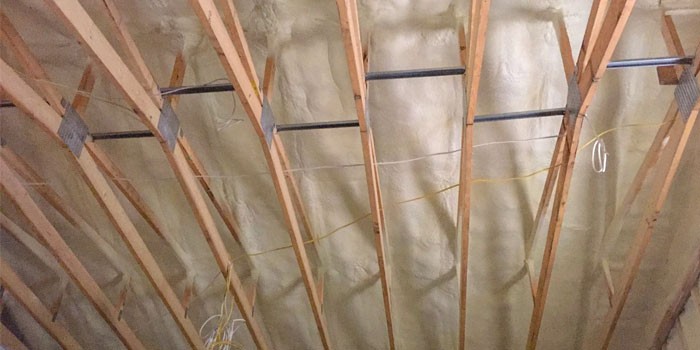
Addressing Moisture and Temperature Concerns in Unvented Attics that Have Spray Foam Insulation
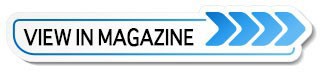
To some, unvented attic construction using spray foam insulation is a fairly new approach in home building. With it, the orientation and type of insulation applied to the top of the building enclosure has changed from the traditional way, and so temperature and moisture conditions experienced by various assembly elements will be impacted. As a result, some in the building industry have experienced concern with this construction approach.
Moisture Concerns
Roof Leaks
The issue of water leakage from the exterior is sometimes raised as a concern. From a design perspective, attic venting is not provided to address roof leaks. The basic design assumption regarding all roofing systems is that the roof system deflects water away from moisture-sensitive materials. If it does not do this, it has failed.
Spray foam insulation performance can offer different ways to address problematic situations:
Open-cell foams will tend to leak closer to the point of water entry making leaks easier to identify and locate. Note that not all open-cell spray foam insulations have the exact same physical properties as some are able to absorb a significant amount of water which could aggravate moisture conditions in an attic.
Closed-celled foams will perform better in terms of deflecting water away from interior element,s but in some cases leaks may go undetected longer. Many have been tested as a water resistive barrier.
Vapor Diffusion
The superior air sealing performance of spray foam insulation, both open- and closed-cell, results in moisture movement by vapor diffusion increasing in importance. Building code vapor retarder requirements for unvented attic construction have been in place since the 2009 IRC and have resulted in thousands of successful assemblies that contain spray foam. Closed-celled foams can meet vapor retarder class II requirements at minimal thicknesses, thereby proving a popular choice in Climate Zones 5 through 8 where such requirements apply. In Climate Zones 1, 2, 3, and 4 the use of open-cell spray foam, with their vapor permeable nature, will allow the drying of roof sheathing and framing as diffusion allows moisture to pass through the spray foam out of sheathing and structural elements.
Lately, discussions related to open-cell spray foam in unvented attics, vapor drives and humidity levels have appeared. It appears that many opinions presented are based on limited building science field research, generalize a complicated building science situation, and doesn’t fully explain the continued successful, long-term performance of spray foam insulated unvented attics in hot climates. There is a significant emphasis on computer simulations in these discussions. The movement of air and moisture in real buildings is a complex and dynamic group of reactions that are difficult, if not impossible, to fully and properly model in a computer analysis.
Some roof assemblies use very vapor impermeable materials such as “peel and stick” membranes to cover the entire roof sheathing exterior. Care should be taken with these assemblies in Cold Climate Zones in that the manufacturers of these materials assume that roof deck may require ventilation to assist drying. If spray foam is used in these climates zones vapor retarder requirements apply, drying to the interior is limited, and a vented space may still be needed directly under the roof deck. In Warm Climate Zones, vapor permeable open cell spray foam would facilitate drying of the assembly to the interior, making a vent space under the roof deck unnecessary.
Air Leakage
For unvented attics, having the spray foam layer applied continuously from the roof/wall intersection to the roof peak, at the specified thickness, encapsulating the entire interior surface area of the attic will hinder airborne moisture entry while providing an energy efficient environment. Coverage gaps could lead to moist outdoor air entry, and since a venting system is not place, higher humidity levels could result. Spray foam installers that have successfully gone through manufacturer or trade-association delivered application training are more likely to deliver the installation needed.
Temperature Concerns
Among the significant issues that get raised pertaining to unvented attics is concern over asphalt shingle temperature/durability in hot climates. Generally, it has been found by researchers that the net impact of eliminating venting is to raise shingle temperatures only by five to eight degrees Fahrenheit. Furthermore, it was found that shingle temperature was affected more severely by factors such as geographic location, roof slope and orientation, and shingle color. The effect on roof sheathing temperatures in unvented attic was similarly shown to be of negligible concern.
But, the lack of understanding of these issues has prompted some manufacturers to reduce or eliminate their warranty on shingles applied to unvented roof assemblies. Were warranties based on scientific evidence, it would be logical that they should also be altered based on geographic location—one should expect to get a different warranty in Las Vegas versus Minneapolis. In any event, a growing number of manufacturers are offering competitive warranties for roofing over unvented attic assemblies recognizing a significant marketing opportunity for their products.
In cold climate locations with significant snowfalls, ice dam formation on roofs is a real concern. The problem is that warm house air can melt the snow on an uninsulated roof when attic venting is blocked. Insulating and providing airtightness with spray foam at the underside of the roof as part of an unvented attic assembly will elevate such concerns.
Spray foam insulation in an unvented attic assembly has been one of the most researched and widely implemented innovations of recent years. Over time, feedback from builders and building owners has been and continues to be overwhelmingly positive, especially in the areas of moisture performance, energy efficiency, and building durability.
*Spray Foam Magazine does not take editorial positions on particular issues; individual contributions to the magazine express the opinions of discrete authors unless explicitly labeled or otherwise stated. The inclusion of a particular piece in the magazine does not mean that individual staff members or editors concur with the editorial positions represented therein.