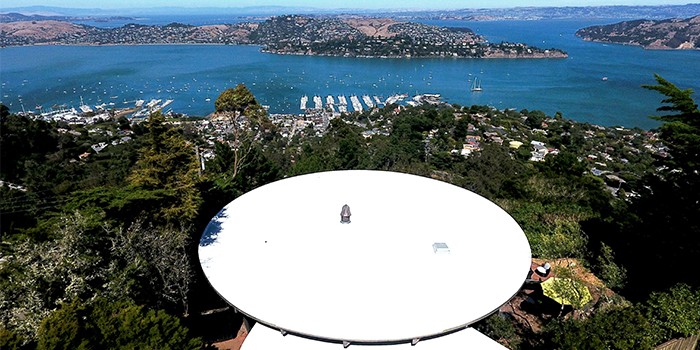
A Well-Rounded System
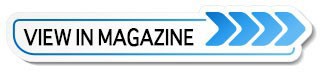
SAUSALITO, CA – March 1, 2018 – Let’s go back in time as early as the 16th century, where the structural design was inspired by the open roundness of Grecian and Roman temples. An Italian architect named Andrea Palladio came to believe that the circle was the perfect figure for building and was superior to the sharp lines of the square or rectangle, and became the first proponent of the “round architecture” movement that has not since expired.
Round structures, however; have gone in and out of mainstream popularity, but there has been a consistent group of “round home converts.” These homeowners gain the benefits of the ability to have wide, open views of nearly everything around them, along with the efficiency of weight-to-strength ratios.
During the post-World War II period, a rejuvenation of round architecture struck the industry with leading architects such as Mario Corbett, Frank Lloyd Wright, and Buckminster Fuller. “Round Homes” became the atomic-age design that offered a futuristic style, yet it was a challenge for builders and contractors due to the circular structure and roofing. The round roofing structure was not durable enough, interior water intrusion would occur, and proper thermal insulation was non-existent.
RELATED Dodge Data & Analytics Unveiled New Research on Performance Management Best Practices at AGC, Recycling and Sustainability of Polyurethanes Explored in Depth at UTECH Europe 2018 Conference, Spray Foam Magazine Turns Focus to the Contractor in Latest Published Issue , Connecting With The Contractors
The home is located above the inlet to the San Fransisco Bay across from the south town of the Golden Gate Bridge in Sausalito, California
These issues were certainly considered during a recent project located in Sausalito, California where a round home towers thousands of feet above the inlet to the San Francisco Bay across from the south town of the Golden Gate Bridge. Built in 1954 by Corbett himself, you can imagine a structure of this sort not only requires technical restoration for the sake of the new home owner, but for American history.
64 years later, the home was in need of repairs to last another lifetime, and with broad sweeping views of 160 degrees, it was not going to be an easy job. Tasked to bridge the structure with the consistency and dependability of contemporary design, Wedge Roofing (WR), a Bay Area-based roofing specialist, stepped in.
The project took place during the winter amidst daily 20-30 knot winds and thick fog. A blanket of clouds coupled with the wettest rain season that the area has experienced in some 50 years posed a challenge to the WR team prior to spraying. Yet with a construction schedule dependent upon their work, they researched and devised a plan of action prior to the application in order to efficiently complete the job within an allotted deadline of three days.
After collaborating with technical industry experts, working with the latest weather software provided by GAF AccuWeather, and creating a ramp out of standard spray shields that that are designed to reduce wind speed, the WR team made a plan to create a calm zone. Utilizing the velocity of the wind to move over the slanted ramp, they would be able to create a dead air space behind it that would be acceptable for spraying.
“Nothing happens without the correct weather window, even a very brief one. First analyzing the NOAA’s GOES (Geostationary Operational Environmental Satellite) West images, careful observation of the Jetstream, and input from local weather stations meant that an anticipated start date eight days away was greenlit. This gave us the better part of three days to complete the project and seven days of preparation to make sure our plan would work,” explains Gary Harvey, general manager of Wedge Roofing.
RELATED Rise Up, Insulating A Castle, Greater Than Gold, What It Takes To Run A Successful Contracting Business
Once this three-day window was open, the nine man WR crew wasted no time. First, they began prepping the site by removing the perimeter metal from the 3,200 square-foot roof and secured the existing built up membrane with mechanical fasteners to provide an additional wind uplift protection layer prior to foam installation.
With a foggy, windy climate to work in, the WR team had short windows of time to spray
Spraying from noon to 3PM each day (it was the only time of the day that the fog would subside due to the 30 mph winds), the WR crew was divided up with a sprayer and helper at each gun and one mechanic on the ground to support the two rigs WR brought on site. Using Graco E-30 proportioners, a Graco Fusion AP, and a Graco D-Gun, the crew applied to the perimeter of the roof 1.5 inches of Everest Systems’ Evercell 3.0, 2.7 lb. closed-cell foam. The foam expanded into a seamless roofing membrane.
Also present were three crewmembers responsible for finding a safe location for the fastener and relocation of the spray shields, and, finally, a standby member on the roof for safety precaution due to the harsh and quick-to-change environment. Because the crewmembers were 800 feet above ground while applying the foam, they were secured with fall protection harnesses and retractable lanyards for the perimeter work. All of the crewmembers dressed in full Tyvek suits, 3M half-face masks with particulate and charcoal filters, and eye protection.
Once the foam had cured, the WR team applied a 22 mil coat of GE Enduris 3500 white silicone roof coating. After the first layer, the crew hand rolled an additional layer of the silicone coating while broadcasting a half-gallon of Lucas Fire White granules to provide reflective properties for a cool roofing system.
The home was first built for Marin County Real Estate Developer Walter Benson and his family. He and his wife are pictured (below) hosting a 1959-era party
“The project looked magnificent,” notes Harvey. “With a new roof, it would make it impervious to moisture infiltration for decades to come and the owners were awestruck at Wedge’s ability to spray in such conditions. With the insulation quality, air-sealing benefits, wind-uplift rating, as well as no fasteners and seams that spray foam offers, they considered it to be one of the major thermal upgrades they’ve seen.”
Although the process was not a tranquil one, the WR team was proud to be standing upon living history that they had helped preserve. Through creating a securely waterproofed, thermally insulated, and aesthetically pleasing roofing system, it is one that Mario Corbett himself would be proud of for decades to come.