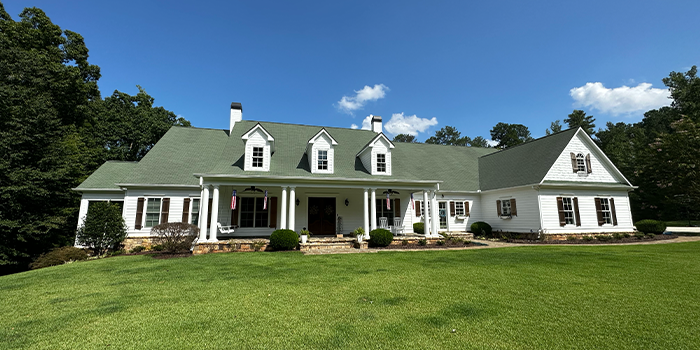
Build It Tight
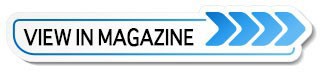
SPRAY FOAM MAGAZINE – The Blower Door Test, often referred to as a pressure test, defines the air tightness of the building and helps detect any air leakage in the building’s envelope. This test has been around for decades but why has it become predominant in recent times? Could it be that builders and architects are increasingly aware of the importance of the airtightness of a building and the need to determine the “weak points” of a building to ensure performance? Building performance specialist, and owner of Elm Energy Group, Jamie Kaye, proudly calls himself and his employees “building geeks.” They like nothing more than to get into buildings and use cutting edge technology to improve its performance, helping make a building safer, healthier, and more sustainable. The Spray Foam Magazine Team (SFMT), spoke with Kaye and asked him, “What exactly a blower door test is and why do spray foam contractors need to be aware of it pre-application?”
Spray Foam Magazine: How did you get started in the industry?
Jamie Kaye: In 2002 I purchased my first home and quickly took to doing renovations. I enjoyed it and was told I had a knack for it, so I got my Residential Builders license in 2004 and started working on historical renovations in Charleston, SC with a focus on changing the build environment. In 2007 my wife and I moved towards Hilton Head Island and shortly after we purchased an old, moldy, and termite-ridden home. I wanted to make it energy efficient, and most importantly healthy. We ripped it down to the studs and did just that. I was fortunate to be working for a contractor at the time who owned an HVAC company too. They designed my HVAC system with a legit load calculation, and they also advised me to put in fresh-air ventilation...no bath fans and only an ERV where it exhausted stale air from the bathrooms while bringing fresh air into the home. The world of building science was opened up to me at that time in my life. It finally answered the why of why we do things in homes, and I was determined to understand how these homes and buildings work.
I had the first blower door test done on Hilton Head Island that wasn't a LEED home and it started my journey in understanding how houses work and the fundamentals of building science and building envelope.
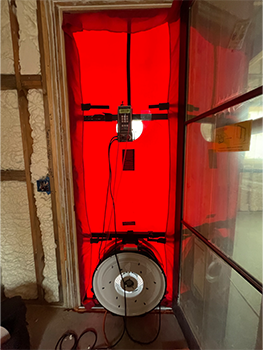
SFM: What does the Elm Energy Group specialize in?
JK: Our roots are in building science which is the interaction of how buildings, materials, and the people in them operate in relationship to the outside environment. We do load calculations to size air conditioning systems for homes, consult on how to build an energy efficient home, or how to fix a home that wasn't built the best from the beginning. We test homes and duct systems. We do air quality testing and moisture intrusion investigations. We are consultants who help owners, builders, architects, and others understand and use building science principles to prevent issues and optimize performance.
SFM: Is a blower door test required by code?
JK: Yes...and no. The requirement for pressure testing has been in the IECC (International Energy Conservation Code) since its 2009 edition, but the implementation has been left up to state and local municipalities. Many states require a blower door test on new homes prior to certificate of occupancy. There is no doubt that in the future this will be more widely adopted, and should be required in every state, but there are still places where you don't need a permit and even places where a code official doesn't exist. Those places can benefit from a blower door test too.
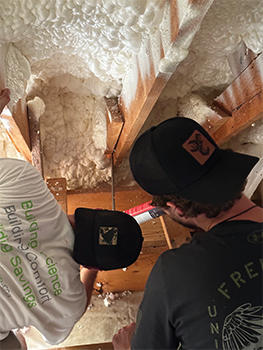
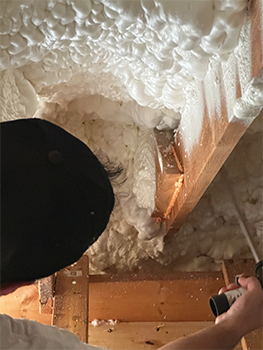
SFM: How long does it take to do a blower door test?
JK: The process of pressurizing a home takes only a couple of minutes. There is a bit of prep prior to testing like closing doors/windows, protecting fireplaces, opening the interior doors, etc. There is also prep that must be done to figure out the volume of the home so we can use that blower door number to determine how tight the home is. The time it takes to analyze a home and inspect it thoroughly is a whole different beast and can be time intensive depending on the use of the testing. If it is just for code, it’s quick.
