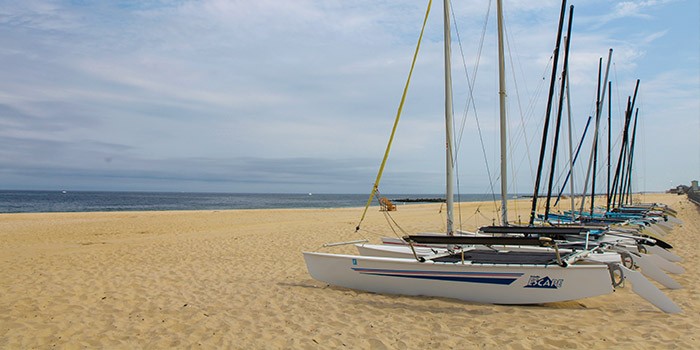
A Safe Bet in Lavallette
LAVALETTE, NJ – June 29, 2018 – It’s been a few years since Hurricane Sandy mercilessly tore through the Jersey Shore and left many crumbling structures in its wake, but that doesn’t mean that the area stopped being a desirable place to visit and live, which is why a great portion of these damaged homes have already been rebuilt and more structures have been added. In the borough of Lavalette, which was one of the areas where most damages occurred, a recently constructed, energy-efficient home on stilts by the ocean is another testament of said rebirth. This is the “dream home in the dream location” of New Jersey resident Sherry Vivenzio and her husband; it is where she wanted to live despite the past disastrous event.
And what’s not to like? Lavalette is home to nine protected picturesque ocean beaches that offer swimming, surfing, kitesurfing, fishing, sailing, and boating. Along the shoreline and further inland, there are opportunities for rollerblading, tennis, bocce, shuffleboard, live music and concert-going, and many other activities to suit all tastes. When you add beachside living with the right kind of entertainment, you understand that Vivenzio’s idea of a perfect location is not far off from most of yours. Living in Lavallette means watching the crowds roll in in the summer and then experiencing mostly peace and quiet the rest of the year with the exception of a few potent sea breezes—and Vivenzio wanted to keep it that way year-round, as well as have an ideal indoor climate through the summer and the winter while keeping energy costs down. That’s why she requested that her home be insulated with open-cell spray polyurethane foam (SPF) insulation.
“I wanted to make our home as energy-efficient and as quiet as possible,” notes Vivenzio. “There was no doubt foam insulation was the way to go!”
The Vivenzio’s home is located approximately 100 feet from the water. They requested spray foam as the insulation material to obtain sound deadening and indoor comfort.
The project involved a collaboration between system house Icynene-Lapolla and Foam Tight Insulation, Inc. (FTI), a contractor specializing in SPF applications. FTI became certified to use Icynene’s Classic Ultra, the latest technology in half-pound, open-cell SPF technology. This product features improved sprayability and consistent yield, as well as introduces Icynene-Lapolla Draw Mixer, an innovative expanding blade mixer that eliminates the need of pre-spray hand mixing. The certification was made possible by way of Damian Lardieri, dealer development manager for Icynene-Lapolla, who played a part in the product demonstration, FTI’s Classic Ultra certification, and the ordering of the product. Not only did Lardieri help out with the qualification process for the contracting company, he also aligned the project and personally introduced Stan Betts, president of FTI, to Vivenzio. Lardieri also oversaw the installation onsite to make sure that the FTI crew understood the ins and outs of the product.
“It was a successful link that led to a well-executed project,” says Lardieri. “I’m hoping I can participate in many future projects and help promote our top-of-the-line products.”
An additional benefit that the Classic Ultra SPF provided was that it could be applied at varying temperatures, with drum temperatures only needing to be at 70ºF for an optimal installation. A three-man FTI crew completed this application during the winter of 2018, and since there was no heat in the home when they arrived on site, using the Classic Ultra proved to be efficient.
“We didn’t need to heat our drums constantly to apply the foam and we didn’t have to use heaters against the substrate,” explains Betts. “This foam system allowed us to go through the job in a smooth manner without needing to heat the building. It’s a tenacious product that adhered perfectly to the plywood substrate.”
The crew insulated the home with Icynene’s Classic Ultra open-cell SPF. They applied it to the exterior walls of both floors of the home, as well the underside roof of the first and second floor.
The FTI crew arrived to the home in Lavalette in a truck-mounted rig that was equipped with a PMC PHX-40 hydraulic proportioner, PMC AP-2 spray guns, and 300 feet of hose. The application of SPF to the 3,000 square-foot home that was located approximately 100 feet from the water consisted of insulating the exterior walls of the first and second floor, the attic, and the underside of the first floor.
Before any foam came out of their AP-2’s, the FTI crew applied a polyurethane foam sealant around the windows and door frames and made sure to staple one-mil plastic sheeting around these openings, masked off light fixtures in the ceiling of both floors, and laid tarps to cover the ground between floors to reduce overspray damage. They also set up Baker scaffolding between each floor to reach the higher areas of the walls and rooflines.
FTI started at the bottom of the home and applied eight inches of foam to the underside of the roof of the first floor, which consisted of a two-car garage and a utility room. The water piping and plumbing system of the home was located in that utility room, so it was specified that the interior walls be insulated with closed-cell foam to create a moisture barrier. For that particular area, the FTI crew applied two inches of Icynene’s MD-C-200, a 2 lb. closed-cell SPF. Approximately 10 gallons of closed-cell foam were installed for that entire portion of the home. Then, the crew moved to the main living areas.
“We have experienced our home holding the heat extremely well and even with our high wind location the house feels solid and quiet.”
Betts explains that the application varied in depth between floors because the first floor had two-by-four exterior walls, whereas the second floor had two-by-six exterior walls, so to accommodate the different structural sizes, 3.5 inches of open-cell foam were installed between the studs of the first floor walls and 4.5 inches were installed to the second floor walls. The FTI crew then applied eight inches of foam to the underside of the roof to complete a thermal envelope for the home. Foam in place, the crew used a foam trimmer to shave off the excess foam and make the material flush with the studs. A total of three sets of open-cell SPF was installed to the home. Because the foam was later covered with drywall, no ignition or thermal barrier coating was required. While installing, the three FTI crewmembers wore coveralls, full-face respirators, face masks, gloves, and boots—and they completed the application in just under a week.
“Spray foam is a green product that is going to help the homeowners save a lot of money on utilities and keep the home nice and quiet at the same time,” says Betts.
And as far as Vivenzio and her husband are concerned, she is now convinced that she made the right choice in SPF. She moved in during the last days of winter and mentioned that the high level of coziness is a result of the insulation.
“We have experienced our home holding the heat extremely well and even with our high wind location the house feels solid and quiet,” points out Vivenzio.
Her vision of the ideal home has been realized, thanks in great part to SPF.
For more information, visit www.icynene-lapolla.com and www.foamtight.com.