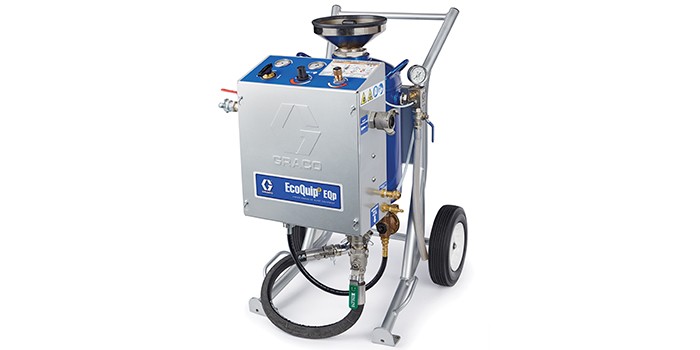
Cleaning Nasty Polyurethane Stains & Spills
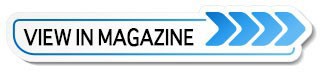
MINNEAPOLIS, MN– June, 2018 – As a field representative for a manufacturer of pressurized surface cleaning equipment, I often encounter challenging cleanup situations. One of the more stubborn materials is polyurethane foam, which has gained wide acceptance as an insulation and concrete-repair solution. The high-density foam expands to fill voids and lift sunken concrete, but can be particularly challenging to remove when spilled onto unintended areas.
Historically, the default choice for large-scale concrete and steel surface restoration has been sandblasting or other dry blasting techniques. Dry blasting has been an effective but dusty approach, with emissions of silica and other abrasive or substrate particles linked to negative health and environmental impacts. Wet blasting was developed to minimize fugitive dust, but was slow to catch on due to heavy water use and the problem of containing and disposing of contaminated water.
To address these challenges, a growing number of contractors and owners are turning to Vapor abrasive blasting, which uses just enough water to suppress dust and still achieve desired production rates. Vapor abrasive blasting systems combine water and abrasive media in a pot under pressure, then inject the mixture into an airstream, providing a precisely controlled system to treat stains resistant to other measures. Because the water is pressurized instead of air, as with wet or dry blasting systems, the operator can set the blast pressure to approximately 40 psi and remove stains without damaging the concrete substrate. Vapor abrasive blasting also uses little water, which avoids slurry messes that accompany wet blasting operations.
Using Graco’s EcoQuip 2 Vapor Abrasive® blasting equipment, I’ve found a highly effective solution to handling polyurethane foam spills. The EcoQuip 2 vapor blasting units suppress dust up to 92 percent when compared to dry blasting. The EQp uses approximately eight gallons of water per hour, far less than traditional wet blasting.
BEFORE
The Graco EcoQuip 2 EQp uses a water-abrasive mixture to restore concrete surfaces, seen here in a before and after example
AFTER
Health, Safety and Environmental Advantages
Health and environmental factors have been key drivers in the development of wet and vapor blasting systems. Several European nations banned sandblasting in the 1950s and 60s due to concerns over silicosis. While the US has not totally banned sandblasting, the US Occupational Safety and Health Administration (OSHA) established a Silica Rule in 2016, decreasing the permissible exposure limit to respirable crystalline silica.
Wet blasting has also been subject to environmental regulatory limitations. According to the United States Environmental Protection Agency (EPA), the Federal Water Pollution Control Act placed strict limits on discharge of pollutants into navigable waters. States and cities have scrutinized the amount of fugitive water in storm water systems.
Vapor abrasive blasting addresses these issues. The vapor abrasive approach encapsulates individual grains of abrasive material in water, weighing the particles down and providing more mass on the particle at impact. Because dust is minimized, less containment is generally required and media clean-up time can be reduced. Vapor abrasive blasting also reduces rebound of abrasive particles, which pose risk to workers and the environment.
On a recent demonstration project, polyurethane foam had leaked onto a concrete pad at SprayPolyParts,
a distributor of spray foam equipment and products. Using a Graco EcoQuip 2 EQp (Figure 1), we removed the stains in less than an hour with vapor blasting (Figure 2). The abrasive media residual required no special cleanup, as crushed glass is a non-toxic material.
Beyond Cleaning Polyurethane Stains
Vapor abrasive blasting can address a variety of removal and restoration situations. A wide range of pressures and abrasive media can be used, providing flexibility for numerous applications, and the adjustable settings also improve efficiency. Traditional wet blasting equipment is typically on or off, which can decrease production and over-use water and media.
Although thorough cleaning and minimal dust generation make vapor abrasive blasting a natural fit for cleaning up polyurethane foam spills, the vapor abrasive blasting equipment has many other beneficial uses. The environmental and efficiency gains make it an attractive option to public and private agencies facing a wide variety of tough cleanup tasks.