SFM: What is the cost?
JK: This is something that is subjective to what you are using the blower door for. For example, code compliance only, troubleshooting of problems after foam, or inspecting the foam to ensure there are no voids. The cost for basic testing starts around $250 for a quick test and can be in the $1000's for a deep dive into inspecting the home envelope.
SFM: What does a complete energy evaluation cost?
JK: A true energy assessment whereby we are doing testing, modeling, and reporting to guide you in making improvements and giving you estimates on what to expect in energy savings costs, is a lot more than most want to pay for it. In most cases those consultants charging larger fees are going to add more value and provide greater ROI (Return-On-Investment) since they are probably not 'pencil-whipping' an energy audit and they are focusing on 'your home' which is unique to any other home.
I personally have shied away in the past five to seven years from giving energy saving guidance (meaning we don’t tell people to plan on saving X% of money by doing X...unless it is changing light bulbs or appliances which are an easy enough calculation) and instead we choose to test and understand the unique home and develop a plan to tune that home properly in terms of airtightness, thermal insulation values and HVAC sizing and distribution (which does include the “V” for ventilation)...which is the largest contributor to comfort and energy savings.
If you still have incandescent bulbs, a 25-year-old refrigerator, and an 80% water heater, there are easy ways to save money when those expire. However, doing the improvements on the building shell and the air conditioning is where the largest gains can be derived.
SFM: Will a blower door test help reduce an energy bill?
JK: When you seal the lid of a cooler, your ice remains longer. It’s the same for your home or building. If you seal it up, your conditioned air will not escape as quickly, and you have more control of the contents of that space. If you run a blower door and rubber stamp the test, since it is better than code in my opinion, that is a dereliction of duty and will not save you money. The test is to measure how tight the home is, and it is true that the tighter you seal up your home in winter, the less heat you will lose.
There isn’t any other way to know how tight a home is, and the blower door is the tool to help someone confirm something is sealed, find something that is not sealed, however little or big that hole is/was.
SFM: What are the most common issues found during a blower door test?
JK: Holes in the envelope since that is about its only job. As the blower door sucks air out of the home, new air is brought in at the exact same time. That incoming air comes from windows, doors, fireplaces, exhaust ducts (kitchen, bathroom, dryer vent, etc...), and holes elsewhere in the envelope. There are times we have used the blower door to check window tightness (window leakage) only and there is an ASTM standard for that, but at the end of the day, it is looking for holes in the building. The more holes that are in your cooler, the quicker the contents of that cooler change (hot or cold).
The goal of a good blower door operator should not be to only run a test and get a number, but to know if that number is good or not for that unique home, and if not, to look for why and find the holes!
SFM: What would you say is a common problem area and how can spray foam contractors avoid it from happening?
JK: The most common area we find is leakage at the top plate connection, where soffit air leaks into the sealed attic. This is frequently because of the installer not getting up high enough on the ladder to see the seam or having a poor angle to apply the foam. We think sprayers with open-cell foam will often spray the roof deck and look for the expansion to seal to the top plate...but this is often not the case! Although the best way to address this is to have builders block that soffit area with sheathing at the exterior wall plane (i.e., to prepare for the home for foam) and the foam contractor only must picture frame this area first with a focus on the seams prior to applying thickness throughout. Blocking the soffits that way is not viable on retrofits, so for this we would say to picture frame the blocking the foam contractor installs first...then add the R-value elsewhere. The airseal is most paramount and it seems that visible line of sight is one way to avoid that, but in our opinion, testing a few homes, and seeing the air leaks that are hard to see until you see them, will make all sprayers better applicators!
SFM: Will a blower door test’s pressure have a negative impact on my home?
JK: No, it is a 20mph at most on the home, so just as a 20mph doesn't negatively impact your home, then the blower door won’t either! But the person running the test should understand what happens when putting a home under negative pressure as it can pull combustion gases into the home (so we need to set natural draft water heaters to pilot settings), methane into the home from broken pipes, or dry traps (so we can cover those traps or find those broken pipes), ashes into the home from an open fireplace flue (so we can protect those ashes from negatively impacting your home by cleaning them or covering them). Doing the test only helps you gather data to make the home better.
SFM: What do you find the most that can be easily repaired or fixed to help increase efficiency?
JK: I would say the biggest culprits we find in homes that aren’t foam are ductwork related. To the shock and dismay of most HVAC guys who are not looking at the ductwork first or even a close second. Holes in your ductwork are the biggest opportunities we find to change homes quickly for the lowest cost. Putting the broken ducts back together all the sudden changes comfort, cost, and air quality in the home. It seems simple to most, but it is overlooked almost always.
SFM: When a good spray foam job is completed, what are the typical results you find?
JK: Better control of the way air moves in and out of your home. This results in better comfort and more energy efficiency. This also means you may need some ventilation to help the home remain a healthy indoor space. In terms of tightness...you can’t build it too tight, but you can fail by not ventilating it right. When they build submarines, they don’t leave leaks and say it’s okay and it needs to breathe...they know that it is the people that need to breathe so they build it tight and ventilate it right! There is a reason the Yeti and Yeti-like coolers work better and keep your ice longer...they are airtight! It is that gasket and seal that makes all the difference, not the R-value of the cooler.
