity, hazard, and much more. We go beyond testing for fire protection; we further test DC315 for the protection of the end user. Furthermore, our Certified Applicator Program (CAP) has generated over 1,100 certified applicators. We have manufacturers and distributors that ask their whole staff to go through the program; there’s letters going around to spray foam contractors from manufacturers and distributors asking them to take the course; code officials have an expectation in the marketplace to have this certification or an application course similar to it. One of our ultimate goals is to set up coating applicators for success and the CAP program does just that. Simply stated, we believe passing an assembly test is a starting point of responsibility, not the ending point.
SF.com: We understand that you are in the process of receiving an evaluation report from the Canadian Construction Materials Centre (CCMC). What does this do for DC315?
GW: To obtain a CCMC report, we first had to create the Technical Guide, which spells out the testing protocol and criteria a coating must meet, and then we had to perform the testing that exceeds the U.S.’s testing standards within this guide. We wrote the Technical Guide but did not make it easy – the fire test is both longer and hotter, and DC315 provided equivalent protection as half-inch gypsum board. It legitimizes, and most importantly, takes liability away from contractors in Canada and throughout the world who want to use DC315 over foam. Having this document in Canada and the ESR #3702 compliant to AC456 does not eliminate liability altogether, but it mitigates it to a point where we (the manufacturers) and our customers worldwide are as compliant as we can possibly be.
About International Fireproof Technology, Inc.: IFTI manufactures state-of-the-art intumescent fire retardants and thermal barrier coatings. Designed and tested for the global market, IFTI's products are widely used in hospitals, restaurants, nursing facilities, commercial buildings, and residential homes. IFTI's products, including DC315, fall under the Paint to Protect brand, and have been developed to provide superior cost-effective fire protection over spray polyurethane foam. For more information, please use the contact details and links provided below. - See more at: www.painttoprotect.com