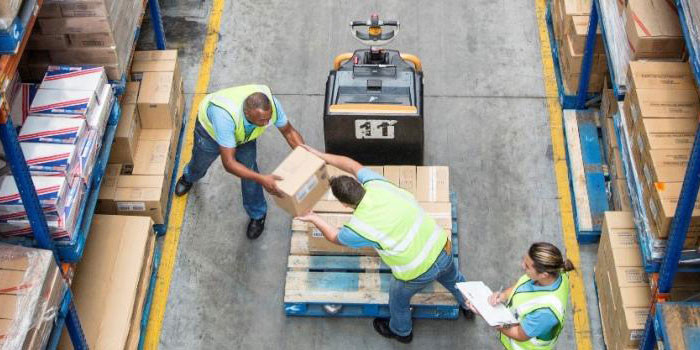
3M Has Ramped Up Mask Production
St. Paul, Minnesota - March 19, 2020 - During the COVID-19 outbreak, we’re working to help those affected around the world, putting a priority on the safety of our people and the public.
That’s because 3Mers across the globe are on the front lines, maintaining operations and producing needed supplies to help others treat and help protect people in the face of a pandemic.
“We are responding to the rapidly changing COVID-19 outbreak by providing supplies where they are needed the most, and I am incredibly proud of the work our people are doing to support the public health and government response to the outbreak,” said Mike Roman, 3M chairman and chief executive officer.
In addition to working to ensure that our supply chains hold up to global demand for products like respirators, surgical masks and commercial cleaning solutions, we’ve taken steps to make sure our employees can lead safe and productive lives during the outbreak. This week, we’ve initiated a remote working policy, a pandemic paid leave policy and a COVID-19 clearinghouse site for our people.
We are also supporting public health and government response to the outbreak by ramping up production at our global manufacturing facilities, including hiring workers, adding shifts and activating more production lines.
As global demand for personal protective equipment continues to outpace supplies, we will work with customers, distributors, and government and medical officials to help get supplies where they are most needed.
The best way we can do that is to keep our people safe.
Keeping our people safe and business running
This week, we instituted a paid pandemic leave policy, giving our U.S. employees up to two weeks of paid leave if they are unable to work due to caregiving, childcare or self-quarantining related to the COVID-19 outbreak. We have also provided new direction for how we’ll continue to work together to keep our people healthy and sustain 3M’s U.S. operations safely.
Beginning now and continuing through the end of March, this includes:
- Escalating procedures in all U.S. factories related to personal safety, cleaning and medical screening measures.
- Encouraging as many corporate employees who can effectively work from home to do so as much as possible, while making plans for longer-term remote work, as needed.
- Committing to cover 100% of the cost of COVID-19 screening tests, as well as the costs of office visits or urgent care visits incurred to receive the test, for 3Mers enrolled in a 3M medical plan.
We are closely monitoring how the spread of the virus is affecting our employees and business operations. We have developed preparedness plans to help protect the safety of employees around the world while safely continuing business.
Early on, we restricted international travel that was not deemed business critical and supplied employees with information on precautionary steps they could take to help prevent the spread of the coronavirus – as well as the actions they should take if they become ill.
“As we face this crisis together, we will remain focused on the well-being of our employees, our customers and the public,” Mike said. “And we will continue to be guided by our legacy of applying science and the expertise of our people to confront the challenges facing the world, including the coronavirus.”
Producing product where it’s needed
We continue to manufacture needed products in multiple areas around the world, including in the United States and China, as well as in Latin America, Europe and Asia. Our manufacturing model emphasizes local for local. For example, the majority of our products made in the United States are sold in the United States.
At our Aberdeen, South Dakota plant, Tim Hofer stood in front of a production line that was turning out thousands of 3M N95 respirators. The plant was running around the clock in response to the coronavirus outbreak – and the resulting global demand for respirators.
“We know what we have to do, we know we need to keep our numbers up, we know we need to keep ourselves safe, and we need to put out great quality,” said Tim, a machine operator. “And that’s what we’ve come here to do.”
While 3M manufactures millions of respirators per month at its production facilities, we expect demand for respirators and other supplies to outpace supply for the foreseeable future.
“We are committed to balanced distribution of our products that both supports the response to COVID-19 and ensures product availability to our existing industrial and healthcare customers who rely on our products,” Mike said. “Unfortunately, with the evolving situation, more of our production capacity must be dedicated to supplying healthcare and government/emergency response. We have notified our authorized distributors that we are prioritizing orders to help serve our base business – including hospitals – due to high global demand.”
While we have not changed the prices we charge for 3M respirators as a result of the coronavirus outbreak, we cannot control the prices other dealers or retailers charge.
As this situation continues, we are closely monitoring and responding to any potential impact to our broader supply chain. Serving our customers is a top priority and our business teams are working diligently to communicate with individual customers about any potential disruptions.
Learn more
Organizations and individuals seeking to support the response in China can reach out to 3M Global Security Operations Center at globsecopscenter@mmm.com.
For more information about respirators and the outbreak, please see 3M's Worker Health & Safety page on the coronavirus.
This is an evolving situation, and it is recommended that all concerned individuals consult the World Health Organization and the CDC websites frequently for the most updated information regarding the outbreak.
3M recommends customers only purchase 3M respirators from 3M authorized distributors or dealers to help ensure their authenticity. Customers concerned about potential fraudulent or counterfeit activity should contact us using our Report a Concern website.