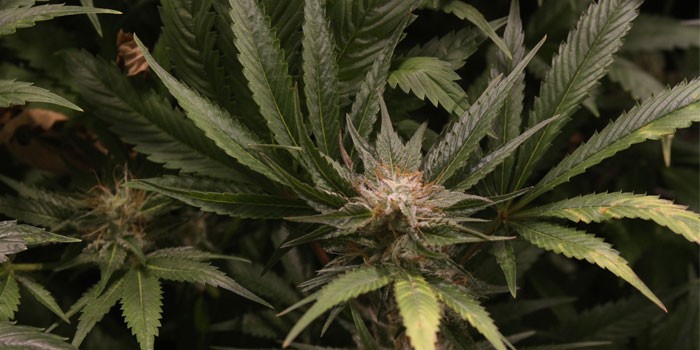
Aiming High with Spray Foam
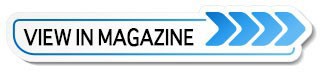
JUPITER, FL – February 1, 2019 — There has been a recent surge in the use of both recreational and medicinal marijuana, with The U.S. Food and Drug Administration (FDA) already approving three cannabinoids for medicinal use. As more states legalize the growing of marijuana and research is carried out into its health properties, the quantity of grow houses are rising drastically. Following this boom, a number of state legislatures are taking steps to endorse marijuana as an agricultural commodity and like any commodity, the crop has to be protected.
Predicted to be a $21-billion-dollar industry by 2021, grow houses are investing in this protection and crop standardization. One way farmers are ensuring their crops are top quality, is to regulate the grow house temperature with a climate controlled facility. The application of spray foam will ensure this happens which in turn will keep heating and cooling costs down for the grower.
Steven Fuhr, a grow house operator, explains the benefits of using spray foam when insulating a grow house. »
During the hottest week of August, we had closed-cell spray foam applied at our grow facility, and went through the process of energy auditing our building.
Spray Foam is worth considering for anybody building a structure to grow, dry or store cannabis (Innovations in Grow-Room Tech).
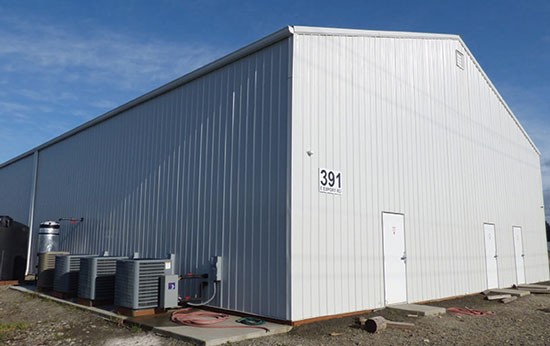
Many grow houses, such as this 5,000 sq. ft. facility in Washington State, are turning to spray foam for its ability to prevent moisture and condensation, which in turn can prevent mold from growing on the marijuana plants.
Photo Provided by Jake Rayl, AT FoamWhat makes this foam insulation so special is its ability to make grow rooms airtight so growers can purchase smaller heating and cooling systems and lower utility expenses. It also features an R-7 per inch insulation capacity. Two or more inches can make a wall resistant to moisture, insects, vermin, mold and mildew.
The bids for spray foam weren’t cheap. By comparison, regular fiberglass R-21 batt insulation would have cost about $15,000 for one 5,000-square-foot building, assuming we blew in R-49 of cellulose on our ceilings as the Washington State Energy Code requires. The average bid for the spray foam was $60,000, while the highest came in at $100,000. Luckily we found a contractor that had a reasonable bid and experience with grow operations. We also found a special provision in the energy code that allowed us to cut the cost by two-thirds.
This special exemption from WSEC was based on our belief that we could use half the insulation required (R-14) and achieve better results than with standard R-21/R-49 insulation. Code would have required we put more than three inches of spray foam on the wall, and more than five inches on the roof (hence the $60,000 cost). We claimed two inches of this special foam was better than six inches of fiberglass because it was airtight. The county building department asked us to prove it before we could receive a variance, so we set out to do just that.
To accomplish this task, we had to conduct an energy insulation audit on our new building (technically referred to as “blower door air leakage testing” and “infrared insulation verification testing”). The audit was cool to watch and also saved us thousands of dollars in insulation to start and thousands of dollars annually in heating costs. The test results earned us the special exemption on our building permits, and helped us created the ultimate grow room.
Energy insulation audits measure two basic things: how efficiently your “thermal envelope” is insulated and how much air escapes it. A building’s thermal envelope consists of all the walls, doors, windows, ceilings, floors and all the cracks in between.