SFM: Can you explain how the blower door test has relevance to the HERS Index? (The Home Energy Rating System (HERS) Index is the industry standard by which a home’s energy efficiency is measured. It’s also the nationally recognized system for inspecting and calculating a home’s energy performance.)
JK: The HERS Index is a rating scale that can give you an idea of how your home should perform in terms of 'costs' versus other homes. As with all modeling, it is only as good as the data inputted and the person inputting the data too, but it is a great tool to know more about what you are buying, like the MPG stickers on vehicles. The blower door is just one piece of the data used in the modeling since you can put in great equipment, have solar panels, have foam insulation, and have the best windows in the world, but if the home is leaky (like the cooler) you will lose your contents quickly. The HERS Index scale rates homes and if your home is leaky, it 'should' have a worse rating.
SFM: What is an ICC HERS Specialist?
JK: An ICC HERS Specialist can assist code officials with the parts of the energy code in the International Conservation Code. There is a good bit of education/training required to understand all the nuances of the code and with the code officials being in shortage throughout the country, the ICC and HERS got together to try and open more opportunities for HERS Raters while aiming to help fill the void.
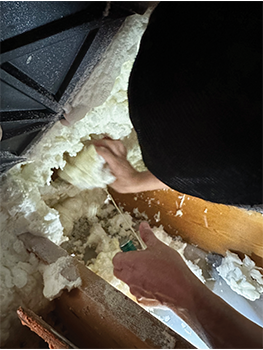
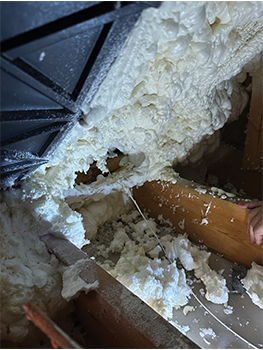
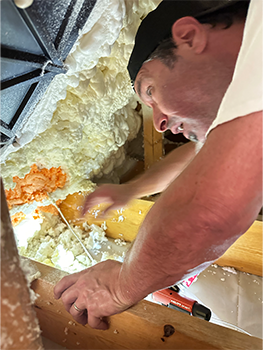
When you were only looking at a fiberglass batt or measuring the thickness of loose-fill fiberglass insulation via a tape measure, that is one thing, but when you are trying to look at all the parts of the energy code and ensure a home complies, that is another.
SFM: Is the blower door test part of The ENERGY STAR certified checklist and how does it help to have a building ENERGY STAR Certified?
JK: Yes, it is part of an ENERGY STAR certification since the HERS Rating is part of the ENERGY STAR certification. ENERGY STAR is one of the most recognized brands, especially in this country...behind say Coke, Nike, and a few others. It's known that if you buy an ENERGY STAR TV, refrigerator, dishwasher, washer/dryer, etc... you are getting a more efficient product. The ENERGY STAR label on homes is the same thing as it should represent a better performing and more efficient home, but it is only as good as the data inputted, the quality of the data gathered, and the quality of the modeling done.
SFM: How will a person know if air sealing is effective?
JK: If the person is doing air sealing because they have a comfort and moisture problem and that problem goes away after air sealing, then it was effective. Think of it like closing a window and your room is more controllable and comfortable after it is closed, meaning that open window was the issue! If you do a blower door test before you do air sealing and then do a test after you do the air sealing, then those results will give you feedback on the amount of air sealing you have completed. This would give you a percentage of improvement, but the question of it being effective is tough since only time will tell unless there is an issue like mold, comfort, stability, etc. which improves after the air sealing is done. There is no question that tighter is better in terms of control.
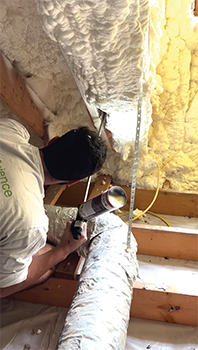
SFM: Anything you would like to say to spray foam installers?
JK: Build it tight and ventilate it right and be passionate about doing good things for the built environment. For those out there doing foam, find someone that does testing. Or go and get certified and test yourself. Test all your home regardless of code. It will make you, and/or your team, better installers. It will help reduce your liability since you will get better and not leave holes in your foam (which you are doing now...guaranteed!). It will help you walk away from buildings you shouldn't foam and help differentiate you in the interim before it becomes the de facto standard. Pressure testing buildings will absolutely help you provide a better product and process. •
Elm Energy Group encounters thousands of performance-related problems in almost every type of dwelling and structure, and by combining their experience and building science knowledge, they really help escalate a home or building’s performance. They use cutting-edge technologies, like infrared, which can pin-point areas of improper insulation, air leakage and moisture intrusion. Showing exactly where problems are occurring while eliminating the guesswork. They also help their clients navigate new energy codes with their building science technicians helping them understand ways they can meet or exceed these requirements, improve their buildings quality, and reduce costly warranty callbacks. With a wealth of building science comprehension, it really is cool to be a geek!
For use by SprayFoamMagazine.com & Spray Foam Magazine