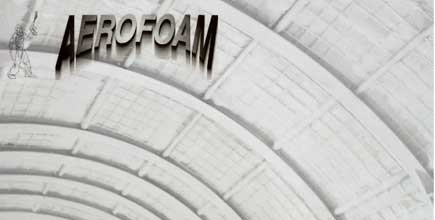
Closed-Cell SPF Utilized to Insulate Additions in Colorado Silver Mine
OURAY, CO – October 11, 2013 – At 14,000 feet in the Colorado mountains, any season can be cold. Yet it was during the winter when the owners of Revenue-Virginius Silver Mine, which nestles atop Mount Sneffels, decided to reopen for business. The reopening involved renovations such as an above-ground propane storage room, as well an underground area that will be used as a workshop where workers can weld and service heavy machinery. Because the owner wanted their workers and equipment to operate in an ideal climate, they opted to insulate these additions with spray polyurethane foam.
The owners brought in AeroFoam Insulation for the SPF application, they were based in Delta, Colorado, a two-hour drive from the mine. AeroFoam's Justin Reed said that the job proved challenging from the beginning.
"To reach the mine site, we would leave our house at 4 a.m. and begin our drive up to the mountains," said Reed. "We had to chain up all our truck and trailer tires to get enough traction to be able to pull ourselves up the ice-covered mountain road."
The AeroFoam crew was not allowed to leave their rig at the mine site, so the icy trip became a part of every working day.
During their time at the mine, the three AeroFoam crewmembers were required to attend weekly OSHA safety meetings in order to be in compliance with safety regulations and to be prepared for the harsh and overwhelming conditions of working in a mine. The crew was instructed about the hazards involved while being underground including the lack of oxygen, claustrophobia, and sudden roof cave-ins. The meetings also stipulated what workers were required to be outfitted with at all times. Aside from regular PPE, which included insulated coveralls and fresh air respirators, the crew had to wear Tyvek a suits over the coveralls, steel-toe boots, goggles, and hard hats to be OSHA compliant. While the AeroFoam crew worked, the construction at the mine was still underway and it included the blasting-out of caverns underground.
"Before they would blast, the mine workers would come warn our crew ahead of time so we could vacate the caverns to the proper safety location," said Reed. "Mine sites can be a very dangerous place and it's best to think of safety constantly, or someone can get injured."
AeroFoam's job consisted of the application of SPF to the exterior walls and the roof of both additions. Both areas had to be sprayed simultaneously and intermittently, depending on the stage of the mine's construction and the areas that were being worked on any given day.If the mine workers were working below ground, the AeroFoam crew would apply SPF to the propane room, and if the mine was being worked on above ground or on areas away from the underground shop, the crew would proceed with the underground application. The goal of the SPF application was to render the propane room and the underground shop area with optimal R-value, which will yield to better working conditions once the mine is ready for full-fledged operations.
For prep work, the crew taped every area on the exterior walls of the storage room that will have windows and doors installed. The propane tanks, which had already been installed before the AeroFoam crew arrived onsite, as well as tools inside the above ground room, were covered with plastic for overspray protection. For the underground SPF application, the crew had their fresh air respirators attached to cables that hooked on to an air compressor that pumped fresh oxygen. The crew operated several BTU heaters and a small diesel fuel heater during the applications, which were used to heat up the materials, keep the equipment warm, and warm up the substrates so that SPF could properly adhere to them.
The crew used Foam-LOK 2000, a 2 lb. closed-cell spray polyurethane foam made by Lapolla, throughout the SPF project. Using a Graco Fusion air-purge spray gun, the crew applied five inches of foam to the underside of the roof and the exterior walls of the propane tank room. Then, they applied nearly six inches of foam to the envelope of the 400-feet deep cavern area where the service shop will be. A total of 21 sets of foam were installed during the project, providing the two areas with an R-7 value per inch. After the SPF was installed, the crew applied 24 mils of DC315, an thermal barrier coating made by IFTI, to protect the foam in both areas.
Aside from the heaters, AeroFoam's rig was equipped with a Boss Proportioner 5/12 K machine made by SFE. It took the three-man AeroFoam crew a month and a half to complete the job.
Reed claims that his client was very pleased with the results, noting that not only have the mine workers been able to resume construction in a warmer climate underground, but that the SPF application made the underground area brighter.
"They were surprised at how much light the SPF and the coating added to the underground area," said Reed. "The yellow foam and the white coating turned those black walls into light walls, and all of a sudden there's this big change down there."
Even though Reed and his crew were glad to see the coming of spring after a long winter in Mount Sheffels, he said that it was rewarding to have taken part in such a unique project.
"Not many mines can claim to have their own workshop underground to be able to weld heavy machinery," said Reed. "Usually, they would have to be out in the snow or in a not-so-warm environment. SPF can create comfort in the harshest of environments."
About AeroFoam Insulation: AeroFoam Insulation proudly serves the Delta, Colorado, and surrounding areas with closed-cell SPF applications ranging from new residential and commercial buildings. They also specialize in spray foam roofing. For more information about AeroFoam Insulation, please use the contact information and links provided below.