A high-tech, heat-sensing camera is used to measure insulation efficacy, which provides a detailed, multi-colored image. To test a structure’s air leakage, a blower fan with a door-shaped gasket is placed in an open door. When the fan turns on, a special meter measures how much air is escaping through all the leaks in a structure. The theory is that somebody could have walls with three feet of fiberglass that are R-100, but batt insulation does not stop air intrusion. Closed-cell spray foam stops air intrusion and provides a significant insulation factor.
Much like the difficulty we had finding a foam contractor that would work with a cannabis-related business, we also had a hard time finding a certified energy auditor. The local public utility district offers them, but wouldn’t work with a cannabis business. After two weeks of digging, I was finally referred to Brent Foster, of Northwest Infrared, a certified building science thermograph.
Foster came out to the facility on one of the hottest days of the year. By 9 a.m., it was 86 degrees outside, and by the time he was doing his final test, the temperature was headed toward triple digits. His thermal imaging camera operates on the difference between the inside and outside temperature. The south side of our metal siding was 121 degrees Fahrenheit at 9 a.m. By noon, it had surpassed 140 degrees.
We started with the blower door test. This test is so sensitive it can calculate to the square inch how much air is leaking from the structure. Following blower door guidelines from the Washington State Energy Code, our building could leak up to 630 cubic inches of air and still comply with the current energy code. That level of leakage is acceptable for building code, but not for our purposes.
We had just 79 cubic inches of leakage for the entire structure. It was so tight, Foster had to adjust the ring size on the blower door twice. He said he’s never tested a commercial building that tight, and he’s done all sorts of commercial structures. Here’s the kicker—our structure was a standard pole barn and we hadn’t even installed sheet rock or mudded the walls yet, which is how most buildings achieve an airtight seal. Foster said pole barns tend to leak so much air they are difficult to test.
Then the thermal camera came out. As you look at the thermal images, it’s hard to train your brain to realize that red is not the hottest color—white is the hottest of all, with dark blue being the coldest and green being slightly warmer. The lowest temperature in the room, the concrete slab, was 71.6 degrees. The air was about 71 degrees inside, while the foam wall on average measured 72 degrees. Remember, on the opposite side of the wall, it was 120 degrees.
After infrared scanning the room with spray foam, we went to the part of the building that had six inches of fiberglass batt and 17 inches of cellulose insulation in place of closed-cell spray foam.
When we opened the door to that section of the building, the difference was easy to feel. It was almost 76 degrees, and the surface temperatures were in the low-70s to low-80s. The hottest spot was 100 degrees—about 25 degrees warmer than the warmest spot in the foam section. You could also see the air intrusion and cracks in the batt insulation. Hot air poured through as white strips in the infrared image.
Putting Money in the Spray Foam Pot
Hired to undertake this project was AT Foam Insulators owned by Jake Rayl, a family owned and operated business based in Maple Valley, Washington. The company has been in the spray foam industry since 2007.
John Rayl of AT Foam gave Spray Foam Magazine the specifics of this job. It was a 5,000 square foot structure with 80% of it being on the agricultural side. Using two Graco E-30 guns and BASF Spraytite 178 they applied two inches of closed-cell foam to the walls and roof of the agricultural side, encapsulating the building envelope. They also sprayed the metal roof to prevent sweating.
On the non-agricultural side, the processing side, two inches of Spraytite 178 were sprayed to the attic floor. A hybrid insulation process needed to be used on this side for a drop down ceiling to meet the R49 code requirements. To meet that, two inches of foam at R14 and seven inches of blown-in insulation on top of that achieved the desired results.
It took four crewmen and five days to complete the entire job.
Spray foam has many advantages to create the perfect growing environment. It will prevent moisture and condensation preventing mold from possibly growing. When using CO2 for the plants, it will be kept more contained. By keeping temperatures consistent, this will cut the usage of the HVAC system saving the owner money.
AT Foam Insulators has serviced at least 15 grow house jobs, making them the ideal company to complete this job.
Watch the video below to see the installed foam in the facility.
The evidence was clear—the spray foam makes the building so airtight that just two inches of it is better than six inches of fiberglass and 17 inches of cellulose.
The next week Foster prepared his report, which had all the thermal images, data and graphs showing how the building performed. We turned it in to the county building department, and within a few days our exemption request was approved. We proved that less can indeed be more. In the end, we saved more than $30,000 going with spray foam and ended up with a better building.
One last benefit came about as we looked at the report. We were able to see the small anomalies and penetrations in our insulation before putting up sheet rock. These leaks were not visible to the naked eye, but were verifiable in the infrared spectrum. We could see where the fiberglass needed to be re-aligned, where doors needed foam backer rod, or plumbing needed extra caulking. This may have been the biggest benefit of all.
Now it’s time for us to rock on, get the HVAC finished and bring some plants in! —By Steven P. Fuhr (courtesy of Garrett Rudolph Editor of Marijuana Venture) •