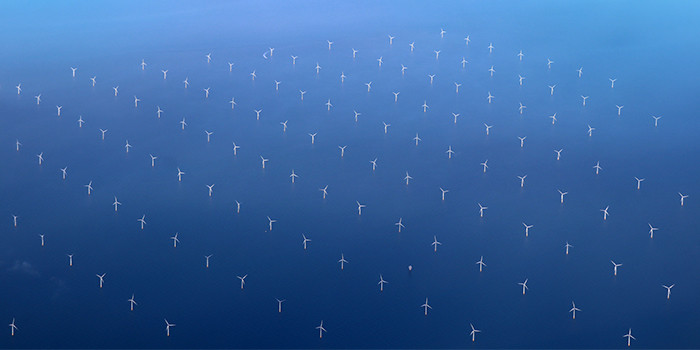
All Is Swell Offshore
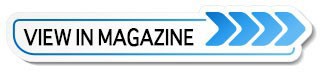
Spray Foam Magazine – Spring 2021 – Corrosion protection provider Krebs Korrosionsschutz GmbH was searching for a polyurea supplier for a new application area: offshore wind turbine foundations. With Teknos as a polyurea supplier, a supportive consulting and training partner came into the picture as well. Starting a large-scale project, especially when using new application techniques, equipment, chemistry and a paint supplier, everything is based on trust and commitment.
Krebs is a German one-stop corrosion protection provider offering comprehensive corrosion prevention, including planning, pre-treatment and coating all the way to logistics services. Established in 1949, Krebs has 70 years’ experience and has grown to a large entity with multiple locations. Krebs is a remarkable partner for the wind energy industry, specializing in offering corrosion protection in offshore environments.
For the upcoming Hornsea 2 offshore wind farm, Krebs will conduct surface treatment for 165 monopiles in Rostock, Germany, along with coating 30 transition pieces in the United Kingdom. The foundations are manufactured by EEW Group, specializing in the production of offshore wind components. According to the project owner Ørsted, Hornsea 2 is expected to be complete in 2022 and it is expected to be the largest offshore wind farm worldwide, powering over 1.3 million homes with green electricity.
Boat Landings Face Rough Conditions
The access to offshore turbines for maintenance and service crew is managed through a boat landing. The boat landing structure is placed on a transition piece which is stacked on the monopile in the offshore foundation design. To safely transfer technicians to turbine premises, service operation vessels connect to the turbines using a gangway system. Also smaller crew transfer vessels provide access to the turbines.
The surface of the boat landing’s docking areas needs to withstand extremely hard mechanical wear and impact, as the strong swell of the sea may cause connecting structures and vessels to rub against the wind turbine foundation.
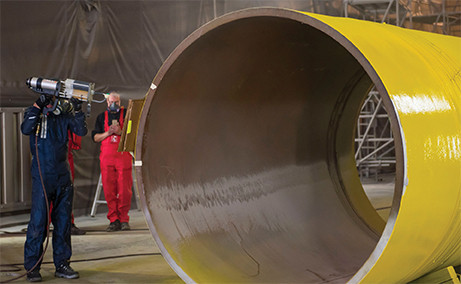
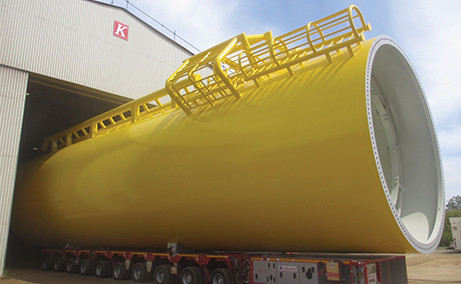
If the paint surface is damaged the risk of corrosion to the structure is increased. The right kind of coating system will protect the structure against damage from both mechanical impact and corrosion. This is vital for a long design life in the harsh offshore splash zone environment.
To tackle the issue, Krebs was in search of a reliable partner for polyurea supply. Polyurea is an ideal coating to protect turbine foundations as it is known for its technical superiority. Being able to stretch even 400 percent of its own size before cracking, it is an extremely durable coating able to protect the underlying paint coats from breaking. Additionally, the coating has another important task to create safety at sea. The polyurea was required to be tinted in RAL 1023 “Traffic Yellow” to match the standard requirements, bringing visibility even in dim and grey conditions.
Krebs needed a partner who could support the training of their painters as polyurea was taken into use for the first time. Spraying polyurea is different and more demanding compared to other coatings. Polyurea has two components that react extremely fast to ensure quick curing, and this requires the right conditions in order to achieve the desired coating properties. Due to quick curing time, measured in seconds, there is no room for application error.
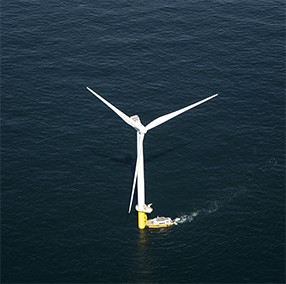
Special Technical Team for the Offshore Polyurea Project
Teknos was brought in as a specialist supplier, and a reliable partner to execute the project where knowhow on polyurea is a key element. Like Krebs, Teknos has comprehensive corrosion protection knowledge gained through 70 years, but from a paint manufacturer’s point of view.
Gathering a winning technical team consisting of polyurea specialists and extensive wind energy experience at Teknos was not a problem. Knowledge of the wind energy industry at Teknos stems from a comprehensive offering of coating solutions for all parts of wind turbines. Regarding polyurea, Teknos has extensive experience not only as a manufacturer but also as an educator.
Two-Day Polyurea Training Locally at Krebs Rostock
After a well performed test painting, the project was kick-started with a two-day, tailored polyurea training session. Teknos Germany’s Polyurea Specialist Robert Kerpen executed the comprehensive training together with Technical Consultant Allan Bonde Jensen, both of whom have a strong background in the wind energy industry.
The training started with theory on polyurea’s special characteristics and behavior, introducing spraying equipment and work safety. Safety is an important topic as the polyurea paint products are heated up to 80°C and sprayed at pressures up to 200 bar. The actual spraying in the training session was conducted on a test dummy version of the real transition piece to ensure as realistic an experience as possible for the applicators. The test dummy was prepared as usual: two coats of high build of epoxy according to Norsok standard, then sanded down for polyurea application.
Application training was conducted with the specially developed yellow polyurea that will be used for coating the end product.
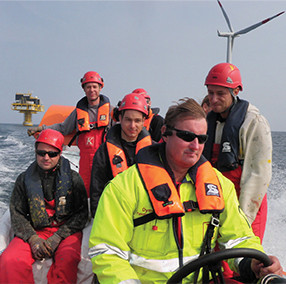
The access to offshore turbines for maintenance and service crew is managed through a boat landing, which is placed on a transition piece stacked on the monopile in the offshore foundation design
In the end, the group went through possible causes of malfunction in spraying and how to resolve them, and the participants were walked through the practice of repair spraying. To conclude, the participants took an exam that granted the Krebs’ painters a certificate as an official Teknos certified polyurea applicator. After the intensive two-day training, the painters were satisfied and felt confident at starting the actual project. Project managers agreed with the team’s opinion.
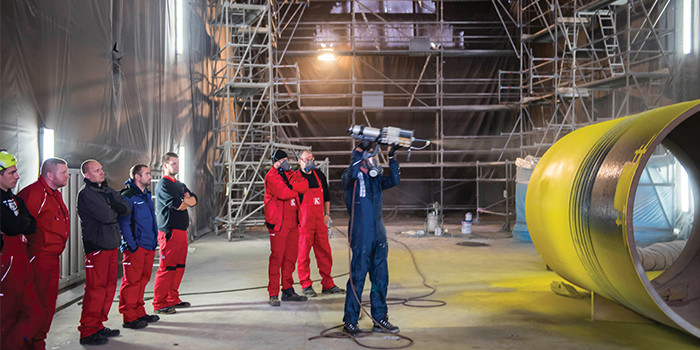
Application training was conducted with the specially developed yellow polyurea that will be used for coating the end product. Participants were walked through the practice of repair spraying.
Finding Reliable, Committed Paint Supplier is Valued
Starting a project, especially in a fully new application area with new chemistry and a new paint supplier, everything is based on trust. Both parties need to have mutual benefits and the enthusiasm to develop. “When selecting a new supplier to bring in a new coating system, everything comes down to trust,” says Krebs CEO Andreas Biermann.
After initial consultation, test painting and training, the cooperation does not end in delivering the polyurea. When the first batches of boat landing pieces were ready at Krebs for coating, the same technical team from Teknos was on site, supporting the initial application of the polyurea.
Deployment of Polyurea Happens by Training and Supporting the Customer at First Time Spraying
At Teknos, we train all our new polyurea customers to excel in all aspects of polyurea usage, including equipment, safety, spraying technique, and troubleshooting. In addition to organizing polyurea training, we normally participate in the first sprayings at the customer site to ensure smooth first deployment of polyurea coating.
Monopile Painting at Krebs Rostock
At the Rostock site, remarkably large objects such as cranes and monopiles for offshore wind turbines are painted.
The cylindrical part of a monopile can have a diameter of 7.5-9.5 metres, they can be 55-67 metres long and weigh up to 1,800 tonnes. As the wind energy industry is expected to grow, increasingly larger turbines are anticipated to be handled in the future.